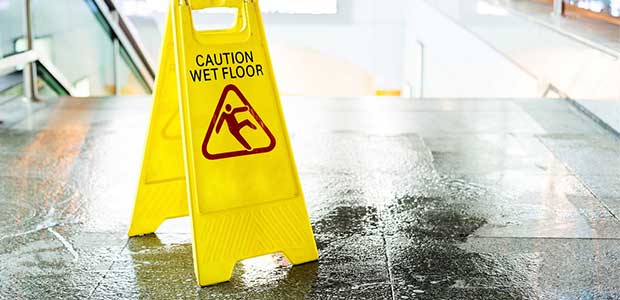
Building a Comprehensive Floor Safety Strategy
Floor disinfection is a safety routine that often falls into the background, but with the ongoing presence of COVID-19, it is extremely important.
- By Patrick Kehoe
- Mar 01, 2021
The way people work changed tremendously in the year 2020. Employees in many industries discovered they could be just as productive working virtually as they were in the office. However, some industries, such as the manufacturing industry, simply can’t function in a virtual environment. Most industrial workplaces, which often play a critical role in the supply chain, have stayed open during the COVID-19 pandemic, creating a new challenge for safety directors and facility managers alike to keep their workers safe.
Priorities have shifted from the typical facility cleaning and safety protocols and procedures to now also protecting employees from a new danger: COVID-19. Disinfection and safety measures have become more important than ever before, and that starts from the ground up—with the floors.
Dedication to Disinfection
While disinfection efforts have always been important, remaining diligent is more important than ever. While you’ve likely been using disinfectants on high-touch surfaces like doorknobs and desks, floor disinfection is sometimes overlooked as an essential part of a facility cleaning plan. As one of your largest high-touch surfaces, it is essential to be proactive in preventing the spread of harmful pathogens that can congregate on floors.
Before starting your floor disinfection process, thorough dusting should be done to trap, collect and discard dirt, dust and debris that has traveled into the facility. It is important to make sure your dusting tools actually trap dust and don’t just redistribute debris elsewhere.
After the dust is cleared, a disinfectant should be applied to the floors and other high-touch surfaces. Paying close attention to disinfectant labels is important to make sure you not only select the right disinfectant for your surface type, but also that you are abiding by the correct dwell time. While allowing a disinfectant to sit wet on the surface for the required dwell time is essential for proper disinfection, a wet floor could potentially lead to another sort of danger to be cautious of: slips, trips and falls.
Mitigating Slips, Trips and Falls
According to the Consumer Product Safety Commission, floors and flooring materials contribute directly to more than two million fall injuries per year. In an industrial workplace, in particular, slips, trips and falls are the second most common workplace injury, costing employers around $70 billion annually, or about $22,800 per incident. In an environment where workers move around quickly, it is especially important for safety directors and facility teams to ensure proper protocol is in place for mitigating and addressing spills and accidents that may occur.
One simple protocol that should be in place is to complete thorough safety walks frequently. Safety directors should check their building, systems and equipment often, while paying special attention to floor conditions in high-traffic areas of the building, including the front entryway, lobby, aisles and hallways, stairs, restrooms and loading docks. When thinking about floor safety, facility teams should consider the following:
- Current floor conditions. Are there missing, chipped or cracked floor tiles? Are carpeting, mats and slip-resistant treads worn-out?
- Climate. Keep in mind the climate of your facility location. Will snow and ice get tracked in? Where are puddles most likely to form when it rains or when snow melts?
- Past incidents. Is there a specific area in your facility where slips, trips and falls tend to happen most frequently, such as a shallow step, a crack in the sidewalk or a slippery metal loading dock?
Proper Products
After the audit is completed, facility managers should develop a plan to combat risks before accidents occur. A comprehensive plan should include floor protection products as well as cleaning and disinfecting tools. Make sure you have the proper products in place for your floor safety demands, including:
- Slip-resistant tapes and treads. Place slip-resistant tape in heavy traffic areas within your workplace, such as stairs and loading docks, to ensure employee safety. In an industrial environment, ultra-heavy-duty tape is recommended. Extra-large minerals allow for a slip-resistant finish regardless of water, oil or other materials it may come in contact with.
- Matting systems. Floor mats both inside and outside of doorways remove and trap dirt, water and debris before it can be tracked into the facility. It is important for facility managers to pinpoint the areas where the most dirt and debris is entering the facility and to place their mats accordingly.
- Sorbents. Sorbents come in many different variations, some to be used on aggressive and hazardous liquids, while some are designed to be used on simple water spills. It is essential to be prepared for anything in an industrial workplace, which is why chemical sorbents are a good investment to allow safe cleaning of hazardous chemicals.
- Cleaners and disinfectants. Finding products that allow facilities to remain safely open without disrupting proper workflow is no easy task. It is important to have products for general surface cleaning and floor maintenance, as well as disinfectants to prevent the spread of pathogens. In light of COVID-19, you should look to use EPA approved disinfectants with a SARS-CoV-2, the virus the causes COVID-19, efficacy claim.
While it is essential to stock your floor safety arsenal with tapes, mats, sorbents and disinfectants, it is equally as important to build a culture of health and safety in the workplace. To achieve a safe environment, training is key. Employees should be properly educated about potentially hazardous chemicals and procedures present in their workplace. When employees know what to look for, they will be able to continually watch for unsafe and unhealthy practices. In many facilities, COVID-19 has required employees who may not have ever been responsible for cleaning and disinfection efforts to keep their spaces clean and safe. Making sure employees understand how to use cleaning products and disinfectants appropriately, such as abiding by the proper dwell time, as well as safely, such as wearing the appropriate PPE when using, is more important than ever.
Keeping employees safe is a complicated process that requires strategy and planning. 2020 was a year unlike any other. If we’ve learned anything, it’s that maintaining the health and safety of employees must be prioritized and planned for in 2021.
This article originally appeared in the March 2021 issue of Occupational Health & Safety.