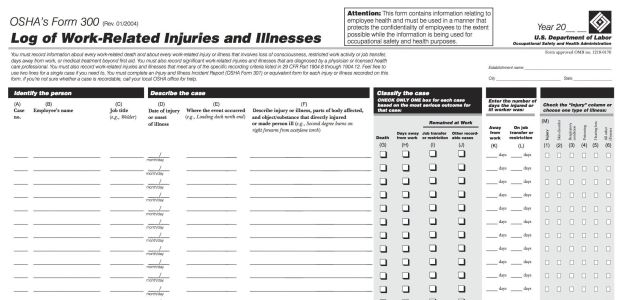
OSHA Electronic Injury Reporting App Available Aug. 1
Establishments with 20-249 employees that are classified in certain industries with historically high rates of occupational injuries and illnesses -- they include construction, utilities, agriculture, and many more -- will have to electronically submit information from OSHA Form 300A.
OSHA is launching the Injury Tracking Application on Aug. 1 to help employers who are affected by OSHA's rule requiring electronic submission of injury and illness data. The online form allows employers to electronically submit required data from their completed 2016 OSHA Form 300A; OSHA has extended the deadline for submitting 2016 Form 300A to Dec. 1, 2017, so affected entities have enough time to familiarize themselves with the electronic reporting system and to give the Trump administration an opportunity to review the new electronic reporting requirements before they are implemented.
The data submission process involves four steps: 1) Creating an establishment; 2) adding 300A summary data; 3) submitting data to OSHA; and 4) reviewing the confirmation email. According to OSHA, the secure website offers three options for data submission. One option will enable users to manually enter data into a web form, another option lets users upload a CSV file to process single or multiple establishments at the same time, and a third option will allow users of automated recordkeeping systems to transmit data electronically via an application programming interface.
Establishments with 250 or more employees that are currently required to keep OSHA injury and illness records must electronically submit information from OSHA Forms 300 (Log of Work-Related Injuries and Illnesses), 300A (Summary of Work-Related Injuries and Illnesses), and 301 (Injury and Illness Incident Report), and establishments with 20-249 employees that are classified in certain industries with historically high rates of occupational injuries and illnesses -- they include construction, utilities, agriculture, and many more -- must electronically submit information from OSHA Form 300A.
The requirement becomes effective Jan. 1, 2017.