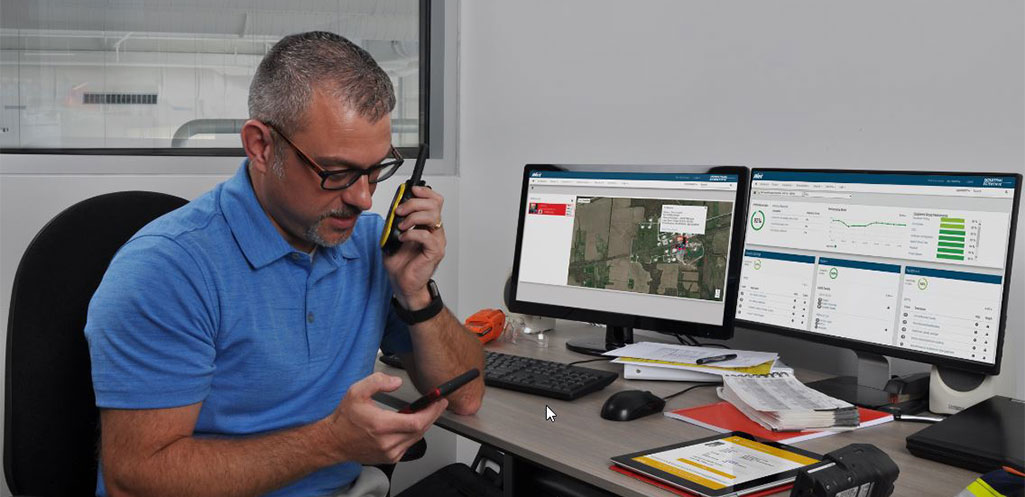
SPONSORED
Take Worker Safety to the Next Level with Live Monitoring Solutions
When it comes to safety in industrial environments, real-time connectivity through connected, live monitoring safety solutions is key.
Safety managers have seen how new technologies, tools, and strategies can reduce downtime and boost operational efficiencies, and in 2019 alone, spent more than $400 million on connected safety solutions.
Of course, linking a workforce through connected safety tools like live monitoring and peer-to-peer sharing won’t eliminate gas hazards. Rather, connected safety can be used to better monitor gas hazards on a facility-wide scale so both workers and safety managers can make informed decisions.
Although using connected safety technology to connect teams has huge advantages, the concept may still feel overwhelming for some. Wireless, wearable gas detectors are a great starting point because they incorporate connectivity into safety equipment your workers already use.
Connected Safety for Everyone
Connected safety solutions function effectively in multiple settings, including the harsh industrial environments found at manufacturing plants, mines, oil and gas production sites, and hazardous material storage locations. But what does connected safety look like? Some examples include:
- Teams receive automatic alerts for when conditions become unsafe – giving them the information they need to act in the moment and reduce second guessing.
- Safety managers use connected gas monitors and software to see where workers are located in an emergency, who’s safe and who isn’t, and as a way to make informed decisions.
- Industrial hygienists remotely monitor perimeters after a gas explosion to minimize the impact on neighboring communities.
- Turnaround planners use connected devices to monitor contractors and learn from their patterns of behavior, which helps with future planning.
Keeping Lone Workers in the Loop
Connectivity and live-monitoring solutions can be used across multiple applications – ranging from lone workers and emergency response to confined spaces and more – and are critical in ensuring that recording and sharing gas readings amongst team members is an easy, automatic process.
Lone workers, for example, are often doing their jobs in remote locations, 20 or more miles from the next sign of life. Safety managers, meanwhile, are often responsible for keeping track of the lone worker. In either case, your day-to-day work can be extra challenging if a problem arises. If a lone worker faces danger on the job, it could be hours or days before help is able to make it to their location. Because of this, it’s important to maintain safe habits while on the job. One safe habit to conduct is regular check-ins.
Manual check-ins occur when a lone worker makes a phone or radio call on a set schedule to report his or her status to a supervisor or team. This gives the safety manager the chance to receive updates on a worker’s whereabouts and health status. If a lone worker misses a scheduled check-in call, you would dispatch help to their location.
However, manual check-ins are time consuming and can be unreliable. Lone workers in a remote location may not have cell signal at the site, forcing them to drive several minutes away to find a cell signal and check in. Forgetful employees may have to be tracked down by a supervisor. This lost productivity can be a big deal. As a worker, you may consider these check-ins to be disruptive. From a safety standpoint, these check-ins are crucial.
Connected, wearable gas monitors eliminate the need for manual check-ins by automatically providing status alerts to safety contacts through live monitoring software. A wearable gas monitor allows the worker to move freely and to do their job without thinking about the device. At the same time, the device sends status information back to you through a cellular, satellite or wi-fi connection. This serves as a reminder to both the lone worker and the safety team that the worker is safe.
Staying Safe in Confined Spaces
In other applications, such as confined spaces, keeping your entire team informed with gas readings continues to be simple. Entrants inside the space carrying a gas detector enabled with peer-to-peer connectivity will share their readings with a connected area monitor or personal gas detector stationed with the attendant outside the space, allowing them to “see” the readings and monitor the atmosphere through each of the entrants’ instruments.
Seeing the gas readings within a confined space is not just convenient, it saves lives. You’ve probably heard confined space horror stories like this a million times: the person inside of a confined space becomes unresponsive. The attendant responsible for monitoring the work goes into the confined space to check on his partner and is overcome by the same deadly gas. It’s a tragic story of trying to help a co-worker based on gut reaction rather than proper safety protocols. According to OSHA, these would-be rescuers make up 60 percent of confined space fatalities.
But with shared data on gas hazards, the attendant watching the hole in this example would have known what caused his partner to become unresponsive without being exposed firsthand. He could then take appropriate steps to rescue his peer, without putting himself in danger.
On top of that, the repeating capabilities of instruments in the mesh network allow workers go deep within a confined space, away from the entrance, where they could never be seen directly. Even in these locations, they can still communicate atmospheric readings back to the entrance of the space with the help of peer-to-peer wireless technology.
With this increased flexibility, peer-to-peer wireless technology in gas detectors is expanding the role of the attendant in confined space entry. One attendant is typically assigned to monitor the entrance of every confined space, however, wirelessly sharing gas readings allows one attendant to monitor the activities of multiple confined space entrants from a central vantage point in real time.
Connectivity is Key
When it comes to wearable devices, connectivity is important. If a worker loses connectivity, they lose the benefits of a wearable device. This means that the gas detection device isn’t communicating or sharing information about the worker back to the rest of the team. Suddenly, nobody is watching the worker’s back. This means safety teams can’t respond to incidents in real time and operations people lose visibility into worker productivity.
Workers at every level suffer if everyone isn’t staying in touch and connected.
Wearable devices can help workers avoid potentially dangerous or life-threatening situations. By sharing data and information out to teammates and supervisors, these devices can have a positive impact even in the most hazardous situations.
When paired with the right live monitoring software solution, you can rest assured that your team has the necessary information to respond quickly and effectively in an emergency. Outside of emergency situations, you can also boost productivity with real-time visibility into worker and site conditions, as well as drive proactive safety improvements by identifying high-risk areas with visual summaries of gas alarms by type, location, user, and more.