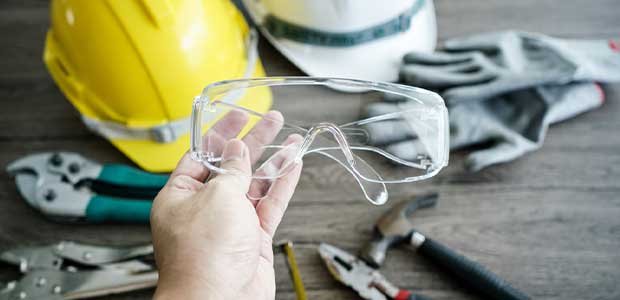
Seeing 20/20: Creating a Vision Protection Program that Works
Understanding why workers aren’t wearing their vision protection will help identify program gaps.
- By Sydny Shepard
- Jun 01, 2021
Seeing clearly is one of the most important abilities employees can have when navigating the work environment safety. If vision is compromised by distortion or fog, workers may not be able to see the hazards in front of them. Distorted vision could result in slips, trips or falls, while fogged lens could lead a worker to take their safety glasses off entirely, leaving the eyes vulnerable to flying objects.
According to the Bureau of Labor Statistics, there were 18,630 cases of injuries to the eyes in 2019 that involved days away from work. In nearly all of these cases, better vision protection programs could have prevented an eye injury. Programs that take a workers’ feedback into consideration will ultimately have a higher rate of compliance.
Assessing the Hazards
The first step in ensuring compliance with your vision protection program is to assess the hazards present in your work environment. According to the CDC, there are three main types of eye injuries that may occur.
Striking or scraping.
Most eye injuries are a result of small partials or objects striking or scraping the eye. These materials could be dust, cement chips, metal slivers or wood chips, that are often ejected by tools, windblown or fall from a worker above. Workers could also suffer eye injuries from larger objects that may strike the eye or face, or a worker may run into an object causing blunt-force trauma to the eye ball or the eye socket.
Penetration. Objects like nails, staples or slivers of wood or metal can go through the eyeball resulting in permanent loss of vision.
Chemical or thermal burns. Industrial chambers or cleaning products are common causes of chemical burns to one or both eyes. Thermal burns to the eye also occur, often among welders. These burns routinely damage workers’ eyes and the surrounding tissues.
The Hierarchy of Controls calls for safety managers and directors to try to eliminate hazards that could cause damage to a worker’s eyes. In doing so, worksites can effectively erase the need for your workers to have to wear any kind of vision protection. Elimination, however, could prove difficult in some environments where flying objects, penetration or chemical exposure is unavoidable.
When elimination no longer becomes a viable way to protect workers, employees must rely on personal protective equipment such as safety glasses, face shields or goggles.
Common Complaints
As with any PPE, safety gear will only work if the employee is regularly wearing it correctly. As in the case of vision protection, there are several reasons why a worker may decide to take off his or her safety glasses, or leave them at home entirely.
Lack of Comfort. One common reason why you might find a worker without their vision protection is the lack of comfort the safety glasses provide. If the vision protection is not properly fitted, the worker may find that it pinches their nose or puts pressure on their ears. If a worker finds that their vision protection is not comfortable, they may take off their gear, leaving their eyes vulnerable to flying objects or penetration.
Fogged Lenses. With the emergence of face coverings due to the COVID-19 pandemic, there was a spike in the number of workers having to deal with fogged lenses. This happens when warm breath escapes through the top of a face covering or mask, causing a temperature change and a layer of fog to settle on the lenses. Understandably so, this makes it hard for a worker to see what they are doing, or the hazards around them, leading to even more opportunities for injury.
Headaches. After hours on the job, eyes may become strained or fatigued. This may lead to the worker suffering headaches on the job. In an attempt to ease the pain, many workers decide to take off their safety glasses opening them up to even more severe eye injuries.
Appearance. As with other types of PPE, such as protective apparel or footwear, appearance sometimes matters to the worker. If employees do not like the way they look in their safety gear, they might decide to take them off whenever they feel they are not in the area of a hazard. This lax approach to wearing PPE could prove harmful if the worker forgets to put them back on before entering a hazardous area.
If you notice a worker not wearing their safety gear, ask them why. It is important to note why workers are having difficulties with their gear and work with them to ensure their issues are covered moving forward.
Tips for Ensuring Compliance
There are many things that safety directors, managers and leadership can do to ensure that employees are adhering to a vision protection program. These include education, an understanding of the workers’ environment, a lead-by-example approach and proper care of vision protection equipment.
Education. Education is a huge part of mitigating hazards present in any work environment. When workers do not entirely understand the injuries they could face if not properly wearing their PPE, then they may become slack in their approach to safety. Be sure to regularly alert employees of the reasons why they are wearing their vision protection and be there for them if they have any questions about the hazards they face.
Environment. It is important to note the environment in which an employee is working to ensure they are provided with the right kind of vision protection. For instance, if the worker is mainly found in an outdoor worksite where the sun may become an issue, safety managers might want to consider vision protection that includes polarized safety sunglasses, which come readily available with scratch-resistant and/or fog-resistant coatings.
Proper Care. For the sake of the wearer’s eyesight and budgetary reasons, it is important to train workers to properly care for their safety gear. As with any other kind of PPE, there are limitations to how long it can be used and in what condition. When workers understand how to properly clean and store their safety glasses, they will generally last longer. Workers should also be training to know when their vision protection is no longer functional.
Leadership. Safety directors, managers and leadership should make it a point to wear the same safety gear that their employees are. This helps the collective approach to safety, as it signifies an “all in this together,” type of safety culture. When employees see their leaders leading by example, they are only more inclined to stay in compliance with their vision protection program.
Open for Discussion
No matter what PPE you are introducing to your worksite, organizations should be sure to create an atmosphere where workers feel comfortable providing feedback on their experience with the gear chosen for them. Or, if you are allowing workers a stipend to purchase their own PPE, be sure that the lines of communication are open with them so they feel like they can ask questions on the proper PPE for the hazards they face at work.
In the case of vision protection, there is much to consider, but when a company has a strong safety culture where employees and leadership alike are part of the safety process, the overall compliance of the worksite rises leading to more protection and less injuries.
This article originally appeared in the June 1, 2021 issue of Occupational Health & Safety.