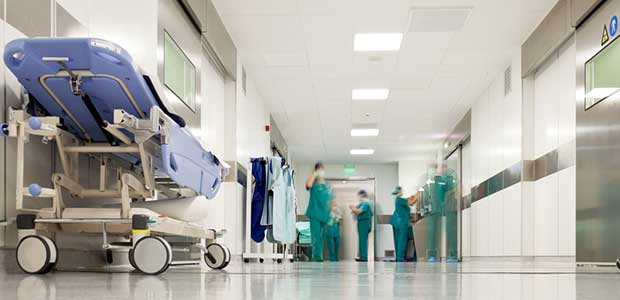
Infection Control: Adapting Worksites at Active Healthcare Facilities
It’s critical to consider how factors like emergency management, patient flow, security, life safety and infection prevention and control all are affected by construction, and endeavor to minimize the impact work has on occupied spaces.
- By Matt Elliott
- Jun 30, 2020
COVID-19 has forced nearly every industry to enhance safety protocols. Perhaps more than others, those working in construction are well-prepared for these changes. When constructing or renovating healthcare facilities, it’s critical to consider how factors like emergency management, patient flow, security, life safety and infection prevention and control affect and are affected by construction, and endeavor to minimize the impact work has on occupied spaces.
In many ways, the precedent has already been set for infection control precautions in healthcare construction. Maintaining access to jobsites and coordinating shutdowns so as not to impact patient rooms during the COVID-19 pandemic is not new to those who work on construction sites at medical facilities. Based on the determined risk level, and in adherence to the hospital’s published requirements in its contractor handbook (if it has one), an infectious control and containment plan is developed well in advance of the construction start.
To control infection, sites occupied by patients must remain dust- and contaminant-free. To do this, we employ containment systems ranging from finished, hard partitions to fabric or plastic barrier systems. We also set up anterooms to keep negative air pressure within the workspace and out of patient rooms. Anterooms look like small boxes and comprise of two doors: one to get in and one on the other side with a door or zippered opening to block debris from escaping. In some cases, two anterooms may be necessary to ensure maximum imperviousness.
Challenging cases—like maintaining negative pressure while working in interior, positively-pressurized rooms—necessitate creative solutions. In 2014, we finished out six operating rooms and two existing rooms, all without windows at the interior of the building and surrounded by other sensitive areas. As a rule, ORs are positively pressured to keep contaminants out. As such, we used a two-pronged approach of temporarily adjusting the supply air balance of the room while exhausting a significant amount of air through temporarily-installed ductwork above ceiling and through a circuitous route across other spaces to reach that exterior window.
To that end, increased COVID-related, hospital-wide sanitation efforts have prompted us to introduce additional infection control measures. Hospital staff administer temperature scans of everyone entering worksites and temperature checks are self-conducted by the construction teams on-site. Without exemption, construction workers don PPE face masks. Worksites are sanitized at the end of each day, and tools are regularly wiped down with disinfectant.
As able, project teams space out the daily schedule to allow for as much social distancing as possible. Staggered schedules and physical separation of worksites limits exposure between groups of workers. Additionally, evening shifts allow for fewer trades to be on the job site during the day.
Good construction firms have always done everything in their power to limit debris and control the spread of contaminants on the worksite. With proper adherence to these outlined recommendations, hospitals will remain safe places for patients, healthcare workers and construction crews.
About the Author
Matt Elliott, CPC, is a healthcare project executive with SpawGlass, a Texas-based general contractor, construction manager, design/builder and civil contractor.