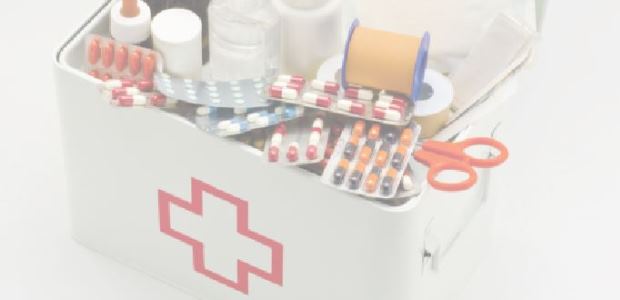
Page 2 of 2
How ANSI is Leading the Way to Better First Aid in the Workplace
First aid supplies are found in nearly any setting—from residential, industrial, and recreational sites to vehicle fleets. Yet as common as they are, first aid kits in the workplace have not historically been required to align with the number of employees they serve or the types of hazards present. The U.S. Occupational Safety and Health Administration requires that first aid kits be accessible for use at work sites with more than five employees. However, in the matter of kit specifications and minimum content requirements OSHA refers to the American National Standards Institute (ANSI). Until recently, though, neither organization called for the appropriate types and amount of first aid components sufficient to meet the unique needs of individual workplaces.
Despite the widespread use of workplace safety controls and personal protective equipment, accidents still happen. In fact, more than 3.5 million nonfatal occupational injuries were recorded in 2013, according to the U.S. Bureau of Labor Statistics. When employers lack sufficient first aid supplies, they expose workers to increased risk of infection and other negative outcomes, including additional medical fees and lost wages, while exposing themselves to myriad direct and indirect expenses that range from medical and legal costs to workers’ compensation and lost productivity.
First aid is critical in treating injuries as soon as they occur to promote a positive outcome. Recognizing the inherent danger and liability in undersupplied first aid kits, the International Safety Equipment Association recently recommended fundamental changes to the ANSI/ISEA standard Z308.1, "Minimum Requirements for Workplace First Aid Kits and Supplies," and these changes represent a holistic shift in our nation’s approach to occupational injury preparedness designed to better protect workers and employers alike in the event of a workplace injury.
When the standard came up for review in 2015, a new ISEA committee was assembled to review the existing standard with an eye toward possible improvements. When it assessed recent data showing a rising number of injuries for which first aid was applicable, the committee recognized an opportunity to make important changes to the way America’s workplaces approach injuries. Among their findings was that the prior standard left room for employers to meet the minimum requirement, yet be woefully undersupplied in the event of an injury. The committee carefully considered the standard’s mission—to protect employees through injury readiness—and brainstormed new ways to help make the standard better support its mission.
What the New Standard Entails
The revised 2015 standard represents a fundamental shift in the way employers will approach injury readiness. It starts with a foundation built upon supplying the right assortment of first aid items based on possible injuries and the appropriate quantity of items based on the number of workers each kit will serve.
One pillar of this foundation is the introduction of two distinct classes of first aid kits. Class A kits contain an expanded list of contents designed to offer greater access to the items needed to treat most common types of workplace injuries, such as minor cuts, abrasions and sprains, while Class B kits feature a broader range and quantity of supplies to treat injuries in more complex or high-risk environments. Many of the supplies that had previously been identified as recommendations are now required for both newly designed kits.
Ideally suited for workplaces with 40 or fewer employees and relatively low-risk operations, Class A kits include a total of 71 required items, ranging from adhesive bandages, tape, and scissors to a breathing barrier, burn treatments, eyewash, and hand sanitizer. Class B kits include an increased quantity of most Class A items, as well as additional products, such as a padded splint and tourniquet, designed to triage serious or life-threatening injuries. Often compiled in cabinets, Class B kits offer a more comprehensive selection of emergency supplies that are suitable in heavy manufacturing, foundries, and other high-hazard environments.
Hazard Assessment
The other pillar supporting the new standard is the requirement for employers to assess the hazards present and ensure that additional types and quantities of supplies are made available based on each site’s individual needs. Risk assessments can be conducted in a variety of ways, from reviewing BLS and OSHA injury data to employing a medical professional to evaluate a facility and make recommendations; the best approach is an informed approach and may involve a combination of inputs. This mandated assessment of possible injuries and appropriate first response protocols is key to tailoring first aid kits based on each workplace’s unique risk factors.
Remember, the kit meets ANSI Z308.1-2015 only when the required minimum fill is maintained with first aid products marked "ANSI/ISEA Z308." To ensure compliance, employers should appoint a safety manager or similar individual with oversight of first aid kits.
From tracking item availability and expiration dates to conducting monthly inspections and restocking supplies, maintaining kits across facilities can become a sizable task. A popular solution is to outsource such operations to a vendor-managed inventory service. The slight increase in costs will pay off in guaranteed compliance and preparedness, which can lead to sizable savings in injury outcomes and their associated costs.
Administering the appropriate type of first aid as quickly as possible can make a significant improvement in injury outcome. By complying with the new ANSI standard, employers can support positive outcomes by being prepared for the types of injuries unique to their site and applications. The result is a healthier, safer, and more productive workforce—the very foundation that makes every company great.
This article originally appeared in the April 2016 issue of Occupational Health & Safety.
About the Author
Erica Osley is the marketing director for eye, face and head products with Honeywell Industrial Safety.