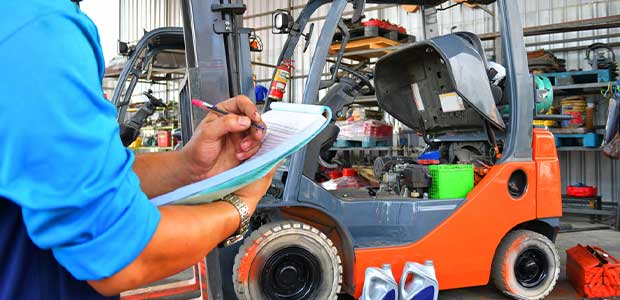
Everything You Need to Know About Forklift Safety
Understanding forklift safety could save lives.
- By Alex Saurman
- Sep 01, 2022
Walk into any warehouse, construction site or dock and you’ll likely see a forklift. These tools are used in workplaces all over the country and by a variety of workers. Although you can find multiple types of forklifts on the market or in the workplace, most of them share one common goal—to help workers move heavy items from one spot to another.
In a warehouse, a forklift might be used to move a pallet of items off a high shelf to a lower, workable area. On a construction site, a forklift might carry heavy timber to where the workers need it. And forklifts can also be used to load and unload items off and onto other vehicles, like a ship.
The use of forklifts is so common that in 2019, more than 1.4 million forklifts were sold globally. It’s also estimated that there are over 1.5 million forklift operators in the U.S. alone.
With forklifts being such a common tool and so many people using them, just how dangerous are they? Well, statistics show that they can be very dangerous. According to the Bureau of Labor Statistics, just over 9,000 workers were injured from forklifts in 2017. That same year, 74 workers died from injuries involving forklifts. Those workers needed an average of 13 days away from work.
Hazards Present
When working on or near forklifts, there are many hazards that can result in injury or illness. If a load is not balanced, rollovers can happen, leading to driver injury. If there are edges in the workplace, a driver can accidentally drive off of one. In 2017, the most common type of incident that led to nonfatal and fatal injury or illness was “non-roadway incidents involving motorized land vehicles.”
Pedestrians walking near a forklift are also at risk for injury. In 2017, 1,850 pedestrians were injured by forklifts. On average, the workers needed 20 days away from work.
There are a variety of factors that go into forklift incidents. According to the Canadian Center for Occupational Health and Safety, some of these are contributed to potential operator error, like driving too fast, not turning correctly or improper parking. The load can contribute to an incident as well. When items are not stacked well or the load is too heavy, this can have consequences on the driver and people around the forklift. Other factors like improper operator training and mechanical conditions can also lead to avoidable incidents.
Besides the consequences of potential OSHA citations, there are other financial costs when forklift incidents occur. The National Safety Council estimates that the average direct costs for these incidents is $38,000. For indirect costs, the average is $150,000. That means companies can be out thousands of dollars following one forklift incident.
Employers also need to factor in the cost of lost work. Forklift incidents lead to a median of 13 days away from work for workers. Forklift operators may also hit other items in the area, leading to costly repairs.
Forklift incidents can clearly cost employers a lot of money. So, how can you mitigate the risks associated with forklifts?
Mitigating Risks
One way companies can reduce the number of forklift incidents is to have workers who are fully trained in operating forklifts. Just like being hired for a job, you need to make sure your worker is qualified to work. Forklift operators must complete training and evaluations as outlined in OSHA standard 1910.178I1. These trainings include formal instruction, practical training and an evaluation.
The training must cover a variety of topics, like engine or motor operation, vehicle inspection and maintenance that the operator will be required to perform, operating limitations, surface conditions, pedestrian traffic and ramps. Because there are a few different types of forklifts, workers should be trained on whatever tool they will be using.
Every three years, forklift operators should also be reevaluated. A reevaluation may be required before that if the operator shows what OSHA labels a “deficiency in the safe operation of the truck.”
It should also be noted that by federal law, no one under the age of 18 is allowed to operate a forklift.
In addition to ensuring that your forklift operators are up-to-date on evaluations and training, you can also keep your workers safe with forklift inspections.
If a forklift is not suitable to perform its job, it can have potentially harmful effects on the operator and other workers. Inspections must be performed on a daily, pre-shift basis. Checklists for these inspections are often provided by the manufacturer. Some companies have provided tools that digitize the process. If an item is found to malfunction or be inoperable, the forklift should be removed from service and sent to be fixed.
Only authorized personnel should perform the repairs needed on the forklift, and they must adhere to guidelines when making these repairs. For example, if a part of the forklift needs to be replaced, the new parts need to be “equivalent as to safety with those used in the original design,” OSHA says.
The third way to avoid the risk of forklift hazards is to protect workers, both on and off the forklift. There are changes employers can make to their facilities to improve the health and safety of forklift operators.
Safe Environments. Employers should ensure that operators have a safe environment to drive the forklift in. Hazards like blind corners or items blocking the path can result in an incident. Forklifts can also be too big for the area they’re designed to work in. In this case, employers should take precautions to purchase the correct size forklift.
Pedestrian Safety. If pedestrians are walking in the same area as the forklift is operating, and keeping the two separate is unavoidable, there are steps you can take to mitigate worker injury. Designated walkways for pedestrians or forklift drivers ensure that everyone is where they are supposed to be. They should be well marked and well lit, with nothing blocking the path. Make sure pedestrians know to make eye contact with the forklift operator so they are aware of the location of the person on foot. No one other than the operator should be on the forklift. Horseplay and giving other people a ride are not safe.
Practice Best Use. Forklift operators should also take precautions themselves. Every operator should follow the speed limit and the weight limit of the load for their vehicle. Make sure the load of the forklift is balanced and not blocking the vision of the driver. If a load is unbalanced, this can result in the load falling off or tipping the forklift over. Wearing a seatbelt is another great way to ensure workers stay safe in the event of a rollover.
At the end of the day, an employer's job is to keep workers safe. Forklift safety applies to more than just the forklift operator itself. It applies to everyone.
This article originally appeared in the September 1, 2022 issue of Occupational Health & Safety.