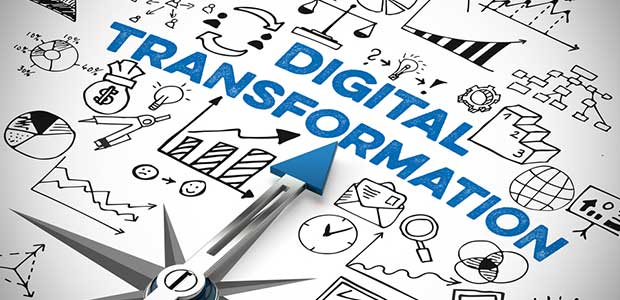
How Digital Transformation Reduces Safety Risks on Jobsites
While safety has always been the top priority in construction, it is often compartmentalized.
- By David Brian Ward
- Mar 01, 2022
Digital transformation is changing how safety is managed on jobsites. If the term digital transformation is familiar, but not clear, here is a refresher. Digital transformation is about using technology to improve business processes, company culture and customer experiences. Extending this to safety, digital transformation also reduces risks and compliance costs and improves productivity. It does this by streamlining and/or eliminating time-consuming processes and administrative tasks, identifying potential safety risks at the office or jobsite and providing the data and insight necessary for general contractors to make more strategic decisions about their business and each construction project.
While safety has always been the top priority in construction, it is often compartmentalized. It is common to see the safety officer conduct routine inspections and audits to identify and address potential risks and observe workers to ensure they are following protocols. However, safety is only practiced by workers not imposed by consulting engineers. Separating out safety can create an uncomfortable environment for the safety officer and colleagues, potentially impacting productivity as workers feel they are being monitored. In turn, this can foster adversarial relationships. Yet to be effective, safety is everyone’s job and requires continuous learning and collaboration.
Digital transformation can help if safety practices are no longer a drag on productivity and if digital transformation empowers everybody on the jobsite to play a more active role in ensuring safety. Digital does not eliminate the need for a safety officer, although it will reduce the overall workload. Rather, it highlights how technology can make it easier to prioritize and follow safety guidelines, especially onsite, further reducing risks while raising profits.
Four Obstacles Holding Back Digital Transformation
The benefits of digital transformation have been proven across many industries, yet construction is among the last to adopt it. That is not to say the industry is not aware of the proliferation of new technology on jobsites. Just look at the rise in innovative solutions such as digital apps, jobsite management platforms, virtual reality, robots, sensors and drones all contributing to the creation of the connected jobsite. Yet, not every new technology leads to a company's digital transformation.
While digital transformation holds a lot of promise for construction, here are some of the most common obstacles and how to address them.
Cultural. Digital transformation is not just about the use of technology. Its success hinges on a cultural shift in the company, led by the CEO or construction business owner and embraced by the entire organization, including the trades and subcontractors. Lately, while headquarters increasingly relies on software, little other than timecard entry occurs at the site, where safety data is almost entirely paper based. When digital transformation and its emphasis on improving safety is led by the company, it has a higher likelihood of success.
Lack of strategy. Any investment in technology must map to the company’s larger goals. Most contractors acquired software to solve particular, narrow, point-wise problems. The result is a large portfolio of technology solutions that don’t talk to each other, don’t share data, or duplicate each other. This makes more work, increases costs and is counter to achieving the benefits of digital transformation. Some frustrated GCs are even exploring scrapping their entire IT portfolio and starting from scratch. Contractors need a plan that builds to a digital platform and eliminates duplication. Don’t purchase any technology that doesn’t support the plan or obfuscates your view into the business.
Cost. Along with the upfront cost of the technology, you also need to factor in hidden costs including employee training and ongoing maintenance. Before you buy, find out if you’ll have to hire additional staff or add more work to your IT resource. When determining the actual cost, you also need to analyze the savings gained through more efficient processes, greater productivity and fewer risks, all resulting in more profitable construction projects.
Ease of use. While every technology vendor touts ease of use, employees need to be able to quickly master the solution and actually enjoy using it. If workers find the technology difficult to use, they will abandon it. If management doesn’t see an immediate ROI, they will drop the technology. The standard should be “consumer usable,” not like complex back-office enterprise apps requiring weeks of training. Ease of use means you’ll realize value faster. Complexity and insistence on rarely used features that will cost you in the long run.
The technologies driving digital transformation should be easy to use, affordable, deliver a quick ROI and work with other technologies in your company. Make sure they present a big picture view of the business and allow managers to drill down into the details of every jobsite.
How Safety Apps Accelerate Digital Transformation
Safety apps are an emerging subcategory in digital transformation and BIM. As a critical part of jobsite safety, these apps can provide actionable insights that increase efficiencies, reduce risks and drive profitability.
Many of the original safety solutions were developed to address common documentation-driven worksite and jobsite issues related to compliance and OSHA regulations. They make auditing easier but often don’t offer additional value across the company.
Recently, a new generation of jobsite safety apps have emerged as a result of the pandemic. Digital check in was introduced as a way to streamline health screenings while keeping worker data private. Along with providing a faster way to mitigate the risk from the potential spread of COVID-19 on jobsites, these apps made it clear that it was time to retire the dated and time consuming paper-based process for workers and subcontractors to sign into jobsites, and it saves money immediately.
By digitizing the check-in process, GCs get additional insight into their businesses that would have otherwise been overlooked. They can more easily reconcile timesheets, reduce admin previously spent rekeying handwritten daily log data and reduce idle time on jobsites as clipboards are no longer passed around for workers and subcontractors to sign in (usually illegibly). Project management software actual vs plan can even be updated automatically.
Other digital safety examples include: Safe equipment handling, hazardous materials handling, tool talk presentation and attendance, safe onboarding of new hires, crew communications and alerts, unsafe condition observations, incident reports, etc. All these processes can be performed more efficiently and with better recordkeeping when digital.
When these safety apps are easy to use, they become part of the everyday jobsite protocol. This is a subtle yet important example of how to introduce a new digitally-driven safety process in a non-threatening way.
As part of a connected jobsite, safety apps have evolved to offer many additional features beyond pandemic risk mitigation. Most basic, they provide real-time insight into who is on site and what they are doing. The transparency and automated data collection provides greater visibility into the jobsite and worker activity. The related data offers insight into worker trends, inefficient processes and potential safety risks. This makes it easier for GCs to manage workers and subcontractors and document their skills, projects and progress.
Going a step further, when safety app data is integrated into a company’s project management platform, it provides an additional level of insight that informs critical decisions. Ultimately, safety integrates into the “big data” that will leverage AI and machine learning to raise construction productivity.
According to Rod Courtney, health, safety and environment (HSE) manager at Ampirical Solutions, “Using a site safety app helps us manage the employee and visitor sign-in process, document vaccination status, and streamline the daily log and weekly reports. This allows us to identify potential productivity or profitability issues well in advance of their impact on the project’s success.” Ampirical, an electrical infrastructure, engineering, design and construction firm was named America’s safest company in 2021 by EHS.
Evaluating the Effectiveness of Digital Technology
Digital transformation is an iterative process and one that does not have a set end date because it’s helping to continuously improve how a company is managed. However, the commitment to it does need to be measured. Here is how to evaluate the effectiveness of digital technology and its impact on critical roles across the organization and on the jobsite.
Executives. Look for the ways it minimizes risks and maximizes profit. For example, does it provide executives with data and insight that helps them spot trends and potential risks before they cut into a project’s profitability? How has the adoption of digital technology contributed to more profitable projects, lower insurance rates and lower jobsite incidents.
Site superintendent. Can it decrease or replace time consuming or administrative intensive tasks such as handwriting sign-in sheets and completing daily logs that are later rekeyed back at the office? Does it make it easier to manage workers and especially subcontractors by knowing when they arrived, where they’re assigned and how much time a project required to complete.
Safety manager. How does the technology make it easier to spot and address potential jobsite risks. These risks include workers and subcontractors not being sufficiently trained, not complying with employer, state or federal guidelines or mandates and proper digital documentation of the jobsite and project. One of the most important innovations to emerge from digital technology is the ability to always know who is or was on a jobsite.
Project Manager. In what ways does the technology align with the project plan? For example, does it make it easy to get a bigger picture view into the status of the project, to know it is on track and/or can the technology uncover insights that will impact the project’s profitability.
Human Resources. Can the technology securely and privately address the often unreported or under-reported issues on a jobsite. These can include ensuring workers and subcontractors are properly onboard by showing training videos, for example. Also, does it make it easier to document hours worked, capture digital signatures to ensure workers read and understand compliance documents and be able to upload images and text from the jobsite to create digital records that may be vital in the future (compliance, legal record keeping, etc).
Digital transformation holds a lot of promise and opportunity for GCs to boost safety and drive more profitable projects. When each function of the organization has insight into what is happening on the jobsite, they can improve the performance of their team and make more strategic decisions. The transparency also makes for a stronger organization and creates better relationships with clients and other critical third parties, such as insurance brokers, property managers, compliance officers, attorneys and local municipalities.
This article originally appeared in the March 1, 2022 issue of Occupational Health & Safety.