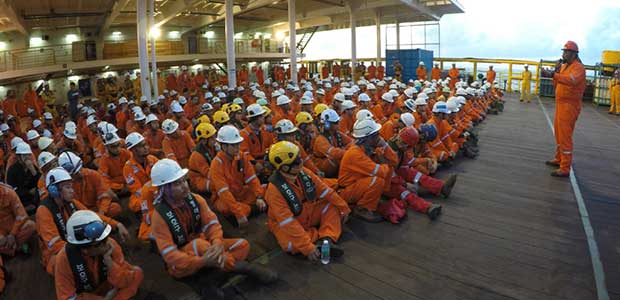
Tracking Safety: Practical Ways to Use Leading Indicators
Challenges like inconsistency and meaningless data hold many companies back. But is it actually worth it to use leading indicators? The answer is a resounding 'yes.'
- By Peter Grant
- Jun 12, 2020
I recently attended a Public Stakeholder Meeting on Leading Indicators, held by the US Department of Labor. There, presenters re-emphasized the potential impact of prevention metrics on safety programs across the country.
Challenges like inconsistency and meaningless data hold many companies back. But is it actually difficult to use leading indicators?
Understanding Leading Indicators
Leading indicators are metrics that coincide with (or indicate) the health of a safety program. The most effective leading indicators monitor participation in safety-related activities at various levels of a business. A few commonly used examples include:
- Toolbox talk attendance per month
- Participation in safety training activities per month
- Hours spent on safety tasks per day
- Number of positive safety observations per week
Note it’s not the activity itself, like toolbox talks, that makes a leading indicator valuable. It’s the measurement of employee engagement in said activity, through attendance, participation etc.
More Than Lip Service
Take this example from day-to-day life. To reduce your cavity rate, you could decide to brush, floss and attend regular cleanings. If you’re only tracking lagging indicators, you’d only record tooth pain and cavities. But by the time you have tooth pain, you may have already skipped brushing and flossing multiple times per week. It may be too late for you.
If you’re tracking leading indicators, however, you’re actually tracking and trending the frequency of the activities you and your dentist decided were most important (in this case, brushing, flossing and attending cleanings) in preventing a cavity in the first place. If you have a horrible week and forget to brush your teeth three times, a review of your leading indicators should alert you to heightened risk, giving you ample time to get back on track.
As you can see, leading indicators must correlate with incidents and they must be tracked consistently enough to reveal deviations from the norm. These parameters can make tracking leading indicators challenging—or so it would seem. There are a few critical steps you can take to make tracking more feasible for your company.
Three Steps to Start Using Leading Indicators
The key to starting your journey is not getting bogged down with what to track. Start with the indicator that you’re already tracking to some extent. For many companies, this is safety inspections of work conditions, employee behavior or toolbox talks.
Take the COVID-19 pandemic, as a relevant example. You could track toolbox talks about hygiene or positive/negative safety observations regarding CDC guidelines for preventing the spread of coronavirus.
Once you’ve identified your indicators, take these steps to track them:
1. Engage all responsible parties.
2. Set up an easy track/trend system for responsible employees.
3. Schedule regular check-ins.
These steps essentially set up a system that makes tracking easy, which increases the likelihood that it’ll happen. Let’s dive into each step:
Engage Safety Stakeholders
Any person at your company who’s responsible for employee safety in any capacity should understand the purpose and importance of leading indicators. Here are a few ways you can kick-off engagement in leading indicators:
- Hold a lunch meeting with an open discussion on the state of safety in your company and a brief presentation on leading indicators.
- Ask everyone responsible for safety which leading indicators they think would be a great fit for tracking (or tracking better than you are now).
- Over coffee, review examples of companies that improved safety by tracking leading indicators and how they did it.
Bottom line: this is not an area for company leadership to delegate all responsibility. Because tracking leading indicators takes time at first, leadership must understand what can be gained and what’s at stake if the effort is half-baked.
Set Up Your System
It’s easy to get bogged down in this step. Most companies begin with a system that’s easy to start. While the intent is good, the problem with this approach is many systems that are easy and cheap to start — like paper scorecards — are tiresome to use.
If your system is too time-consuming, too difficult to use in the field, or just plain boring you risk wasting time. Look for a system that is incredibly easy to use and will fit into already existing workflows.
Ideally, you’ll find a safety management app you can use to capture information in the field and trend your chosen indicators on a dashboard.
Schedule Rewarding Check-ins
Schedule leading indicators check-ins in advance. Include a reward element to make it less likely you’ll cancel the meetings. Check-ins may involve your entire safety committee or just a few select personnel.
These short meetings should also happen between a committee member and a company director or executive, though less frequently, to keep the highest levels of leadership engaged.
Check-ins can happen as often as weekly or bi-weekly, but most companies will find it more reasonable to have them monthly.
At each check-in, review your leading indicator data and compare it to company (or industry) benchmarks to identify areas for improvement. It’s also a great time to discuss tracking challenges or general safety issues in the field.
To make check-ins rewarding, you may decide to go off-site to have your meeting, enjoy a beverage or lunch offsite, or give a gift card for reaching goals.
Ultimately, you aren’t making these meetings enjoyable to give yourself a pat on the back. You’re doing it to failsafe your overall system.
Conclusion
It is difficult to track leading indicators if you don’t first set your team up for success. Attendees of the DOL stakeholder meeting were in agreement on this point.
To track leading indicators, set up a system that makes it as easy as possible. Start by engaging safety stakeholders. Then, use mobile-friendly software to capture and trend your data. Finally, don’t neglect check-ins.
With a solid system in place, you’ll be able to harness the power of leading indicators and prevent injuries before they occur.
Peter Grant is co-founder and CEO of Safesite, a safety management software and leading indicators dashboard. His experience working as a civil engineer in project management for large commercial contractors motivated him to use mobile technology to reduce preventable incidents and deaths. That goal has driven Peter's strategic decisions for Safesite, which has grown from a mobile app to a robust safety management system. Read more of Peter’s safety insights on the Safesite blog.