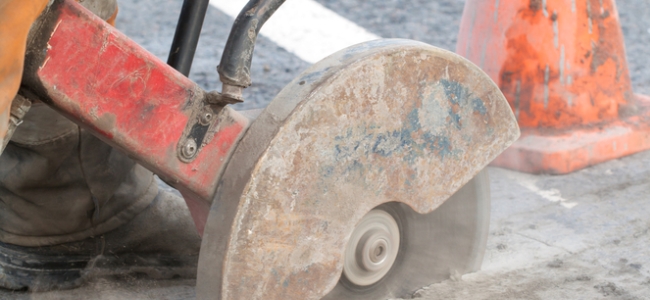
Essential Elements of Worker Protection
The more information you have about your own organization and workforce, the better the insight into how to reduce hazards to an acceptable level.
- By Langdon Dement
- Feb 01, 2017
Every day, millions of people work in environments with hazards that can cause illness or even death. Many of these hazards—which can include a range of issues, such as chemical vapors, extreme temperatures, and poor ergonomic design—might not cause immediate adverse health effects but can cause life-altering problems over time. Furthermore, many workers might not fully grasp the magnitude of the issues around them. A simple yet recurring exposure to a hazard could lead to something as serious as silicosis or a permanent hearing impairment. That’s why understanding what chemicals, stressors, and adverse conditions are present in the workplace and how to mitigate those hazards provides important tools in reducing many workplace injuries and illnesses.
This is where industrial hygiene (IH) comes in to play. The definition of IH itself describes its importance. According to the American Industrial Hygiene Association (AIHA), IH is "the science and art devoted to the anticipation, recognition, evaluation, prevention, and control of those environmental factors or stresses arising in or from the workplace which may cause sickness, impaired health and well-being, or significant discomfort among workers or among citizens of the community."
In order to anticipate, recognize, evaluate, prevent, and control environmental factors or stresses in the workplace, it’s important to create a work site analysis. This initial step is crucial in determining what jobs and workstations are potential sources of problems for the employee and environment. During the analysis, the industrial hygienist will measure and identify exposures, problem areas/tasks, and risks associated with them.
In your own organization, think of the importance of understanding all aspects of the workplace, including who works where and for how long. Does a specific job task in your organization require a worker to spend a continuous amount of time dealing with dusts, chemicals, or even excess noise? Do certain workers perform more of these potentially hazardous tasks than do others? The more information you have about your own organization and workforce, the better the insight into how to reduce hazards to an acceptable level.
This is where the overall health and safety culture plays a pivotal role for an organization. Many times, organizations just want to maintain "compliance." They don't consider other steps that need to be made to create value for health and safety. Ultimately, focusing only on compliance is not going to motivate workers to value health and safety, nor will it organization as a whole. For example, why do we want employees to wear hearing protection? Is it because their ears are cold or because they have to? Or is it because we want employees to be healthy and safe when they return home? When we move past "compliance" to "risk management" and eventually to "continual learning," we have made essential progress in keeping workers healthy and safe both on and off the job.
Consider OSHA's new rule on respirable crystalline silica. The ultimate goal of this rule is protecting workers by reducing hazardous levels of silica (found in rock, concrete, sand, and many other materials), which can lead to lung cancer, silicosis, chronic obstructive pulmonary disease, and kidney disease. Approximately 2.3 million workers exposed to this chemical yearly, so ensuring their health, however the means, should be a priority in any organization. The new rule will assist in reducing this exposure through a number of key provisions:
- Reducing the permissible exposure limit to 50 micrograms per cubic meter of air over an eight-hour shift;
- Requiring employers to use engineering controls, provide respirators when engineering controls cannot adequately limit exposure, limit worker access to high-exposure areas, develop a written exposure control plan, offer medical exams to highly exposed workers, and guarantee workers have been properly trained on silica;
- Providing medical exams to monitor highly exposed workers; and
- Providing flexibility to help employers protect workers from silica.
Although this new rule might be challenging and potentially expensive for organizations to implement, remember the real reason it's being changed: to protect our employees.
Recordkeeping's Key Role in Industrial Hygiene
Maintaining records is also essential for industrial hygiene. Think about this scenario: "After 15 years of work, an employee has developed silicosis. During their time of employment, how often has the individual been exposed to silica? Has it been regular exposure or intermittent? Have controls been in place the whole time?"
Questions like these can be answered by a simple yet effective recordkeeping system. In addition, it's beneficial to be able to recall previous assessments that have been conducted throughout the facility. Having the ability to look at the historical records of IH sampling for a specific job task or area aids the organization in:
- Following certain regulations where required;
- Assessing whether the job tasks/area has improved or declined in hazards present;
- Increasing program effectiveness; and
- Mitigating legal threats that may arise.
Additionally, industrial hygiene management systems have the ability to assist organizations in ways such as:
- Simplifying tracking and recordkeeping;
- Managing qualitative and quantitative exposures;
- Managing IH equipment with calibration data; and
- Integrating EHS processes with other departments.
Hazards are present in all organizations, so understanding best practices to minimize hazards and reduce them to acceptable levels is crucial for every workplace. Having and utilizing a proper IH management system will set your organization apart and will empower you to keep your employees safe. Ultimately, as health and safety professionals, we should have one foremost goal: to keep workers, their families, and the community healthy and safe.
This article originally appeared in the February 2017 issue of Occupational Health & Safety.