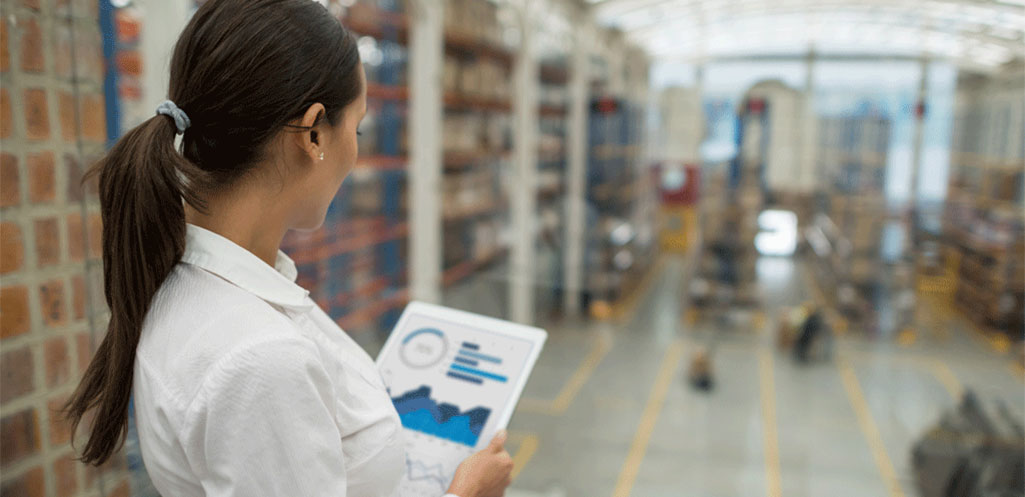
SPONSORED
How Ready is your Company for Industry 4.0?
Transform your Organization through EHS and Quality Automation
- By Kelly Kuchinski
- Apr 29, 2019
Organizations are increasingly looking for ways to transform their business so they can stay competitive, streamline operations and increase profits. Implementing Industry 4.0 technologies, such as Artificial Intelligence (AI), Internet of Things (IoT) and cloud technologies, are expected to support these objectives. Unfortunately, many manufacturers are struggling to start these projects when outdated processes are embedded in daily operations. To incorporate these technologies, companies need to look at their current infrastructure to determine what changes need to be made to develop a strong foundation for implementation success.
Setting the Groundwork
The first step is to determine the maturity of your “digital readiness” in the company. Manufacturers have seen the benefits of implementing enterprise IT systems, such Enterprise Resource Planning (ERP) and Manufacturing Execution System (MES), to increase efficiencies and centralize information. However, many other areas are still in the dark ages when it comes to automation. According to LNS Research, approximately 78% of manufacturers are still managing Environmental, Health, Safety and Quality (EHSQ) processes using paper-based or spreadsheet records. This results in data being outdated, incomplete and siloed in someone’s files or computer.
An Industry Digital Readiness study sponsored by Xerox, showed that employees waste more time on document workflows than core operations and responsibilities, making them less effective in the workplace. Over 80% of respondents expect digitization to streamline processes, improve document workflow and positively impact the bottom line. Now is the time for all manufacturers to join the 65% of businesses beginning to digitize paper-based processes and automate workflows in an EHSQ system.
By automating shopfloor processes in an enterprise EHSQ system, companies can eliminate paper-based records with electronic data, allowing it to be easily shared and reviewed for more transparency and operational intelligence. Now EHS and Quality processes can be properly recorded, managed and resolved to create a repository of information for preventive risk management.
Take an example of a chemical company where an outdated record was causing problems in operations. Some of the production lots were out of specification and had to be scrapped and costs were beginning to add up. An investigation was done to determine the root cause and it was discovered the production line manager on the third shift was adjusting the levels too high on the processing equipment. A month prior, raw materials were sourced from a new supplier and a management of change (MOC) was issued to adjust temperature settings during production to maintain the consistency of the product. The production manager was on vacation and not aware of the change and continued to use the outdated settings resulting in nonconforming finished product.
If the company had an integrated EHSQ system in place, alerts would have been issued through email notifications with links to the electronic MOC record and the company would have avoided costs of over $250,000 in scrap, additional production runs and expedited customer shipments.
The Benefits of Integrated EHSQ
When you first think about environmental, health, safety and quality management processes, it may look like there are not many similarities – let alone reasons to connect these departments. But looking a bit further, there are many advantages to linking these functions together in one platform.
Common processes
When you compare EHS and quality ISO compliance requirements (i.e. ISO 9001, ISO 14001 and ISO 45001) you can begin to see a number of common processes, including document control, audits, corrective actions and preventive actions (CAPAs) and MOCs. Whether you are addressing incidents in EHS or nonconformances in Quality, the terminology may vary but there are issues that need to be addressed to prevent a recurrence. And even Enterprise EHSQ solutions standardize these process workflows and compile data for better business decisions regarding risk management and operational excellence initiatives.
Shared resources
Common processes are not the only similarities in these systems. Often times when there is an issue - whether it’s EHS or quality - that needs to be investigated, you rely on the same shopfloor employees to support the resolution lifecycle. Having one system provides a consistent user interface and workflow so employees are not required to enter multiple systems to capture data that may affect safety and quality. This streamlines the process, eliminates the need for additional training and simplifies the user login process. It also provides a central repository of information that allows users to quickly access current standard operating procedures (SOPs) and MOCs to maintain facility processes and compliance requirements.
Single Source of Truth
Organizations who use an EHSQ solution can increase process and data collaboration through the integration of current and planned systems. When you integrate your EHSQ system with other IT systems and shopfloor devices, you begin to create a single source of truth that allows users to proactively manage the facility and identify risks across the shop floor, the enterprise and the supplier network. It also enables master data to be shared across systems for consistency and less data entry errors.
This centralized data allows users to create ad hoc reports to evaluate aggregated data values and drilldown to determine if trends or anomalies need additional analysis or corrective action. Instead of compiling information from separate data from different systems into an Excel spreadsheet for analysis, you have one system that can easily evaluate KPIs within the system in real-time.
Holistic Risk Management
Building on the single source of the truth, another advantage of an integrated EHSQ solution is the ability to develop holistic risk management programs to identify all relevant hazards and proactively monitor and control those risks to maintain employee health and safety, compliance requirements and product quality. A risk module can calculate risk through various points of a process and classify event history, possibility and level of risk, and risk mitigation. It integrates with CAPAs to manage and control those risks effectively and establish SOPs for critical and noncritical events. Now companies can manage their risks proactively and identify resolution plans early in the process to limit the impact on employees, the environment, product and the organization.
A recent example in the food industry showed the importance of an integrated EHSQ system. A company had to issue a food recall of one of their best-selling products when an employee tested positive for Hepatitis A. The recalled lots were produced over a two week period, but the recall wasn’t issued until three months later, so there was a high likelihood that the products were already consumed.
If the company had an integrated EHSQ system in place, management would have taken the employee out of the production area based on visual assessment or a regular occupational health (OH) screening. The reported incident would have been activated in the EHSQ system and alerted the production team to begin sanitation procedures on high risk areas. The Quality team would begin additional testing on other lots that could have been contaminated. Material could be quarantined until QA testing could confirm product safety. The Product and Customer Service teams could make sure contaminated lots did not ship to open orders. The Legal and Marketing departments would be issued alerts to identify risks to public safety and brand reputation. An integrated EHSQ solution can break down data silos to provide greater transparency and risk management to prevent an issue from entering the supply chain.
Choose a System that Grows with your Needs
Too often companies invest in large enterprise solutions that cost millions of dollars in licensing and services implementation fees. The system is configured to meet your organization’s needs today, however within a short period of time the system becomes outdated and unable to support new regulatory or business requirements. That’s why many companies are now looking at SaaS solutions to evolve with their business needs and challenges.
Look for a true SaaS solution that can easily be implemented within your facility. You want a solution that offers out-of-the-box best practices to enhance your operations while recording and managing nonconformances and incidents through the entire resolution process. While an on-premise or highly customized SaaS solution can support a company’s needs initially, they become antiquated without upgrades that require expensive implementation and services support – often costing as much as a new solution. But a true SaaS solution relies on Agile development and provides a continuous flow of new feature and function updates several times a year without additional charges so your business can use the latest and greatest tools to enhance their operations while not exceeding budget allocations.
Another advantage of using a true SaaS EHSQ solution is the ability to connect to the suppliers, contract manufacturers and contract packagers across the value chain. With half of all product recalls attributed to supplier and contract vendor issues, creating a more collaborative relationship will enhance product quality. Look for a solution that allows you to create a repository of supplier information including contact information, locations, product information, accreditations and other important data. This can be done through a secure supplier portal to enable the exchange of updated information as needed.
It also allows your company to include suppliers in the quality nonconformance resolution process. No longer will an audit leave the Quality manager with the response that the nonconformance was a supplier issue. Now there will be an electronic audit trail that traces back to the source of the problem, the root cause and Corrective and Preventive Actions (CAPAs) taken at the supplier location to resolve the issue going forward. It also builds better collaboration with the supplier to enhance the partner relationship as opposed to the time and cost associated with finding and onboarding a replacement vendor. And finally, reporting tools and dashboard reports can provide an overview of how all your suppliers are performing, how many nonconformances are open, and other key performance indicators (KPIs) that are important to your organization.
Closing Thoughts
Taking the steps to build a solid foundation of automation and integration of systems and shopfloor processes creates a comprehensive data-driven organization that finally achieves full transparency across the facility, enterprise and value chain. The efficiencies of an integrated EHSQ system will streamline processes, enable transparency for better business decisions and reduce operational costs and risks. Organizations can then begin to identify how new technologies, such as AI and IoT, can be added to drive further efficiencies and enable greater competitive advantage in an ever-changing global marketplace. Now is the time to change the way you do business.