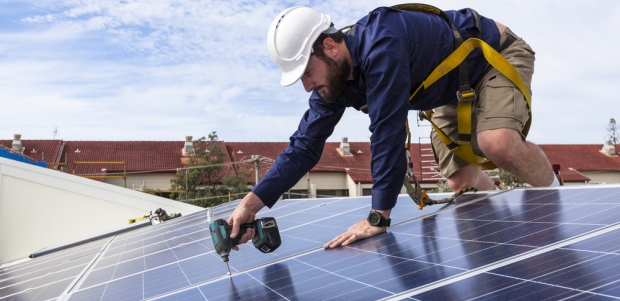
Job Hazard Analysis Process Redesign: Integration of Job Hazard Analysis and Work Planning Processes
Integrating the JHA and Work Planning processes reinforced the new philosophical approach for shifting responsibility for working safely to those responsible for planning and actually performing the work.
- By Randy Hancock
- Jul 01, 2017
Job Hazard Analyses (JHAs) are used throughout industry in a variety of forms and formats. Typically performed in advance of accomplishing a particular task, they identify potential hazards and recommend mitigation to control the hazards. Consequently, they are an important tool in ensuring work is accomplished in a safe manner.
A large employer was recently struggling to implement a JHA program. They had a number of shops, each with specialized equipment, tools, and expertise. Given this environment, it was important that the company get their implementation right. Their approach was basically a sound one: First, each shop was to prioritize their tasks according to what they thought was their greatest risk. Once this was done, JHAs would then be prepared in order of that priority. When completed, a catalogue of generic JHAs would exist covering each shop’s routine tasks. As engineers planned work, the JHAs would be referenced for hazard controls and mitigations. Hazard controls were to be inserted in Work Planning documentation, and the Safety Department would review these documents to ensure they were properly incorporated—a straightforward approach.
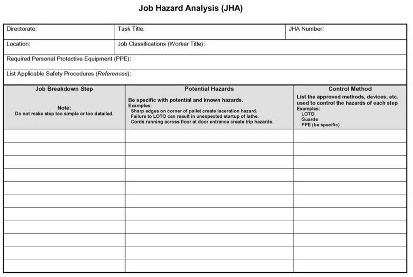
But once this program was rolled out, it became apparent that implementation would not be as easy or straightforward as originally thought. It was hard to convince management to provide the necessary resources to prepare large batches of JHAs for future work that may, or may not, ever materialize. With only a partial catalogue of JHAs to drawn from, there were few consistent hazard controls available for engineering to reference when preparing Work Plans. The result was that hazard controls were inserted into the plans, but they were not based on any analysis. Consequently, the level of detail and completeness of the plans varied widely. When the Safety Department reviewed them for approval, rejection/rework was common. Engineering personnel responsible for Work planning were frustrated with having to constantly rework their documents; the Safety group was, in turn, frustrated that the JHAs were not completed and reflected in the Work Planning documents. It was clear that a new approach was needed.
Guiding Principles:
|
Work done properly is work done safely.
|
The Safety team's role is to support personnel in achieving the goal of safe, error-free performance of work.
|
A new strategy for preparing JHAs was introduced. It reflected a different philosophy for how safety was to be accomplished for this company. It emphasized safe, error-free performance of work—i.e., that work done properly meant work was also done safely. Safety was to be treated like any other component of properly executed work—i.e., just as engineers planned for the appropriate personnel, tools, and resources to properly accomplish the task at hand, Safety should also be planned into the job. This approach addressed a faulty assumption that is present in many companies and organizations: that safety is the responsibility of the Safety Department. This company’s philosophy shifted the responsibility for safety to those charged with getting the work accomplished and shifted the Safety team’s role to one where they supported the engineers and technicians in achieving the goal of error-free—and therefore safe—performance of work. Safety department personnel would serve as technical consultants for interpreting and applying safety requirements and also verify compliance with those requirements. As stated, this philosophical approach drove a number of changes in how JHAs would be accomplished.
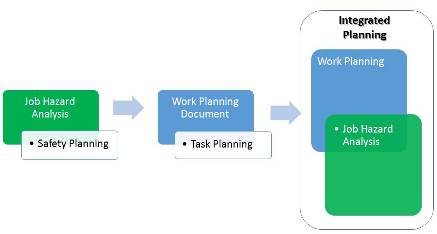
First, instead of treating JHAs and work planning as separate efforts, the two were combined. The Safety function became a part of the Work Planning process alongside the other elements of properly executed work.
The Work Planning document template was modified to include a basic JHA form. The JHA was incorporated near the beginning of the document to help ensure it is accomplished early in the Work Planning process. As the figure (below) shows, it includes three columns to identify the hazard, its mitigation, and a reference for the mitigation. Once the JHA portion of the Work Planning document is completed, the engineer responsible for Work Planning continues by describing specific work steps (not shown in the figure below).
Using a job that requires the use of a ladder to access an electrical panel as a simple example, the engineer might first identify "Fall Hazard" on the Work Planning document. It is noted in the "Hazard" column of the JHA section. The "Hazard Mitigation" might be something like, "Use fall protection gear." The "Mitigation Reference" might be "CFR 1926.502" (as an example). The Work Planning engineer would probably also list an "Electrical Shock" hazard. The "Hazard Mitigation" could be "Use lockout/tagout" and the "Mitigation Reference" could be "CFR 1910.147." For simple tasks, such as our example, these two entries might be the entire JHA. As the Work Planning engineer prepares the specific work steps, he/she will include detailed controls for working at heights and lockout/tagout.
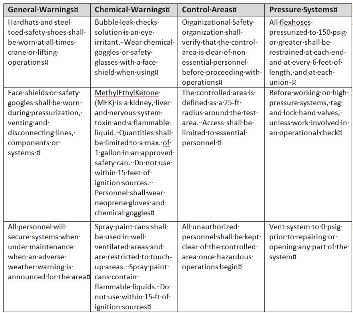
Input was solicited from engineers responsible for preparing Work Planning documentation. Involving them in the process helped avoid the earlier problems with implementation and greatly reduced the barriers to implementation and required training. In some cases, including a "Note," "Warning," or "Caution" might be preferable to writing detailed controls into specific work steps. In order to standardize the wording of "Notes," "Warnings," and "Cautions," a "library" was prepared (by subject area) for engineers to use in preparing Work Planning documents. The library covered a broad range of commonly encountered conditions and circumstances, including chemicals, high-pressure gases, etc.
The reception was very positive. JHAs are now prepared on an "as needed" basis, rather than for tasks that may be done at some point in the future. Each task has a JHA prepared specifically for it, and the JHA is prepared as part of the Work Planning process. And, most importantly, integrating the JHA and Work Planning processes reinforced the new philosophical approach for shifting responsibility for working safely to those responsible for planning and actually performing the work.
This article originally appeared in the July 2017 issue of Occupational Health & Safety.