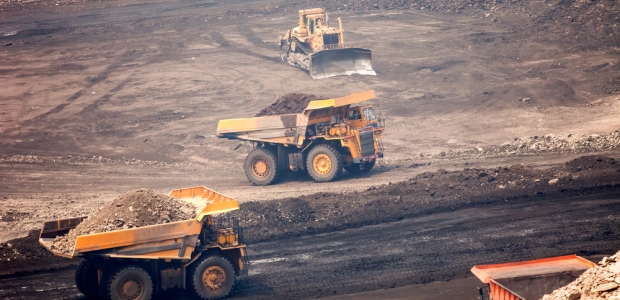
MSHA Seeks Data on Technologies, Controls to Boost Safety
The agency's Request for Information focuses on reducing accidents involving mobile equipment at surface mines and belt conveyors at surface and underground mines. It says MSHA is also considering the role of various engineering controls.
The Mine Safety and Health Administration is asking for data on technologies and controls that can improve safety conditions at U.S. mines. Its Request for Information focuses on reducing accidents involving mobile equipment at surface mines and belt conveyors at surface and underground mines but says MSHA also is considering the role of various engineering controls to increase the use of seat belts, enhance equipment operators’ ability to see all areas near the machine, warn equipment operators of potential collision hazards, prevent operators from driving over a highwall or dump point, and help prevent entanglement hazards for those working near moving or re-energized belt conveyors.
The RFI was published on June 26. To comment, visit https://www.regulations.gov and search for docket number MSHA-2018-0016. Comments should be identified with “RIN 1219-AB92” and are due within the next 180 days.
"The Trump Administration is committed to the health and safety of America's miners. Through the deployment of modern technologies, such as proximity detection, we can help ensure that miners return home safely at the end of their shifts," said Assistant Secretary of Labor for Mine Safety and Health David Zatezalo. "MSHA is also interested in learning more about how seat belts can be more widely used in mining operations to prevent injuries."
Mobile equipment at surface operations includes bulldozers, front-end loaders and trucks; belt conveyors are used to transport materials in surface mines and in underground mines. The RFI is part of a larger initiative that MSHA is undertaking to reduce accidents involving powered haulage and belt conveyors.
MSHA also will hold stakeholder meetings (the dates and locations will be announced at a later date), will provide technical assistance, and will develop best practices and training materials to raise awareness of hazards related to mobile equipment and belt conveyors.