
Page 2 of 4
Tips for Creating a More Successful Industrial Hygiene Program
OSHA defines industrial hygiene as "the practice of anticipating, recognizing, evaluating and controlling workplace conditions that may cause workers' injury or illness." That's the kind of definition that read one way can seem general, and when read another way, can seem overwhelming. There's a lot to unpack when it comes to industrial hygiene—and a lot that employers simply must get right. Let's review the basics of industrial hygiene and strategies for making sure your company has a successful program.
Getting Started: Risk Analysis
Industrial hygiene, like so much else in EHS management, really begins with good risk analysis. We can't protect employees from hazards in the workplace unless we first identify them. One of the most effective methods is to break jobs into a manageable number of tasks (try for no more than 10), work with and observe employees conducting these tasks, and pay close attention to the actual and potential hazards. Be sure to include chemical exposure hazards, biological hazards (e.g., mold), and physical hazards (ionizing and nonionizing radiation, vibration, illumination, temperature, noise) and to assess both routine and non-routine jobs.
Also, don't overlook these commonly ignored hazards in your evaluation:
- Hazards from beautification/renovation: Many paints used on factory floors and walls contain solvents and other chemicals with established OSHA exposure limitations—for instance, topcoats and primers often contain methyl methacrylate. Renovation and construction projects can also generate hazards such as noise or nuisance dust.
- Naturally Occurring Radioactive Materials (NORM): The name says it all—this is radioactive material found naturally within the earth, and it's easy to overlook for exactly that reason. NORM often rises to the surface as a byproduct of oil and gas production and can become concentrated on production strings, flowlines, pipelines, and other equipment. So, for instance, if you operate "pump shops" that clean and service oil exploration field equipment that may come into contact with NORM, your employees may have exposure risks.
- Short-term exposures: Sometimes when evaluating potential exposures, we miss exposures from processes that are conducted for short durations of time, especially when they're not conducted daily. For example, there may be a cleaning solvent that is occasionally used on process tanks, and the entire duration of exposure may be under 20 minutes, but sufficiently high concentrations during that time may pose exposure risks.
Once hazards are identified, introduce controls to limit exposures or reduce the consequences of exposure. Remember to use the hierarchy of controls (see Figure 1) as a guide to remind the team that eliminating the hazards is always the best option and that you must resort to personal protective equipment such as respirators only after more effective controls have not reduced exposures to acceptable levels. Remember, if you provide respirators other than voluntary use varieties, you will need a formal Respiratory Protection Program.
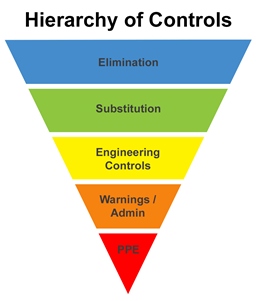
Figure 1
Similar Exposure Groups
A similar exposure group (SEG) is a group of employees who have common risks and similar exposure profiles. Use of SEGs can help streamline your IH program. You can define a SEG based on knowledge of the activities employees conduct, expecting that similar tasks with similar regularity will result in similar exposures (qualitative approach), or you can define them based on direct exposure measurements (quantitative).
The best option is to use an integrated approach that begins with determining which employees conduct similar tasks with common exposure risks, then to validate that with direct exposure monitoring and adjust the SEGs as needed based on the results. For best results, determine SEGs based not just on a review of records, but on direct observation of the work environment, with participation and feedback from employees.
IH Sampling Protocol
Now that you've identified hazards for job tasks and defined SEGs, you need a good sampling protocol. The key here is to make sure you’re accounting for all types of chemicals, workplace hazards, and exposure durations you’ve identified up to this point. Consult available sampling guides to identify established exposure guidelines for chemicals, including the OSHA Permissible Exposure Limit (PEL), the NIOSH Recommended Exposure Limit (REL), and the ACGIH Threshold Limit Value (TLV), all of which are 8-hour time-weighted average (TWA) exposure limits. While the PEL is the only limit among these that is federally enforceable in the United States, consider the best practice of keeping 8-hour TWA concentrations below the TLV and PEL, which tend to be lower.
Don't forget to review the potential for short-term exposures identified during risk analysis, and plan sampling to compare with any applicable limits such as:
- OSHA Short-Term Exposure Limit (STEL): A time-weighted average over a short duration of time, usually established as 15 minutes. Note: If you use methylene chloride, you should know that OSHA's methylene chloride standard states that you must sample for the STEL.
- Lower Explosive Limit (LEL): The lowest concentration (as a percentage) of a gas or vapor in air capable of producing a flash of fire in the presence of an ignition source. Obviously, concentrations above the LEL even for a short time are extremely dangerous.
- Immediately Dangerous to Life and Health (IDLH): Exposure which is likely to cause death or immediate or delayed permanent adverse health effects or prevent escape from such an environment.
For hazards not associated with chemicals, such as noise, make sure you're also accounting for processes that involve short-term exposures, such as periodic start-up of noisy equipment, as well as those that generate more consistent, predictable levels of hazards throughout the workday.
When planning the sampling protocol, take special note of the sampling methods you will need. For instance, when sampling for respirable silica, you must use a cyclone attachment and a low-flow sampling pump. Make sure you also know which analytical method to use in advance of the sampling, to avoid delays in completing the chain-of-custody form for the samples when it’s time to send them in for analysis.
Communicating Results
After you've received your analytical results, communicate results to the affected employees. There are some specific OSHA requirements regarding timing, depending on the standard and affected industries. For instance, the recent silica final rule states that employers must provide employees with the results of monitoring and information about any corrective actions taken within five working days in construction or 15 working days in general industry and maritime.
Formal requirements aside, sharing sampling results just makes good sense. It ensures that employees have information they need to work safely and fosters an environment of trust needed for an effective EHS culture.
Managing Change
To be impactful, your sampling protocol must reflect the risk analyses for all operations as they exist today. This means that when changes are planned, you need to identify the ways these changes may affect employee exposures. These changes can include operational changes, for example installation of new equipment such as ovens, printing presses, or machining equipment, or facility changes, such as plant renovations.
Have a formal process for identifying the impact of changes, so that hazards can be identified at every step and proper controls identified. The number of approvals that need to be documented can be overwhelming, so it might be wise to explore management of change software solutions that can easily route approvals, remind approvers, and maintain an audit trail. If the system includes a method to inform the appropriate people to review IH implications of the plans and update the protocol accordingly, you’ll be much more likely to be able to keep your IH program aligned with your current operations.
Reality Intervenes: A Word About Funding
The reality of running EHS programs is that money is often a stumbling block. Companies often see EHS as a "cost center," but even in the best cultures, funding can be a challenge.
Make sure you're factoring in enough money for effective IH sampling in your annual budget. You may identify a need to expand your IH sampling protocol due to planned changes. You may also need to perform types of sampling you've never conducted before, such as noise dosimetry, if warranted by review of new processes. If you obtained any sampling results over established enforceable limits such as the PEL, you'll need to take corrective actions and re-sample. Make sure you're budgeting enough extra funds to cover these kinds of additional sampling.
Closing Thoughts
Industrial hygiene has many dimensions, and to do it well, you need the proactive involvement of your entire workforce. Fortunately, there are EHS software solutions that can significantly simplify the management of many of these tasks, such as conducting Job Safety Analyses (JSA), Management of Change (MOC) workflow, Risk Assessments, and Corrective Actions. With the right strategies and tools, you'll overcome the challenges and create an industrial hygiene program that protects your most important asset—your employees.
This article originally appeared in the May 2018 issue of Occupational Health & Safety.