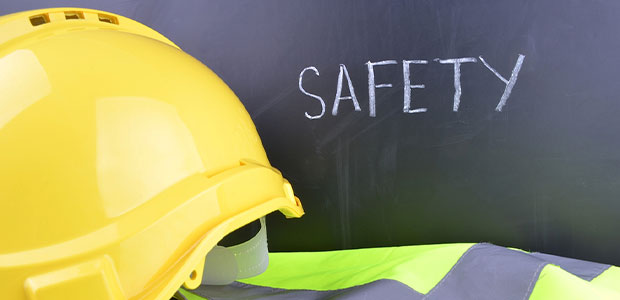
Quarterbacking Safety When Nobody Takes Charge
- By Darren Lottes
- Nov 19, 2021
Every diligent safety manager preaches to his or her coworkers about the importance of speaking up when they anticipate or see danger on the job. Dangerous conditions don’t always strike like lightning, sometimes they move like a shadow. At either end of the spectrum, the hope is that well-trained crews will alert their boss. What happens, though, when your business partners on a project don’t have the experience (or training) to stop work as a situation evolves from safe to dangerous?
Earlier this year, a general contractor was repairing and replacing large swaths of concrete at a private luxury condominium’s four-level, parking garage in a major city. Two of the structure’s four parking levels were below grade. An engineering firm hired the contractor who in turn subcontracted our company to paint walls and stairwells and stripe parking spaces in the garage.
My work as an OSHA certified trainer and an OSHA confined space trainer includes teaching crews not only about on-the-job hazards but also about the importance of creating a culture of safety. When we engage crews in training, the preference is to teach in-person, so we can read the expressions on the students’ face. We want to see if they’re absorbing the material and understanding the finer points of workplace safety. Safety instructors have a responsibility to know their audience and structure training to suit students. For instance, during our company’s OSHA 10 classes, we talk about cranes because OSHA requires that. But our crews don’t use cranes and are very rarely around cranes, so we keep that section to about 10 minutes in length—a synopsis. We use the extra time, nearly two hours, to discuss, for example, fall protection because that’s critical for our crews. Our crews know we tailor training for them, and they embrace the courses.
A False Sense of Safety
At the project’s pre-construction meeting, one of our safety team members inspected the particulars of the job site including elements such as access points, lighting and ventilation. Everything was in order, and we began work. Our crews initially worked alongside the contractor’s crews on the garage’s above-grade levels one and two, without incident.
Within days of our crews moving below grade to the garage’s third level, our foreman called me while I was traveling to another city to say he sensed a problem. By way of background, the general contractor we were working for was using skid steer loaders and other heavy equipment to break up concrete in certain areas of the garage. Our foreman saw dust and fumes gradually accumulating; some of his crew members’ eyes were beginning to water, and they left the area to be in a safer location. My first question concerned the functioning of the garage’s ventilating shafts and blowers. Our foreman said the units were no longer working, and we immediately made the call to get everyone out—our crews and the contractors’. Once our foreman had cleared the garage, he returned with a four-gas monitor for detecting oxygen, hydrogen sulfide, carbon monoxide and lower explosive levels of combustible gases. As he descended through the garage’s third level, the CO detector fired off an alert. We instantly asked for a meeting between the contractor’s site supervisor and engineering project manager. We met on site and learned the contractors’ crews had been complaining among themselves about the conditions. As we investigated the ventilation system on each level, we found some of the contractors’ crew members had boarded up the ventilation shaft openings because the air handlers weren’t working; they thought covering the ventilation grates would help protect the stalled equipment from being coated with concrete dust.
Without the ventilators properly working, we had to treat the job site as a non-permit confined space. Most confined spaces are designated as such, but because this was a parking garage it wasn’t dubbed a confined space. And there were no hazards until the contractor introduced the heavy equipment. Apart from this job, our crews regularly perform work inside industrial tanks, which are confined spaces. In those situations, we begin our safety reviews and discussion up to three weeks before sending a crew into a confined space. Despite my experience as an OSHA trainer for confined spaces, I hadn’t seen a situation transform itself so fluidly and unchecked as the one in this condo’s garage.
Coordinating a Response
We took the lead and asked the contractor to rent a dozen, large industrial fans and remove the barriers from the ventilation shafts. We positioned half the fans to push air from the upper levels of the garage downward, while placing the other half of the fans to move air up through the ventilation shafts. This pulled the dust and fumes out of the work area. Within 45 minutes, our four-gas monitors showed we had a safe work environment. Our foreman and crew discerned the speed at which things were turning for the worse and prevented injuries, perhaps worse. By quickly coordinating and collaborating with the general contractor (who had no experience working in a confined space) and the engineering project lead, we added several recommendations to improve conditions, safeguard everyone, and keep the project on schedule.
Our recommendations included splitting the concrete repairs and painting work into two shifts. The contractor took the day shift, and our paint crews on the two subgrade levels worked second shift, beginning at 3:00 p.m. This kept our crews away from the dust and fumes and made it safer for the contractor to maneuver its vehicles without added workers in the space. We also added a crew member as a safety monitor to regularly check the ventilation system and monitor the atmosphere. Had this project been a public garage there might have been more oversight from the outset. But because it was a private facility, our crew, although a subcontractor, began quarterbacking the safety for this job because nobody else had our qualifications.
With the situation we encountered in the garage, our crew relied on its training. Our foreman had received competent person level training and was able to identify the rapidly changing conditions. Due to the general contractor’s inexperience, its crew was unmindful to the safety issues, until our foreman halted work. Safety always matters, and this situation proved someone with training has to take charge to prevent injury. Training triggers action and the confidence to speak up. At every tailgate meeting, pre-job meeting, stand-down or while working, safety managers and foreman owe it to their crews to empower them to speak out and use their stop-work authority. Success comes from making sure crews and general foreman have the knowledge to spot and understand a developing situation and crews knowing managers trust their decision-making. What reinforces the second point is a safety manager’s reaction when called regardless of the place and time. When a call or text comes in, a safety manager must make the query a top priority, which shows crew member’s we practice what we preach.