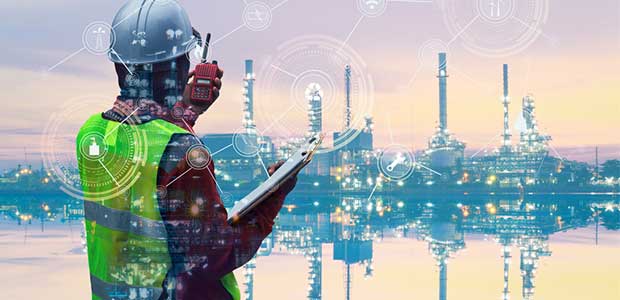
Harnessing IoT to Maintain Occupational Safety, Minimize Risk During COVID-19 and Beyond
Best practices being deployed in construction and industrial environments.
- By Robert Costantini
- Aug 01, 2020
As workers slowly but certainly return to manufacturing plants, construction sites, oil refineries and office environments in a post-COVID-19 world, there will be new requirements, processes and ways of working that were not even a consideration just a few short months ago. Yet, what does not change is the ongoing commitment to keeping workers safe on the job.
Thanks to Internet of Things (IoT) technology and wearable devices, businesses everywhere are finding it easier to help prevent the spread of COVID-19.
IoT technology has already been making inroads in industrial markets. According to a survey1 conducted by TechPro Research, “The Industrial Internet of Things (IIoT) has the potential to significantly impact businesses.” Key industries, such as manufacturing and energy, among others, are interested in or already using IIoT devices. Based on the survey results, 82 percent of respondents have either implemented IIoT, are running a pilot project, or are considering implementation. Most respondents recognize the value of using IIoT devices.
The New PPE: IoT on the Jobsite
The use of IoT technology at worksites will only accelerate as COVID-19 moves the technology from a long-term business strategy at many firms, to an immediate business necessity. The CDC, ECDC, and other public agencies cite a minimum of six feet of social distancing as a way to minimize the spread of COVID-19.2 The CDC also provides guidance for contact tracing, in order to track and monitor the close contacts of infected individuals and notify them of possible infection.3
In addition to helping companies ensure compliance to these guidelines in the fight against COVID-19, IoT solutions also provide real-time information about who is on the site, where they are operating and who is working together. By making this information accessible through a cloud-based dashboard, they allow project managers to maintain accountability across a worksite while minimizing potential exposure to the virus. Furthermore, since all IoT information can be stored in the cloud, project managers can access it from a remote location as well as the worksite.
Gaining Actionable Insights
While guidelines are in place, it can be extremely difficult for workers to maintain social distancing from each other on a complex worksite where they often need to work together on projects. When workers are focused on their specific tasks they are often not aware of how close they may be to another worker. The need to continually look around to see who’s near them in order to avoid potential exposure can be very distracting for workers, who may be operating dangerous machinery or tools. Today, advanced IoT devices worn by workers can communicate with other devices and send out an audible and visual alarm when they come into close contact with one another.
In addition to actively alerting workers who are in close proximity, the devices collect passive data on these interactions with other devices as well as the duration of each one. This data can be used to identify patterns and develop new best practices to prevent and correct behavior that can cause the spread of the virus.
In the event that someone is exposed to the virus, an employer can conduct contact tracing using this historical data that is captured passively by the worker’s device to identify who may have been exposed. Traditional methods of contact tracing rely on workers’ memories and whether they can identify other workers by name and recall who they were in contact with during a given time period. Now, with more reliable information from IoT devices, companies can decide who needs to be in mandatory or precautionary quarantine per CDC guidelines. Without these types of solutions, in the event of an infection, entire plants could be completely shut down as it can be difficult to determine and isolate specific individuals who were exposed.
In addition to social distancing and contact tracing support, every industrial sector is rethinking how it conducts routine activities—from signing in at the worksite to tracking time—in order to reduce touchpoints. IoT technology can also support these efforts.
One way to reduce contact on the worksite is by automating time and attendance. Normally, on construction jobsites for example, there are common check-in points where workers line up—often in a cluster—to sign in for the day and clock out, sometimes using shared pens. Some forward-thinking employers are using wearable devices to automate this time and attendance process by having the wearable device automatically log the worker in and out. This improves safety by avoiding a crowd of employees waiting to sign in, and eliminates the need for dedicated personnel to be in contact with workers throughout the day as they check in and out.
OSHA Policies for COVID-19
Additionally, new federal rules are forcing employers to take a hard look at how they track employees diagnosed with COVID-19 and search for new tools to help them meet the mandates.
Up until last month, only employers in the healthcare industry, emergency response field and correctional institutions had to make “work-relatedness determinations” about coronavirus transmission on the job. But in May, the U.S. Department of Labor’s Occupational Safety and Health Administration released updated policies4 that broadened the list of employers with coronavirus-related record-keeping requirements.
Now, COVID-19 is considered a recordable illness for all employers covered by OSHA’s record-keeping regulations.5 Workplaces must record cases of the coronavirus if they are work-related6 and involve one or more of the general recording criteria,7 such as requiring medical treatment8 beyond first aid or days away from work.
IoT-based social distancing and digital contact tracing technology can support the new OSHA policy by providing proximity alerts when workers stand too close together and record these close contact interactions, offering employers a digital trail of potential exposure.
As the COVID-19 health crisis has shown, companies everywhere need to change their business processes and implement new ways of doing business to succeed in the new normal. IoT technology holds the key to minimizing worksite risk, providing safe environments and ensuring peace of mind for businesses and workers alike.
REFERENCES
1 https://www.techrepublic.com/resource-library/downloads/research-why-industrial-iot-deployments-are-on-the-rise/
2 https://www.cdc.gov/coronavirus/2019-ncov/prevent-getting-sick/social-distancing.html#:~:text=Stay%20at%20least%206%20feet,while%20school%20is%20out.
3 https://www.cdc.gov/coronavirus/2019-ncov/php/open-america/contact-tracing-resources.html
4 https://www.osha.gov/news/newsreleases/national/05192020-0
5 https://www.osha.gov/recordkeeping2014/records.html
6 https://www.osha.gov/laws-regs/regulations/standardnumber/1904/1904.5
7 https://www.osha.gov/laws-regs/regulations/standardnumber/1904/1904.7
8 https://www.osha.gov/laws-regs/regulations/standardnumber/1904/1904.7
This article originally appeared in the August 2020 issue of Occupational Health & Safety.