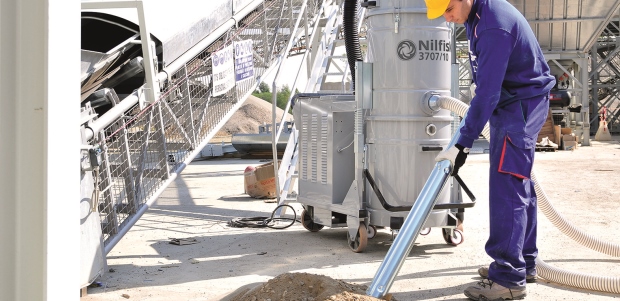
Three Dangerous Misconceptions Surrounding OSHA's Silica Dust Standard for General Industry
On June 23, most provisions of OSHA's silica standard for general industry became enforceable. Many employers still have a long way to go to achieve full compliance.
- By Stephen Watkins
- Sep 01, 2018
Although the dangers of respirable crystalline silica have been known for more than 80 years,1 silica dust has only recently begun to be recognized as the major health hazard it is. In fact, silica is now frequently referred to in safety circles as "the new asbestos."
However, despite the fact that the risks are well known, many employers still haven't taken the steps required for compliance. These steps include measuring worker exposure, implementing controls to keep exposure below the specified limits, and verifying that those controls work.
In talking with our customers as well as outside safety consultants, we've learned that one reason many general industry employers still haven't complied is that they don't entirely understand the new standard and how it applies to them. This lack of understanding has led them to develop misconceptions that can be dangerous for everyone involved — dangerous for employees who aren't being adequately protected from silica dust and dangerous for employers who aren't prepared for inspectors to knock on the door. Let's clear up a few of these misconceptions.
"I'm aware of all of the silica dust hazards in my operations."
In an interview earlier this year, safety consultant Abby Ferri told Nilfisk that she's had several experiences where she was called in to perform silica safety training, but when she arrived at the facility, she realized that the employer didn't have a clear picture of what activities were generating exposures and which workers were exposed.2 This is because the employers hadn't yet taken the first step of examining their operations and performing exposure assessments.
The standard provides two options for an exposure assessment:3
1. Performance option. Employers can measure the 8-hour time-weighted average (TWA) exposure for each employee using either air monitoring data or objective data. Objective data can be from industry-wide surveys or calculations as long as it "reflect[s] workplace conditions closely resembling or with a higher exposure potential than the processes, types of material, control methods, work practices, and environmental conditions in the employer's current operations."
2. Scheduled monitoring option. Employers can perform initial monitoring to measure the 8-hour (TWA) for each employee using "personal breathing zone air samples that reflect the exposures of employees on each shift, for each job classification, in each work area." This initial monitoring is followed by subsequent monitoring every three or six months, depending on the result of the initial test. The scheduled monitoring option also provides a representative sampling method for groups of employees who all perform the same tasks on the same shift and in the same place.
Regardless of which option you choose, the sampling will most likely need to be done by an industrial hygienist using personal sampling pumps fitted to each employee.4 After the samples are collected, they need to be sent for laboratory analysis. Appendix A of the standard specifies procedures for analyzing the air samples.
Until you follow these steps, it's impossible for you to have an accurate picture of the silica dust hazards that exist in your operations. Without this full picture, you can’t guarantee that any controls you implement will mitigate your employees' safety risks.
"I just need to provide respirators."
The new general industry standard sets the permissible exposure limit (PEL) for silica at 50 µg/m3, calculated as an 8-hour TWA. That's roughly half of the previous PEL. This drastic reduction is more than what can be accomplished using respirators alone.
There are several reasons respirators aren't as protective or as practical as engineering controls. First, they need to be selected and fitted for each individual. There is no acceptable one-size-fits-all approach. For example, a 2016 article in Safety+Health magazine addressed the challenges of fitting respirators for men who have facial hair, particularly during cultural events like Movember (aka No Shave November).5 And while there have been great strides in protective equipment for women, many women are still injured on the job because their PPE isn't available in an appropriate size.6
Respirators also need to be maintained correctly—they won't work if the HEPA filter is clogged. And they need to be worn properly and consistently, which, unfortunately, they aren't because, as OSHA notes, they can be uncomfortable (especially in high-temperature areas).
For these reasons and more, respirators simply aren’t enough. The only way to ensure that employee exposure is kept below the PEL is by implementing the required engineering and work practice controls to reduce employee exposure to silica dust. This includes proper housekeeping using a HEPA-filtered vacuum cleaner.
"OSHA will be lenient."
The Trump administration’s focus on deregulation has had an impact on new worker safety laws. We've seen multiple delays to standards already adopted as well as standards-in-progress being dropped from the regulatory agenda. This has led some employers to take a more relaxed view toward compliance in the hope that OSHA will be more lenient.
However, those hopes have not come to fruition. In 2017, the number of OSHA inspections increased for the first time in five years. This was despite the fact that there were fewer OSHA inspectors.7
On the silica front, general industry employers can look to what has happened in the construction industry, where a silica dust standard became enforceable last September. A Bloomberg analysis of the first six months of the standard's enforcement found a total of 116 citations.8
Here are the top three reasons companies were cited:
- Failing to measure silica exposure levels (35 violations)
- Failing to follow the procedures on Table 1, as well as the required engineering and work control methods and respiratory protection (31 violations)
- Lack of a written exposure control plan (20 violations)
Overall, 80 percent of the violations were considered serious, which means they posed an immediate threat to workers.
It's likely that the number of citations issued for silica dust violations will increase with time. First, during the first 30 days of enforcement for the construction industry, a "good faith" provision was in place, meaning that inspectors didn't issue citations to employers demonstrating an effort to comply (a good faith provision is also in place for general industry). In addition, September through April isn't exactly peak construction season. And, finally, inspectors have up to six months after an inspection to issue a citation, so it's possible that more violations will be associated with inspections performed during that time.
These data suggest that OSHA has not been lenient on the construction industry. And although we won't know for sure until the citations begin appearing, it's likely that the agency will be even less lenient on general industry because inspectors have already had the opportunity to get used to the new rule and its enforcement. (OSHA is currently operating under an interim enforcement guidance,9 which details inspection and citation guidelines.)
If you work in an industry where silica dust is present,10 it's imperative that you understand the requirements and your responsibilities under them. Misconceptions like the ones above put your workers as well as your business at risk.
References
1. Video: "Stop Silicosis." U.S. Department of Labor. https://www.youtube.com/watch?v=GtYErK9KjQ8
2. "Safety Consultant Abby Ferri on How to Comply with OSHA's Silica Rule for General Industry." Nilfisk. https://news.nilfiskcfm.com/2018/05/safety-consultant-abby-ferri-on-how-to-comply-with-oshas-silica-rule-for-general-industry/
3. "§1910.1053 Respirable crystalline silica." OSHA. https://www.osha.gov/silica/SilicaGeneralIndustryRegText.pdf
4. "Personal sampling or air contaminants." OSHA. https://www.osha.gov/dts/osta/otm/otm_ii/otm_ii_1.html#appendix_II_9
5. "Facial hair and respirator fit." Safety+Health magazine. http://www.safetyandhealthmagazine.com/articles/14401-facial-hair-and-respirator-fit
6. "Trends in ... women's PPE." Safety+Health magazine. http://www.safetyandhealthmagazine.com/articles/16194-trends-in-womens-ppe
7. "Number of OSHA workplace safety inspectors declines under Trump." NBC News. https://www.nbcnews.com/politics/white-house/exclusive-number-osha-workplace-safety-inspectors-declines-under-trump-n834806
8. Silica Safety Enforcement Ramps Up at Construction Sites. Bloomberg. https://www.bna.com/silica-safety-enforcement-n57982091432/
9. "Interim Enforcement Guidance for the Respirable Crystalline Silica in General Industry/Maritime standard, 29 CFR 1910.1053 – June 23, 2018, Enforcement Date." OSHA. https://www.osha.gov/laws-regs/standardinterpretations/2018-06-25
10. "A Quick Overview of OSHA’s Silica Dust Rule for General Industry and Maritime." Nilfisk. https://news.nilfiskcfm.com/2018/04/a-quick-overview-of-oshas-silica-dust-rule-for-general-industry-and-maritime/
This article originally appeared in the September 2018 issue of Occupational Health & Safety.