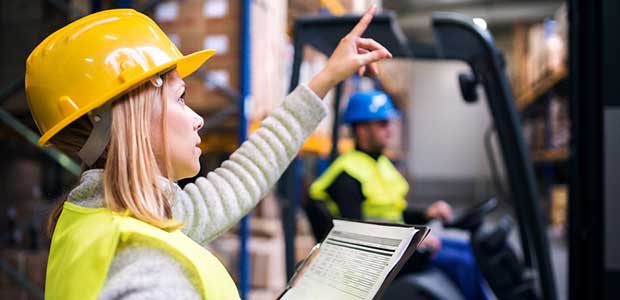
If I Were the Boss
Safety is as critical an element as production to an organization, but why doesn’t the message always resonate up to the top of every organization? Here are some checks and balances you can utilize to better prioritize safety.
- By Joseph Werbicki
- Jun 16, 2020
It’s just my opinion that one of the most frustrating and unappreciated workplace jobs has to be that of the person tasked with safety. Looking back on my years as a safety manager, the best that I could hope for was a feeling of being tolerated (“better put on the safety glasses, here comes Joe”).
The worst-case scenario that can be imagined is when safety is just another hat worn by an otherwise overworked employee. Safety may be simply window dressing to fill a position on an organization chart. In such cases, where does safety sit on that person’s priority list? To make things worse, the safety part of the job may report to someone who has his/her own (non-safety) job to do and has no idea of the scope and value of the safety function.
In other cases, there may be a knowledgeable and professional person, adequately trained and experienced in safety, in charge of a program whose efforts are routinely deemed as secondary to production, reporting to someone who simply tolerates the safety person as a necessary evil, and who provides little or no guidance, authority or funding to do what needs to be done to keep the workplace safe.
Then there are the lucky ones, who report to someone in a position of authority who gets it where safety is concerned. They put safety up there with other core values. I always read with great interest the National Safety Council’s annual list of CEOs who ‘get it’ (published in Safety + Health Magazine). In a perfect world, safety would report to upper management, given the impact an unsafe workplace can have on the bottom line.
Liberty Mutual publishes an annual Workplace Safety Index, documenting the billions of dollars lost each year due to accidents and injuries. For 2019, the total cost of the most disabling injuries was $55.43 billion.
There is sufficient, documented information that speaks to the direct and indirect costs of accidents and injuries. Accidents need not be tolerated as one of the costs of doing business. Accidents signal a deficiency in the overall operating system, the causes of which need to be identified, corrected and learned from. The best example of the value of accident investigations is that of aircraft accident investigations. The findings and recommendations made by national air accident investigation boards have made flying significantly safer year after year.
Not to be forgotten is the sobering fact that, according to the Bureau of Labor Statistics, there were over 5000 fatal occupational injuries in 2018, 2.8 million non-fatal workplace injuries and over 900,000 cases with days away from work. The direct cost of a lost-time workplace injury can range from $1,000 to $20,000 with indirect costs estimated to be four to 10 times the direct costs, depending on the sources cited.
Additionally, production—the prime driving force for many organizations—is impacted when equipment is damaged or when workers are off the job due to injuries.
To safety professionals, it’s a no-brainer. Safety is as critical an element as production to an organization. Why doesn’t the message always resonate up to the top of every organization? Top management needs to demand (and fully support) an A-game when it comes to safety. Upon reopening a Volkswagen plant on April 23, 2020, the company said the plan was “health before production numbers.”
An example worth noting is that of Paul O’Neill who, when he was introduced as the new Chairman and CEO of Alcoa back in 1987, stated, “If you want to know how Alcoa is doing, you need to look at our workplace safety figures.” At the time, almost all Alcoa plants experienced at least one accident a week. When he retired in 2000 the company’s injury rate was one-twentieth the U.S. average, and the company’s net income was five times that of 1987.
So, safety people, if you were the boss, what would your safety program look like? How about sharing some thoughts with the boss?
Here a just a few suggestions to prioritize to suit an individual workplace:
- Place safety on a par with production. Make it a core value, not a priority. Both are crucial and can work hand-in-hand. Get the job done, and get it done safely.
- Do you know how your facility functions? Be visible to the workforce. Get out of the ivory tower and see what is happening on the shop floor, and visibly support safety efforts. Executives must “walk the walk” as well as “talk the talk.” Everyone follows the same rules when it comes to safety.
- Encourage and support certification for safety personnel, through the National Safety Council’s Advanced Safety Certificate, the Board of Safety Professional’s Associate Safety Professional (ASP) or Certified Safety Professional (CSP); the Institute of Hazardous Materials Management’s Certified Safety & Health Manager (CHM), Certified Safety Management Certificate (CSMP), or Associate Safety & Health Manager (ASHM); or, the National Association of Safety Professionals Environmental Health & Safety Professional Certificate.
- Supervisors are the first line of defense for any safety program. They are best able to observe, correct and mentor daily behaviors and adherence to safety procedures. Assign to them the responsibility for health and safety in their individual areas. Make safety an element of their job evaluations. However, if they are not trained in safety, what can you expect of them? Make sure that they receive safety training. Their time away from the production floor will be a sound investment.
- Ensure that each new employee receives a safety orientation on day one of employment. Use a comprehensive checklist and have each employee sign to acknowledge that he/she has received the training and is committed to safe job performance.
- Ensure that all mandatory safety training is completed on-time, is documented, is put into practice and is followed up to insure retention. Doing a job safely is as important as doing a job well.
- Ensure that operators of critical equipment are trained and certified.
- Don’t encourage getting work out at the expense of safety.
- Set up a system where employees can anonymously report accidents, unsafe working conditions and near-misses.
- Investigate ALL reported incidents, accidents and near-misses. Disseminate and implement findings, lessons learned and procedural changes with the goal to prevent recurrence.
- Encourage near-miss reporting. A near-miss is a near-hit. Much can be learned before accidents occur.
- Establish enough safety committees to ensure that all work areas have a voice in safety and that findings and recommendations are implemented. Encourage feedback on safety issues, especially from the floor. Workers know best what is happening on a day-to-day basis at their workstations.
- Have trained responders (first-aiders; nurses; EMT’s; paramedics) on-site to ensure rapid response to accidents. Don’t depend on local emergency services, whose response time may not be adequate to meet OSHA guidelines.
- Draft Job Safety Analyses for all jobs. These spell out the hazards that can be encountered and provide a good checklist for job training.
- Keep the workforce updated on what is being done to keep employees safe, where deficiencies have been identified, what is being done to correct unsafe situations and good news when progress is being made. Emphasize that each individual is ultimately responsible for his/her own safety. A comprehensive safety program is the basis for a safety culture, where employees feel safe and empowered to participate in continuous improvement.
- Utilize the expertise of safety equipment suppliers to ensure that personal protective equipment is appropriate and adequate for each job. Maintain an adequate stock of PPE to meet demand.
- Ensure that all employees whose jobs requires PPE are provided quality products, are trained in proper use, wear them when required and that there are procedures for proper storage when not in use and disposal and replacement when needed.
- Budget for items in the physical plant that can pose ongoing safety hazards such as lighting, walking surface quality and equipment maintenance.
- Schedule independent safety audits (to identify any systemic problems) and routine safety inspections (to check for day-to-day adherence to all safety guidelines). Set up safety observer teams to routinely monitor the work area using appropriate checklists. Rotate personnel into these teams to give them first-hand knowledge of safety protocols. Provide safety procedures reference binders for each area, which can be consulted when needed.
- Establish a policy of continual improvement of the safety program. Set forth a safety and health policy statement that sets clear program goals and objectives.
- Small and medium-sized businesses can take advantage of the no-cost OSHA On-Site Consultation Program.
- To upgrade your safety efforts, you can opt for certification of your safety program through the OSHA Voluntary Protection Program (VPP), OSHA’s Safety and Health Achievement recognition Program (SHARP), or ISO 45001.
- Conduct periodic air quality testing in areas where there may be a potential for health hazards (loading docks; paint spray booths; sanding areas; etc.).
- Provide resources (time, money and clout) for the safety program. When it comes to funding, the U.S. Department of Labor estimates that a good safety program can save four to six dollars for each one dollar invested. How’s that for a good ROI incentive, boss?