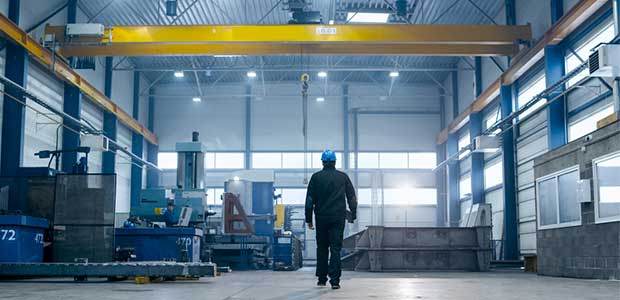
Professionally Distanced: Ensuring Employee Safety Through Remote Monitoring and Social Distancing
Technological advancements in monitoring methods—especially personal monitoring equipment—have presented unintended possibilities for aiding in the fight against COVID-19 in the workplace.
- By Tim Turney
- Sep 01, 2020
With the focus for many businesses dealing with the ongoing COVID-19 global health crisis beginning to shift to “the new normal” and returning to the workplace, workers and employers alike are asking questions about how workplaces will be made and kept safe.
According to a poll of U.S. employees, 54 percent shared concerns about exposure to COVID-19 in the workplace. Employers can take assurance, however, in the fact that 71 percent of those polled have confidence that their employers can bring them back to work safely.
COVID-19 is a health hazard that will necessitate new ways of working for some time to come, with one of the primary methods to limit the spread of the virus being maintaining social distancing of at least six feet (or two meters) between people. While COVID-19 is a primary concern and must be consistently monitored in all workplaces, it does not mean that the old hazards of many workplace environments have disappeared.
When reintroduced into workplaces, it is essential that employers and employees continue to observe monitoring procedures for other risks to health including noise, dust and vapor hazards. Technological advancements in monitoring methods for these hazards have presented unintended possibilities for aiding in the fight against COVID-19—namely personal monitoring equipment where employees can start measurements and check data remotely without disturbing the wearer.
It is important that employers establish protocols that allow workers to minimize close contact and ensure social distancing throughout a shift as much as is possible, while continuing hazard monitoring with minimal disruption to either procedure. Whether individual workplaces will be adapting social distancing into existing workflows or changing workflows to introduce social distancing measures, flexibility of monitoring equipment will make either approach much easier to integrate.
Body-worn monitoring equipment allows individual units to be issued to employees in a controlled way. These equipment pieces can be collected from a demarked area at the start of a shift, which allows a restricted number of employees in and out at any one time while maintaining a social distance. This method can then be used for employees to deposit units at the end of a shift, ready for thorough cleaning and disinfection.
Once equipment has been issued, real-time results can be checked remotely throughout the day. Connectivity is key; advancements such as integrated Bluetooth connections allow dosimeters and pumps to access remote data at distances that greatly exceed the suggested social distancing minimum of six feet. This minimizes both worker disruption during a working day and potential close contact levels, increasing peace of mind for employees and employers alike.
In addition to real-time data such as battery charge level, flow rate, run time and volume sampled, these devices allow managers to generate full reports for a monitored period and send them via email from the app.
With the ability to overview and download data from multiple devices, managers are given a clear picture of hazards across the workplace without having to interact with monitoring units (and the employees wearing them) directly. Utilizing Bluetooth or remote connectivity in conjunction with a sampling pump and an air flow calibrator allows users to calibrate monitoring devices and check results remotely, giving confidence in results and minimizing physical interactions from the start of sampling to completion.
Advances in personal monitoring technology, such as Bluetooth connectivity and partner apps, were developed to meet the ‘traditional’ challenges of workplace hazard monitoring. While the impact that COVID-19 has had on workplaces has been impossible to predict, such advances have given users the flexibility to adapt to socially distanced working while continuing seamless workplace monitoring for existing hazards such as excessive noise, dust, particulate and vibration levels.
This article originally appeared in the September 2020 issue of Occupational Health & Safety.