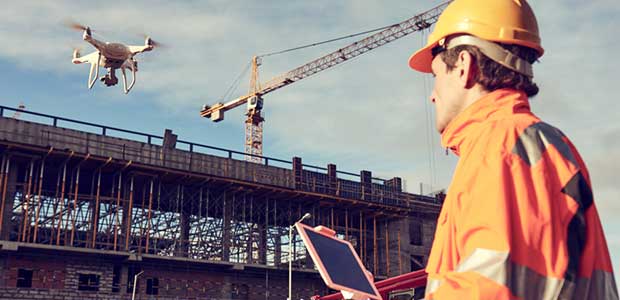
Companies Use Drones to Limit Dangerous, Potentially Fatal Tasks for Workers
With 166 deaths in confined spaces and 887 deaths from falls in the United States in 2017, drones are becoming a safer way to complete dangerous tasks.
Companies are increasingly beginning to use drones to performsome of the dangerous tasks that workers risk their lives executing.
Jobs such as working in confined spaces to retrieve trash or fix machinery or working on tall scaffolding to paint a building can be fatal, but as technology develops, workers are beginning to have to perform these jobs less and less.
Huge companies including Dow Inc., AT&T Inc., BASF SE and Royal Dutch Shell Plc have begun using drones to do dangerous jobs such as inspecting tanks and towers from hundreds of feet in the air, replacing faulty parts in small tunnels and looking into smokestacks.
Christ Witte, manager of chemical giant BASF’s Freeport, Texas site said the site is using drones to keep workers off scaffolding and out of tanks where potential injuries lurk.
“We look at these tasks and say, ‘Is there a better way that we can do this without exposing the worker to risk?’” Witte said. “The answer is yes. We can send a drone in.”
Research shows that even though drones are expensive, at costs ranging anywhere from $25,000 to $250,000, they not only save lives, but cut costs for companies. Many jobs that would’ve taken human workers days take drones only a few hours.
In 2017, 166 U.S. workers died in confined spaces, and 887 died by falls, which is the second-biggest cause of workplace deaths after car accidents, according to Bureau of Labor Statistics Data.
Billy Bardin, Dow’s global technology director, said that even with all the safety equipment and PPE that workers use while entering dangerous situations, such as confined spaces, the risk is high for injuries and fatalities.
He said that the company used robots for more than 1,000 confined-space entries in 2018, and for another 1,000 external inspections that involved high elevations.
“Drones save us downtime, save cost, save on productivity for our maintenance personnel,” Bardin said. “They eliminate having to put a person in that potentially hazardous environment.”