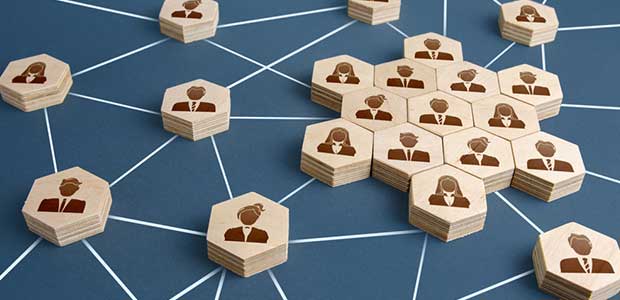
How Connectivity is Leading the Future of PPE and Creating Adaptable, Proactive Safety Programs
Advanced technologies are making it possible for safety managers to better connect workers, worksites and workflows for safer, more efficient work environments.
- By Chris Borneo
- Mar 01, 2022
Want to know what makes one safety program more proactive than another? It’s simple: Having access to meaningful data-- which data is collected, how it’s collected, how it’s disseminated, who analyzes it and when can determine how proactive your safety program is. That’s because every single data point has the power to inform decisions that can literally change your workplace safety and, perhaps, save a life.
What Is Meaningful Data?
Meaningful data is information that is relevant to a given situation. It’s information that helps in identifying risks, as well as mitigating them. More importantly, it’s information that promotes employee well-being and worker safety.
Organizations that understand the importance of it know that meaningful data is:
- Accessible: readily retrieved and easily visualized by those who need it
- Accurate: reliable in informing and supporting decision making
- Automatic: routinely identified and collected, which simplifies recordkeeping and reduces the potential for human error
- Applicable: goes beyond the factual and is specific to the user or situation
- Actionable: enables insight and clarity for swift and proactive decision making
Where Does Meaningful Data Come From?
If you think about it, critical data points come from – and have an impact on – three primary sources: (1) workers, (2) worksites and (3) workflows.
Data points for workers include such things as PPE compliance, productivity and incidents. Worksite data points provide information about the jobsite, including location, working conditions and potential hazards. Workflow data points include PPE readiness, device assignment and management and reporting and recordkeeping.
In the world of safer gas detection, these data points, if they’re meaningful, will translate answers to such fundamental questions as these:
- At the start of the workday, is the PPE ready to use?
- At the end of the workday, did the worker use the assigned device for the entire shift?
- Throughout the workday, what, if anything, happened that needs to be explored, investigated, mitigated or resolved?
Traditional PPE offers limited awareness and little in the way of answers to those questions. Also, traditional PPE is fraught with the potential for human error, often making even the most basic compliance a challenge.
A connected safety program, on the other hand, reliably and accurately answers those questions and helps safety managers create a more transformational, proactive safety culture.
Connectivity: What It Is, Why It’s Important
Like other technological innovations, connectivity is a capability that facilitates transparency, drives commitment to a common cause and enables people to learn what they otherwise might not.
Safety Programs Deserve to Have This Capability. Think about it. Millions of workplace injuries, the costs associated with them and untold productivity losses happen every year simply because organizations don’t have the ability to incorporate technology-based solutions that can help prevent these issues.
What’s surprising is that we live in a world where our phones can start a car while we stay warm inside our comfy house, change the temperature on our thermostat while we’re away or ensure that a loved one arrives at their intended destination, yet we haven’t been able to apply these same technologies to the world of safety.
There’s been a reported 2.8 million workplace injuries and illness as recently as 2019, and an estimated 80 to 90 percent of those attributed to human error—all because safety technology was left in the dark. That is, until now.
Advanced technologies are proving their capacity for reducing the potential for human error, which may explain why industries, such as oil & gas, chemical production and construction are expected to lead the way in terms of adopting connected worker technologies within the next two decades.
This is good news for safety-focused organizations. Why? Because connectivity will connect workers, worksites and workflows so that safety managers can anticipate need, safeguard personnel and respond to situations more quickly and confidently than ever before.
What Is Connected PPE?
While traditional PPE protects the wearer, it does not have the ability to enable real-time visibility across workers and worksites; nor can it provide data that leads to insights and trends that can be used to influence worker behavior. Additionally, as demands on workers and safety managers escalate, conventional methods and processes for recordkeeping and maintenance have demonstrated how prone they are to human errors, ranging from inconsistencies to incompletions to inaccuracies.
Successful integration of a connected work solution means that workers, worksites,and workflows are seamlessly connected. What that looks like is a complete system comprised of:
- Hardware: Smart devices that can perform out-of-the-box with cellular connectivity to the cloud and with the durability and functionality required to protect the worker
- Software: Solutions that support remote monitoring, reporting, and enhanced site safety
- Cloud: Equipment status, asset information, data logs, and centralized reports all in one place
This model of worker-worksite-workflow connectivity is what can transform traditional PPE devices into a data-driven, future-forward solution.
The Connected Work Model
Here’s a closer look at the worker-worksite-workflow model and how integrating connectivity into your safety program can help your organization become more proactive.
Connected Workers. Enhanced awareness and visibility can help reduce safety risks by answering key questions, such as: What’s happening? Where is it happening? Is what’s going on a true emergency or a false alarm?
While traditional PPE is good for protecting the wearer, it doesn’t have the ability to enable real-time visibility across workers and worksites; nor can it provide meaningful data that can help safety managers identify trends and influence safety-first worker behaviors. With connected workers, on the other hand, safety managers gain visibility into:
- Worker location, gas readings and alarms
- Whether the worker is compliant in using the device
- If the worker is engaged in faulty safety behaviors, such as turning an instrument off or changing settings
- In-the-field safety behaviors that may indicate a need for additional training
Connected Worksites. As safety professionals know, it can be difficult to difficult to manage a fleet of assets across a variety of work locations, while also keeping teams productive. Connectivity helps ease the burden with automatic data collection and real-time monitoring – even in unmanned locations and confined spaces. Connected worksites give safety managers greater visibility into:
- Teams, including worker positions and activities
- Assets, including device maintenance schedules
- External or environmental factors, such as temperature and humidity
- Intelligent mapping and zone segmentation, automated digital follow-ups, alarm sharing, and heat mapping to help drive operation-wide safety
Connected Workflows. With traditional PPE and methodologies and the increased demands on workers and safety managers, manual recordkeeping and maintenance processes are prone to inconsistencies and incompletions.
Connectivity, on the other hand, is key to resolving that issue. Take, for example, gas detectors. Local and federal regulations (and perhaps company policies), often require organizations to log and keep calibration and bump-test records. But keeping the fleet compliant with a hands-on, pen-and-paper or even spreadsheet-style recordkeeping process is not only tedious, it also often proves to be an administrative nightmare.
Connected workflows give safety professionals the data and insights they need to improve safety, as well as streamline compliance and productivity. This kind of visibility can allow organizations to:
- Automate compliance
- Decrease false alarms
- Reduce asset-related risks
- Lower the cost of downtime
- Determine if instruments were correctly configured and compliant in testing and while in use
- Generate comprehensive reports in an industry standard format
Proactive Safety
Connected workers, worksites and workflows can empower leaders to create adaptable, proactive safety programs and improve operational efficiencies. Connected solutions can help build and promote an organizational culture of safety in a way that traditional PPE can never do.
This article originally appeared in the March 1, 2022 issue of Occupational Health & Safety.