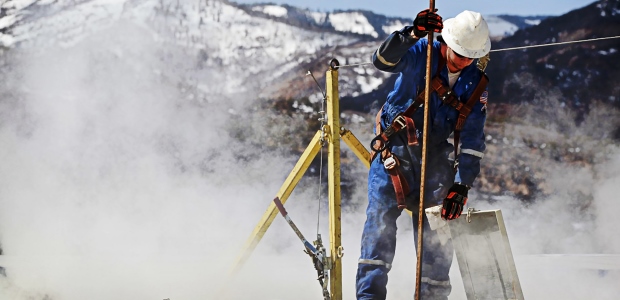
Page 2 of 4
This Is Not Your Grandfather's Glove: Hand Protection in the Age of Performance Gloves
I will always remember how my grandfather was missing half of his left pinky finger. It's just something I can't forget. He lost half of his finger at work at the age of 50 when a 55-gallon drum of ice cream rolled over his hand. I always admired how he made the best of the situation, and he repeatedly spoke about his work-related injury, so his story went down in the family lore.
Like 70 percent of workers today who suffer from hand injuries, my grandfather was not wearing safety gloves when he sustained his injury. And like 30 percent of workers today, even if my grandfather were wearing a glove, most likely the gloves "were inadequate, damaged or wrong for the type of hazard," according to a study conducted by the U.S. Bureau of Labor Statistics (BLS).
Plus, the technology of composite engineered yarns and steel for cut resistance and Thermal Plastic Rubber (TPR) overlays for impact resistance simply didn’t exist during my grandfather's time as it does today—in the age of performance gloves. Fortunately for workers today, performance safety gloves are engineered with technological advances that aid in extra protection, dexterity, durability, and comfort.
Ouch! The Statistics & Cost of Hand Injuries are Staggering
In today's work environment, let’s not forget that hand injuries are the second leading cause of work-related injury—back and neck sprains and strains take first place. The most common causes of hand injuries are blunt trauma, followed by cut and laceration injuries from a sharp object, which account for one-third of hand injuries.
A human hand consists of:
- 27 bones—including the eight wrist bones
- Major nerves, including the ulnar, median, and the superficial branch of the radial nerve
- Arteries, veins, muscles, tendons, ligaments, joint cartilage, skin, and fingernails
Because our hands have an intricate structure and a complex anatomy, the potential exists for a variety of injuries. Human hands are truly amazing and are definitely worth protecting properly. The cost of a hand injury can far exceed the cost of a hand protection safety program.
BLS reports that today, the average hand injury claim exceeds $6,000, coupled with a typical workers' compensation claim of $7,000—for a total of $13,000. Plus, the National Safety Council reports the following costs for typical injuries:
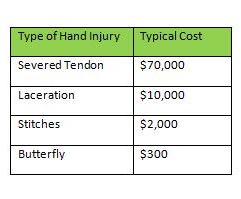
OSHA's Top Eight Hand Injuries to Protect Against
OSHA dictates that employers must use personal protective equipment (PPE) to provide additional protection against hazards that can’t be completely eliminated through other measures. According to OSHA, 70.9 percent of arm and hand injuries could have been prevented with PPE, specifically safety gloves.
The hand injuries that employers need to protect against include:
1. Burns
2. Bruises
3. Abrasions
4. Cuts
5. Punctures
6. Fractures
7. Amputations
8. Chemical exposures
Three Effective Ways to Prevent Hand Injuries
How can employers help prevent the eight hand injuries listed above? They can 1) evaluate job site risks, 2) teach employees about the hazards, and 3) provide the proper safety glove for the application.
1. Evaluate job site risks by asking the right questions:
- What engineering and work practice controls need to be in place to help prevent hand and finger injury?
- What tools and equipment will your workers use?
- Does the equipment have built-in safeguards to protect against pinching when exposed to moving machine parts? Are there barriers between your workers' hands and the saw blade?
- Are your workers wearing jewelry that can get caught in machinery? Thousands of employees are injured every year when a ring or bracelet gets caught in a moving machine part.
- Does the worker have to handle heavy equipment or machinery where fingers and hands are easily crushed?
You can always consult with a safety specialist, safety engineer, or product manager to help you evaluate the potential areas and risk factors that can lead to hand and finger injury at your job site.
2. Teach & train:
One of the best ways to behaviorally teach and train is to role play or simulate a hand injury. Tape up an employee’s dominant hand with gauze, then instruct him or her to perform a couple of simple work tasks and a personal task, such as texting. The simulation drives home how debilitating a hand injury can be and will help increase compliance.
Have a Glove Show & Tell: Display several different types of gloves and talk about the specific application for the glove. Reiterate the importance of using the right glove for the right task. (As was mentioned earlier, 30 percent of hand injuries are a result of using the wrong or inadequate glove for the job.)
3. Outfit workers with today’s high-performance gloves:
OSHA says, "It is essential that employees use gloves specifically designed for the hazards and tasks found in their workplace because gloves designed for one function may not protect against a different function even though the glove may appear to be an appropriate protective device." Below are three types of high-performance gloves, all of which have revolutionized hand protection.
Impact-resistant gloves
Impact-resistant gloves, also known as anti-impact gloves, feature dense thermal plastic rubber pads or overlays strategically located along the top of the hand and along fingers to help protect from crushing blows. TPR provides maximum cushioning while not interfering with dexterity. Other features of impact-resistant gloves include padded palms, molded knuckle areas, and extra grip patches. Workers in oil drilling, automotive, and heavy manufacturing environments benefit greatly from TPR technology.
Coated gloves
Numerous types of coated gloves are available today, which include nitrile foam coated, high-visibility knit coated, PU palm coated, crinkle latex coated, and the list goes on. Prominent features of coated gloves include seamless design, breathable knit back, elastic cuffs, and a variety of gauges. The main features of seamless knit coated gloves are their good grip and great dexterity. Solid coated fingers and palm usually provide abrasion and tear resistance. When wearing coated gloves, workers are also able to move their hands more freely and easily in cold conditions. Plus, coated gloves give additional skin protection from harmful chemicals and oils.
Coated gloves are ideal for jobs that require a high degree of touch sensitivity, dexterity, and a superior grip. Industrial applications include general assembly, painting, the handling of small oily parts and components, horticulture, machining, and maintenance.
Cut-resistant gloves
The use of cut-resistant gloves has increased considerably. Glove fabrics and coatings have been improving at a fast and furious pace; thus, cut-resistant gloves are thinner, more comfortable, and provide greater protection. Thanks to engineered composite yarns, manufacturers are creating gloves with superior levels of cut resistance without compromising comfort and dexterity—two major factors in worker compliance.
Engineered yarns, or super yarns, are popular in industrial applications requiring ASTM Level 3 or higher and are heavily used by meat processing, glass handling, and heavy sheet metal handling industries where workers are exposed to sharp blades. Those who work around sharp blades will need to wear cut-resistant gloves. The gauge and cut level required will depend on the specific task.
Get a Grip on the New ANSI/ISEA 105-2016 and EN 388 European Glove Standards
Just as today’s high-performance gloves have evolved and changed to take advantage of new technologies, the American National Standard for Hand Protection Classification and the European EN 388 standard have evolved to address these advances in PPE technology and cut-resistant materials.
On Jan. 12, 2016, the ISEA approved the new ANSI/ISEA 105-2016 standard for Hand Protection Classification. This standard is a voluntary consensus standard first published in 1999 and later revised in 2005 and 2011. A major focus of the new standard is cut-resistance testing and classification. The new ANSI/ISEA 105-2016 standard can be ordered at https://safetyequipment.org/standard/ansiisea-105-2016/.
The European Norm (EN) 388 standard is in the revision process and will be released in early 2016.
Below are three key points to help you navigate the new ANSI standard and the proposed EN 388 changes:
- Both the ANSI/ISEA 105 and revised EN 388 standard will now use the Tomodynamometer (TDM) 100 machine. As a result of this important change, the cut level between the two standards will now match in terms of range for most levels. Designating one piece of equipment for cut testing will help to eliminate confusion about glove performance and help safety managers choose the appropriate protection for their employees.
- ANSI will add four additional cut levels for higher cut-resistant materials using a nine-level alphabet scale rated from A1-A9. EN 388 levels through the TDM method will be given a six-step letter score of A through F. Previously, the ANSI and EN standards both had a ranking scale of 1 to 5, which caused confusion because different testing and classification methods were used. An "apples to apples" comparison did not exist between the ANSI testing and the European Norm (EN) testing.
- There are no third-party testing or conformity requirements for ANSI/ISEA 105. Testing can be performed and certified by the manufacturer.
Let's Do Something About That 70 Percent/30 Percent Hand Injury Statistic
Gloves today come in a variety of sizes, price points, materials, and styles to satisfy a wide range of industrial applications. Safety managers have thousands of glove resources and safety solutions at their fingertips to ensure they are protecting the fingers and hands of employees. Ask yourself, "What can I do today to protect my employees' fingers and hands tomorrow?"
Tackle the fact that 70 percent of workers aren't wearing gloves by making sure safety gloves are readily available for the employee. Establish work rules that demand when and where gloves are to be worn. Reward compliance and make sure employees know the repercussions if they don’t comply with safety rules.
Put a dent in the fact that 30 percent of workers are not wearing the right glove by choosing the proper glove for the application, whether that is an impact-resistant glove, a coated glove, or a cut-resistant glove of the proper gauge. Also, don’t be misled by leather gloves for cut protection. Because leather is skin, it can be easily cut, just like the skin of your employee. Leather, although a popular choice during my grandfather's time and my father's time, is not a good choice today for employees whose jobs expose them to the risks of cuts and lacerations.
I hope in the next year, the number of hand and finger injuries drops significantly as compliance and proper glove specification improve through technology, innovation, training, and motivation. Let's all work together to reduce the number of hand injuries. If in favor, raise your hand!
This article originally appeared in the April 2016 issue of Occupational Health & Safety.