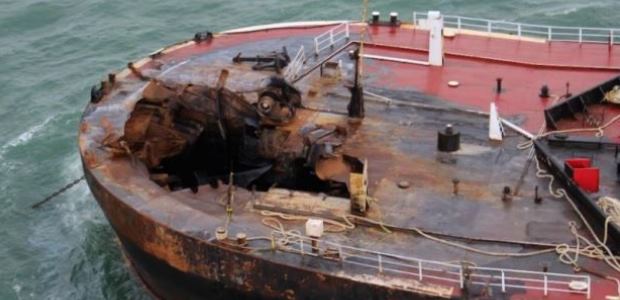
NTSB Cites Lack of Maintenance, Safety Management in Barge Explosion
The October 2017 explosion and fire involving the tug and barge Buster Bouchard/B. No. 255 off Port Aransas, Texas, killed two crewmen and caused $5 million in property damage.
The National Transportation Safety Board has released its report on the October 2017 explosions and fire involving the articulated tug and barge Buster Bouchard/B. No. 255 in the Gulf of Mexico off Port Aransas, Texas. The explosions killed two barge crewmen and the explosion and resulting fire caused $5 million in property damage. NTSB's report cites lack of maintenance and of effective safety management by Bouchard Transportation Co., Inc., operator of the barge.
A U.S. Coast Guard photo included in the NTSB report shows damage to the port bow of barge B. No. 255 after the explosion.
NTSB concluded the three explosions were caused by the ignition of flammable vapor that formed in a void space. The vapor was from crude oil that leaked into the void space from the number one port cargo tank through a corroded bulkhead. About 2,000 barrels of crude oil were discharged from the barge into the water or were consumed by the fire. The 468-foot-long barge, which had a capacity of 7.91 million gallons, sustained more than $5 million in damage and was scrapped after the accident, while the tugboat was undamaged.
According to the report, the void space was supposed to remain empty of ballast water or liquid cargo and contained an anchor chain locker, lighting circuits, and an electrical control box for the anchor winch. The barge crew did not routinely check the space or sound ballast tanks for leaks, and the company did not require the crew to check those areas of the barge, it says.
At the time of the incident, the barge was being used to transport 1.39 million gallons of crude oil to the Port of Corpus Christi. The explosion occurred about 4:30 a.m. as the crew were in the process of raising the barge's anchor.
The report says investigators found two through-cracks and other holes in the bulkhead between the [void space] and the no. 1 port cargo tank on barge B. No. 255, and the board concluded these were primarily a result of corrosion that existed prior to the accident and compromised the integrity of the cargo containment in the no. 1 port tank. Additional findings listed in the report include that Bouchard Transportation's safety management system and maintenance processes failed to ensure proper maintenance of the company's fleet of barges, including B. No. 255; Bouchard Transportation management failed to promote and ensure a safety culture in the company, which compromised the safety of both the vessel and the crew; Coast Guard marine inspectors who examined barge B. No. 255 prior to the accident failed to identify unsafe conditions, which allowed the vessel to continue to operate at increased risk to the crews, the environment, and port facilities; and the American Bureau of Shipping's survey program was ineffective in ensuring the safety of barge B. No. 255 and its crew. The lack of communication between the American Bureau of Shipping and the Coast Guard limited each organization's ability to assess the overall condition of the B. No. 255 and identify hazardous conditions, including the corrosion on the forepeak/port no. 1 cargo tank bulkhead, the board found.
"The series of failures documented during this investigation highlights the need for effective safety management systems, proper vessel maintenance, and thorough regulatory examinations," said NTSB Director of Marine Safety Brian Curtis. "If implemented, the recommendations issued as a result of this investigation will help to identify the failures that led to this accident and prevent similar casualties in the future."
The board's recommendation to Bouchard Transportation is that it evaluate the company’s safety management system (SMS) with an independent third party to identify the areas that allowed for the poor mechanical and structural condition of the B. No. 255 and revise the SMS to address any identified deficiency. To the Coast Guard and the American Bureau of Shipping, the board recommended that they establish joint policy and procedures to share information, including all results and findings from audits, surveys, examinations, inspections, and other applicable activities related to vessel safety.