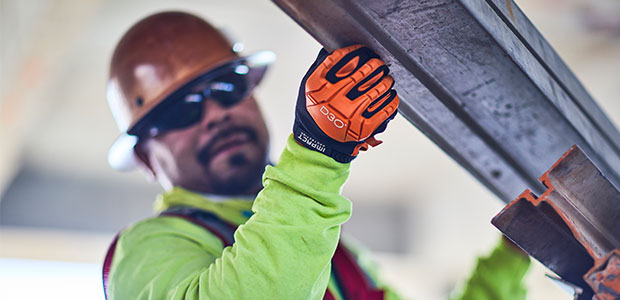
How Health and Safety Managers Can Reduce the Risk of Hand Injuries
Even with rigorous safety protocols in place, the bones and tissues in the back of the hand remain particularly vulnerable to impact injuries.
- By Andrew Shields
- Feb 01, 2020
The hand is one of the most complex pieces of engineering in the human body, which explains its vulnerability in industrial environments. What actions can occupational health and safety managers take to specify PPE that better protects workers’ hands and reduces the number of lost time incidents?
With 27 bones, 48 nerves and 123 ligaments and tendons, it’s little surprise that the hand is the second most frequently injured part of the body (after the back). According to the U.S. Bureau of Labor Statistics1, almost 120,000 injuries to hands and fingers in 2016 involved days away from work—13 percent of the total injury toll. Statistics from the International Association of Drilling 2 that in 2018 more than 34 percent of all recordable incidents in the oil and gas industry affected the hands, wrists and fingers.
Even with rigorous safety protocols in place for the oil and gas, construction, mining, manufacturing, warehousing and transport industries, the bones and tissues in the back of the hand remain particularly vulnerable to impact injuries. These range from a bruise to the knuckles to pinching fingers between two pieces of equipment to a severe bone fracture. How can occupational health and safety managers reduce their incidence rates?
Identify Risks as well as Hazards
Job Safety Analysis (JSA) is a key tool within Occupational Health & Safety (OH&S). A typical JSA process breaks down a task into a sequence of steps, identifies the potential hazards in each step, and specifies any preventative measures needed to overcome them.
This approach usually considers ‘hazard and control,’ but does not take account of any risk components such as ‘How often is a hazard encountered?’ or ‘What is the potential impact energy of the hazard?’ The greater the frequency of the hazard, such as the number of times a rail-car door is opened, the greater the risk. Similarly with impact energy like a hammer strike, for example, how much risk is attached to the force delivered by each strike?
Including both of these risk components will make a JSA more comprehensive. By then applying ANSI/ ISEA 138, the new American national standard for impact resistant hand protection to each step of a task, it will be possible to make risk-based decisions on the most appropriate performance level of gloves to assign where impact protection is required.
Recognize the Value of Performance Standards
Knowing the true performance of PPE is critical to reducing the risk of injury.
“The hand protection market is growing at an accelerated pace, so we are the first to acknowledge that it can be challenging for H&S managers and specifiers to navigate available options and choose the right protective product for the given task,” Bill VanMullekom, Executive Vice President at D3O US LLC said. “Performance standards are an essential tool for both PPE specifiers and manufacturers to ensure the decisions they make are the correct ones.”
Standards for cut, puncture, chemical, and thermal protection in gloves have existed in the U.S. for many years but, until recently, there was no performance standard for back of hand impact resistance. This gap has now been filled by ANSI/ISEA 138.
Cutting occupational injuries through the application of performance standards can also have a positive impact on a company’s bottom line. Fewer lost-time injuries means overall increased productivity. The financial impact of workplace injuries can be calculated with the $afety Pays tool developed by the Occupational Safety and Health Administration (OSHA).3 This program uses a company’s profit margin, the average costs of an injury or illness, and an indirect cost multiplier to project the amount of sales a company would need to cover those costs.
Use Standards to Specify More Accurately
A common approach among H&S managers is to obtain a variety of gloves advertised as offering impact protection, ask employees to try them out, get feedback, and go with those most preferred by the workers—provided the gloves selected also satisfy budget constraints. Then, if an employee sustains an injury, the cycle of fieldtesting to find the next preferred gloves has to start all over again.
Quite apart from the hit-and-miss nature of this method, the fact that a hand injury costs an average of $20,000 before surgery or lost time is factored in points to a clear financial benefit from more accurate specifying.
A manager’s objective is to deliver optimum protection for a job, rather than under- or over-protection. In the same way that thin cotton gloves would offer inadequate protection to a drilling rig operator using a 50-pound wrench covered in oil, heavyweight gloves with limited manual dexterity would not only risk the wrench sliding out of a worker’s hands, but they would also add unnecessary expense. ANSI/ISEA 138 helps eliminate such trial and error.
“Before the introduction of this standard,” Jill Clements, Chair of the ISEA Hand Protection Product Group said. “We had gloves with bumper guards which some manufacturers referred to as impact protection. When tested, they were found to offer protection against nothing more substantial than a knock. There’s a place for these gloves in the market but we now have an impact protection standard that gives clarity about how much energy is being transferred through the glove.”
The simplified approach of the standard, with performance levels identified by pictograms on the gloves, has made testing and choosing the most appropriate protection a more precise exercise.
Educate Your Workplace
Faced with an array of gloves to choose from and no specific guidance, a worker may pick a pair he or she recognizes from a previous task, or simply grab the nearest available. Furthermore, two gloves may look the same to a wearer, but the difference in the level of protection offered can be significant.
Providing a core range of gloves along with education and visual management on how they match glove selection to specific tasks reduces confusion and makes it easier for workers to select the most appropriate pair.
Continually Reassess Risks to Optimize Protection
Applying ANSI/ISEA 138 and other relevant hand protection standards, such as ANSI/ISEA 105-2016 for mechanical protection, chemical protection, ignition resistance and vibration reduction, involves decisions to choose the right performance level of gloves for a particular task.
H&S managers can use standards and the performance levels within them as day-to-day tools—not only to help continually reduce the risk of injuries, but also to help provide clarity when seeking approval on spend for worker protection.
“First, the standard provides a starting point that is reliable and evidence-based,” VanMullekom said. “End-users can then apply their own specific variables, such as workforce, tasks, budgets and working environments.
“Armed with this information, HSE’s are in a better position to align the different hazards or risks that a wearer might face to the protection of the appropriate performance level. In this way, the choices made can truly meet the needs of the workforce.”
ANSI/ISEA 138 EXPLAINED
ANSI/ISEA 138 establishes minimum performance, classification and labeling requirements for gloves designed to protect the knuckles and fingers from impact forces:
- The standard evaluates gloves for their ability to dissipate impact forces and classifies them accordingly.
- Impact performance is classified using three distinct levels: level 1 offers the lowest protection, level 3 offers the highest.
- A glove’s level of performance is indicated with a mandatory pictogram which must be clearly visible and legible throughout the normal useful life of the glove.
OH&S specifiers can use the classifications to compare products on an equal basis. They can still choose from gloves that compete on factors such as design, durability, comfort and cost, but not on key performance characteristics.
REFERENCES
1 www.bls.gov/spotlight/2019/25-years-of-worker-injury-illness-and-fatality-case-data/pdf/25-years-of-worker-injury-illness-and-fatality-case-data.pdf
2 www.iadc.org/isp/iadc-2018-isp-program-annual-report-index
3 www.osha.gov/safetypays
This article originally appeared in the January/February 2020 issue of Occupational Health & Safety.