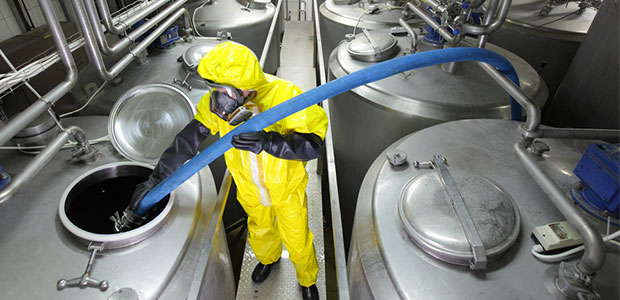
Process Safety Management— A Challenge for Small Businesses
Small businesses often find it difficult to execute PSM.
- By Janet Persechino
- Dec 02, 2019
OSHA’s Process Safety Management (PSM) of Highly Hazardous Chemicals regulation applies to facilities that handle a threshold quantity of specific chemicals listed in Appendix A of the standard.
The regulation calls out 14 mandatory elements, and within each element is a list of required items. Implementation can be complex and resourceintensive. The elements, or programs, are focused on decreasing the likelihood of a loss of containment and are somewhat performance-based, leaving room for interpretation. For this reason, a certain level of experience, expertise, and understanding is needed to ensure that the programs actually meet the true intent of the standard.
Small businesses often find it difficult to execute PSM. OSHA points to a study for the chemical processing industry that estimates, “employers with one to 25 employees are 47 times more likely to have a release and 17 times more likely to suffer an injury, per employee, than facilities with 1500 or more employees.”
Insurance companies and other Authorities Having Jurisdiction will also be interested in the quality of the PSM programs due to the risk and loss potential. These parties will want to confirm the facility’s awareness of the process hazards and will look for assurance that they are reducing the risk to a level that is as low as reasonably practicable (ALARP).
Process Hazard Analysis
One mandatory PSM element is Process Hazard Analysis (PHA). This is a formalized and systematic approach that analyzes the design of a chemical processing system to ensure that it will operate safely. There are various PHA methodologies that are recognized by the chemical industry and the regulation. The PSM standard specifically states:
“The process hazard analysis shall be performed by a team with expertise in engineering and process operations, and the team shall include at least one employee who has experience and knowledge specific to the process being evaluated. Also, one member of the team must be knowledgeable in the specific process hazard analysis methodology being used.”
OSHA realizes that it can be difficult for some companies to comply with this requirement, and states in its document, Process Safety Management for Small Businesses:
“Some companies, particularly smaller ones, may not have the staff expertise to perform such an analysis. The employer, therefore, may need to hire an engineering or consulting company to perform and augment the analysis.”
PSM Implementation
For the reason listed above it can prove helpful for your company to work with a PSM consultant that knows how to integrate the PSM system into your organizational structure.
A good PSM consultant will stay abreast of developments and advances in the industry that can facilitate compliance. This can result in increased efficiency, safety, product quality, and a competitive advantage. The benefits of hiring a consultant typically outweigh the upfront costs. These benefits include time saved in PSM implementation, process improvements, cost-effective solutions to corrective actions, potential savings on insurance and/or avoidance of a loss.
This article originally appeared in the November/December 2019 issue of Occupational Health & Safety.
About the Author
Janet Persechino is employed at Engineering Planning and Management, Inc. (EPM). She can be reached at jap@epm-inc.com, 508-532-7360, for a free chemical process safety consultation