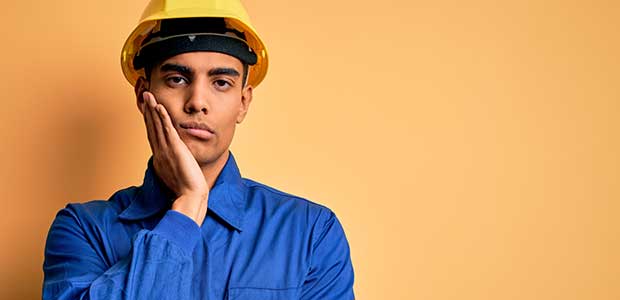
Managing Complacency
Issues stemming from complacency will decrease if an organization creates a culture that embraces enterprise-wide risk management.
- By Peter Furst
- Feb 17, 2021
The dictionary defines complacency as "a feeling of self-satisfaction especially when accompanied by a lack of awareness of actual pending trouble, deficiencies or controversy." Psychologists hold that complacency might result from that is known as "confirmation bias", which is the tendency to look for, or interpret information in a way that conforms with one’s currently held beliefs. This could apply to the workforce, supervision or management when they assess the competence, capability or motivation of other persons or groups, with deficiencies attributed to complacency.
This phenomenon may be reflected in how a person evaluates their own actions or how others evaluate those same actions. This is especially common with people who deviate from accepted practice, take risk, or shortcuts, in order to accomplish goals or objectives without experiencing any negative outcomes. These people are lulled into risk taking believing that an adverse event just “won’t happen to them.” Alternately a supervisor may attribute fault (complacency) to a worker for a failure, immaterial of the actual reason or cause.
Signs of Complacency
There are many underlying reasons for employee complacency which managers and supervisors should be looking for in order to try and control its inevitable adverse effect. One sure sign of complacency is when employees stop being actively engaged in their work, stop solving problems, work cooperatively in moving the project’s goals forward, or work hard at their tasks. When employees lose their passion and do just enough to get by. As a result, they become unproductive, and their attitude invariably affects the whole crew. This results in the employees’ failure to add value to the operations and ultimately negatively impact the organization.
Employee disengagement can also stop them from being thorough, detail oriented and over time they become lazy. Their action becomes disruptive to the work culture and a liability to operations. Workers lose their incentive to further their careers and organizational goals. Some of this may be the result of work that is repetitive and unchallenging. Some of this may be attributed to the fact that the employees do not see any potential for growth or promotion. Rightly, or wrongly, employees may perceive that playing it safe is in their best interest rather than being an active team member. These are strong warning signs that they are physically present but mentally absent in their work.
Risks Associated with Complacency
Complacency has many negative outcomes that are injurious to the organization. Take Deep Water Horizon, for example, the president’s commission reported that the root cause of this disaster was the result of a culture of complacency throughout the organization. The two NASA shuttle explosions is another classic example of complacency. In these cases, and many others information was not shared, warnings from staff ignored, risks were underestimated, and discounted, resulting in a general lack of concern associated with the risks involved and its acceptance.
This culture of complacency can affect any organization, worksite or work group where the primary focus is on meeting production goals or cutting cost, as well as accepting or ignoring standards creep. In such a culture speed is valued and cost cutting rewarded, while ignoring potential consequences. In many cases, there is a continual pressure for greater speed and ever increasing the production output, without due consideration for capacity, capability or consequence (standards creep). This, in many cases results in the workers taking shortcuts or risks to achieve goals and/or meet expectations in order to maintain their jobs.
This culture of complacency develops over time with each risk taken without an adverse effect results in the acceptance of more risk, which results in standards creep. This leads to the normalization of deviance. See my paper on “Normalization of Deviations” - posted here. All this reinforces the fact that all levels of management in the organizations must be on the “lookout” for the standards creep, where production trumps protection and a culture of complacency as well as risk taking becomes the norm.
Conclusion
Complacency is in fact a risk, and there are only a few methods in dealing with risk. These are risk avoidance, acceptance and monitoring, transfer, reducing the impact or its likelihood. The first few mentioned are either impractical or ineffective. The ones that may garner some form of positive result are reducing the impact or better yet reducing the likelihood of those risks occurring. One organizational approach is to make risk assessment a structured integrated part of planning. In construction, risk should be identified and assessed every time a contractor considers taking on a construction project. It should be considered during the estimating process, the operational planning process, the means and methods selection process, the pricing process, the subcontractor selection process, the staff assignment process, the organizational structure, selected work processes, tools and techniques used, technology selection, control methods, goal and objective setting, workforce capability, skill, experience and motivation... to name a few.
Issues stemming from complacency will decrease if an organization creates a culture that embraces enterprise-wide risk management. Functionally, such an organization is structured to be more responsive to risks and their treatments if dealing with risk is a part of all planning, organizing, directing, staffing, and controlling as it regards every aspect of the project delivery process, and has some form of confirmation element that it is being carefully adhered to as well as managed.