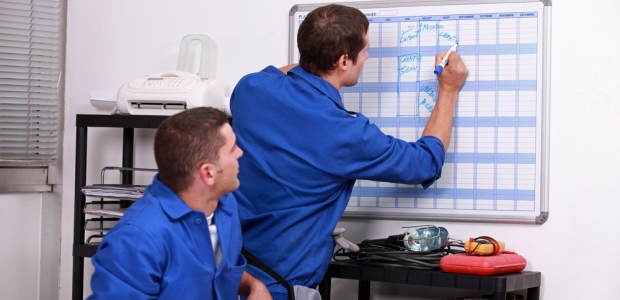
Impact: Developing an Attitude for Safety
If workers are overly optimistic that no injuries will befall them, they may be more likely to take risks that could end up in injuries.
- By Dennis Knapp
- Aug 01, 2016
Investigating why some workers do not wear eye protective in certain industries—such as professional cleaning where workers handle potentially dangerous chemicals every day or workers in construction, warehousing, or factories—what was uncovered as one of the key reasons was, very simply, they do not like the design and appearance of traditional protective eyewear. This ranked ahead of such issues as comfort, which was also a concern.
Addressing these issues, at least one manufacturer redesigned many of its protective eyewear offerings so that they were more fashionable looking, while still offering optimal protection, and it appears this strategy has been successful.
Unfortunately, when it comes to wearing protective gear—apparel, aprons, wrist sleeves, etc.—in warehouses, industrial facilities, and construction sites, there are more and bigger issues that must be addressed. In too many cases, there is an "attitude" against wearing protective clothing. Some of these attitudes include the following:
Invincibility: This appears to be more prevalent in rural areas of the country and among younger and older workers. They may be aware of the dangers—and hopefully they have been educated on the potential physical harm their work can cause—but they simply do not believe a workplace accident will happen to them. As a result, these workers tend to not wear protective apparel.
It occurs in rural areas of the country because there is often a "Wild West" mentality. Younger workers always seem to take more risks, if for no other reason than they have not witnessed injuries on the job, either their own or fellow workers'. As for older workers, some have been performing these tasks for 10, 20 years or more. These workers tend to develop a false sense of invincibility at the workplace.
Company size: Many times employees at smaller companies believe that workplace injuries are more prone to happen at larger firms instead of at smaller firms that might just be called in to complete a specific project, for instance. Very often, smaller companies' workers don't wear protective gear because the thought is that workers at larger firms are on site every day, which increases their risk of a job-related injury. This is a naïve approach that so often results in injury. Additionally, there may be situations where a smaller firm, for a variety of reasons, has not placed enough priority on educating its workers on job safety issues.
Too optimistic: Another misleading attitude for not wearing protective gear is that some workers believe unfortunate events—like a job-related injury—simply do not happen to them. This somewhat parallels the invincibility reason addressed earlier, but being too optimistic has more serious implications. If workers are overly optimistic that no injuries will befall them, they may be more likely to take risks that could end up in injuries.
Comfort: A big problem is that many workers have an attitude that all protective apparel is uncomfortable. This becomes a much bigger issue in the summer months. Even workers who do wear protective clothing during other times of the year will start complaining about it when the weather turns hot and humid. One construction company in Louisiana, which is famous for its hot summers, sends out emails and adds posters at its work sites during these months, reminding workers to "stay covered" and avoid rolling up protective sleeves or removing protective apparel until they are in a safe location.
Addressing These Attitudes
The only way to address most of these "attitudes" is with education. It can be tough because what we are dealing with is actually more than an attitude. Employers and managers are dealing with a culture that says essentially, "work injuries do not happen to me."
We don’t want to scare workers into wearing protective apparel, but we must keep reminding them of the need to wear such garments and the potential dangers of their work. Another step is to follow the lead of the Louisiana company mentioned earlier. Emphasize safety in emails to workers and on posters, and have training programs on how to properly wear protective gear.
Another critical consideration involves the protective wear selected. For instance, when the worker's back and shoulders are hot, it can make his or her entire body feel hot. Some manufacturers of protective apparel are well aware that heat is an issue when wearing these garments. To address this, they make their garments more breathable and add back panels made of polypropylene, which keep the user cooler.
Ultimately, when it comes to the wearing of protective clothing, our goal is twofold: First and foremost, we want the protective clothing to help prevent injuries to our workers and keep them safe. Second, we also want to improve morale and worker productivity. A safe, comfortable worker is the most productive worker.
This article originally appeared in the August 2016 issue of Occupational Health & Safety.