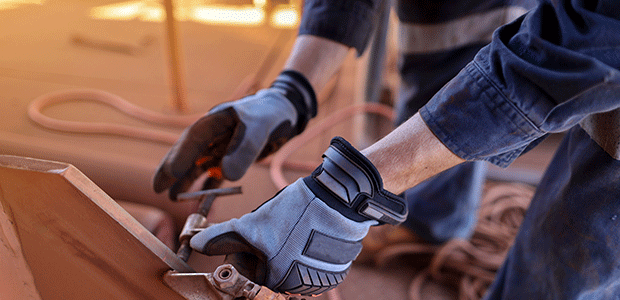
Pushing the Boundaries of Hand Protection
How a new technology is delivering next-generation comfort, dexterity and protection within industrial work gloves.
- By Andrew Shields
- Feb 01, 2021
Most industrial work gloves include a back-of-hand impact protector. Usually made from TPR (thermoplastic rubber) and stitched or glued onto the product, this component of PPE is vital in terms of function, but has a number of drawbacks.
The thickness of the TPR needed to give sufficient protection can make gloves inflexible and tiring to wear, while the level of dexterity required by a worker to complete many manual tasks can be compromised. The lack of ventilation caused by the large surfaces of solid TPR bumpers in such gloves also means they retain heat and sweat, making them uncomfortable over long periods of use.
As a result, some workers simply discard their hand protection rather than perservering with equipment that is uncomfortable and unsuited to the task. However, doing this leaves workers at greater risk of serious injury to one of the most vulnerable parts of the body.
Personnel in the offshore oil and gas, construction, mining, manufacturing, warehousing and transport industries, as well as consumers doing DIY, are particularly susceptible to hand impact injuries.
In 2018, the US Bureau of Labor Statistics reported that 43 percent of non-fatal occupational injuries to upper extremities requiring days away from work affected the hands. The Association of Drilling Contractors’ 2018 summary of occupational incidents found that more than 41 percent of total industry recordable incidents by body part involved fingers, hands and wrists.
Applying Cross-Sector Learning
A particular issue in developing products intended for use in demanding environments such as these is that glue or adhesive can fail, while stitching can come apart. Stitched products also require a flange, further obstructing dexterity and breathability and making them less comfortable.
Impact protection specialist D3O has conducted extensive R&D to explore how its materials could be more easily integrated into garments and combined with fabrics and substrates compared to the previously used methods. In 2019, the company launched D3O Ghost, a CE level 1-certified, “fit and forget” limb protector for motorsport and mountain bike riders. This product was manufactured using D3O Impact Print, a new process for imprinting D3O materials directly onto fabrics and substrates.
The process enabled the company’s materials to be printed directly onto a fabric with greater detail and complexity, and with the protective material attached to the substrate via a durable mechanical bond capable of withstanding the toughest conditions.
This combination of factors proved significant. The new technology made an optimal combination of breathability possible through the open geometries that support impact performance while also allowing airflow. The latter, which is defined by the substrate on which the protection is printed, includes the following:
- Enhanced flexibility (also determined by the substrate)
- Low profile due to the materials used
- Enhanced coverage from the ability to print anywhere (compared to the limitations imposed by adhesives or stitching)
- A superior level of performance.
Having successfully commercialised Impact Print for the motorsport and mountain bike markets, D3O explored which others could benefit from this new technology.
In March 2019, the ANSI/ISEA 138 - 2019 American National Standard for Performance and Classification for Impact Resistant Gloves was published. The hand protection market was rife for innovation that would meet level 3, the standard’s highest protection level, while outperforming existing technologies on the other key product attributes to support compliance—namely those related to wearer comfort.
Adding the Benefits of Proven Protection
PPE standards enable manufacturers to determine the performance requirements for the products they design and the procedures to test them with. They also help health and safety managers make informed choices about the right product for any given job.
Like all standards, ANSI/ISEA 138 sets minimum performance, classification and labelling requirements for occupational hand protection products. However, this particular standard goes further by incorporating performance levels from one to three, clearly identified with mandatory pictograms to help health and safety managers select the most appropriate product for a task.
“The revolution in back-of-hand impact performance through recent material advances has made ANSI/ISEA 138 practicable and facilitated a standard that is a major advance in terms of PPE protection,” says Kevin Fleer, D3O’s Head of Product. “The performance levels identified in the standard can be achieved more easily through next-generation tech.”
Promoting Behavior Change Through Innovation
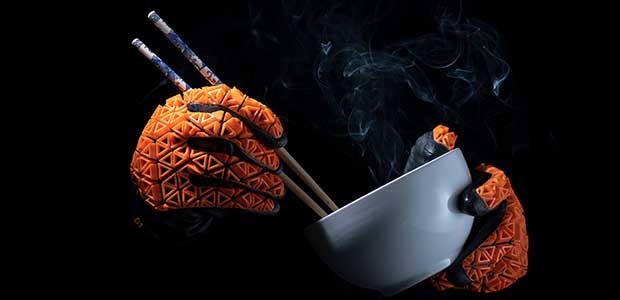
Traditional TPR or injection-molded manufacturing methods require the bumper geometry of a glove to be a large, solid, joined surface, which hinders dexterity and comfort. Printing directly onto a fabric enables intricate, open geometries with many small, individual modules, so flexibility is only constrained by the material itself.
By making it possible for protection to be printed throughout a glove rather than occupying only the sections which would allow stitching or gluing, up to 26 percent more hand coverage can be achieved compared to other gloves on the market. For the first time, the fingers and knuckles are connected and protection is extended towards the wrist.
This protection is also up to almost 50 percent thinner than other products, enhancing comfort over an extended period of wear. In short, it offers all the advantages of impact protection without any of its limitations.
Impact Print will make its industry debut in January 2021 as part of Mechanix Wear’s SpeedKnit line of coated work gloves. The key benefits will be no stitched parts, delivering increased comfort and flexibility while achieving the highest ANSI/ISEA 138 impact performance level 3 with a lighter-weight, lower-profile design that has tremendous dexterity advantages over most of the ANSI/ISEA 138 impact protection level 1 options available in today’s market.
To take advantage of these dexterity and performance gains, Mechanix Wear is utilizing the new touch screen compatible technology on its new SpeedKnit high performance dip knit line.
The Mechanix Wear gloves also meet the EN420 standard, which defines the general requirements and relevant test procedures for glove design and construction. This includes resistance to water penetration, comfort and dexterity, marking and information supplied by the manufacturer.
“The ability to print directly onto a fabric enables the creation of an industrial work glove that delivers breathability, comfort and dexterity compared to traditionally chunky and restrictive TPR products, without any compromise on impact protection,” concluded Fleer. “This technology pushes boundaries and the design opportunities are limitless.”
Furthermore, health and safety managers can be confident that the combined benefit of greater comfort and ANSI/ISEA 138 level 3 protection will increase levels of PPE compliance, reduce the chances of worker hand injuries and enhance productivity—all positive contributions to a business’s bottom line.
The technology also has potential applications beyond hand protection. The US Bureau of Labor Statistics data for 2018 showed that the upper extremities, including the arms, accounted for 31.9 percent of all injuries involving days away from work. The lower extremities, including the legs, accounted for 23.9 percent. In the future, innovative industrial sleeves and limb protectors that incorporate printed impact protection could lead to even safer workplaces.
This article originally appeared in the January/February 2021 issue of Occupational Health & Safety.