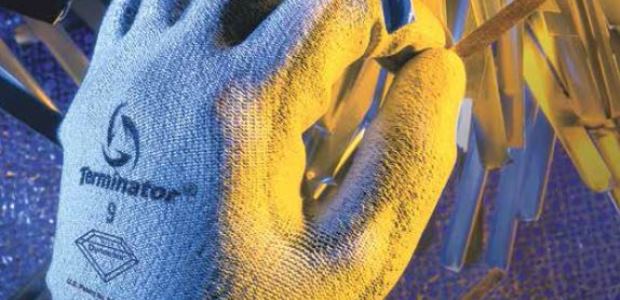
Get the Cut Resistance Your Workers Require
Why do you need to know what is in your cut-resistant glove and how it works?
- By Griff Hughes
- Nov 01, 2014
Recently, I visited a plant that was stamping large pieces of metal. Each had a sharp edge with lots of burrs. Judging by the severity of the edge, we started application testing with ANSI level 4 gloves. All cut very quickly as we moved them along the edge with pressure.
When we tried ANSI level 2 gloves, they did not cut. Why?
First, we have to look at the ANSI standard as compared to real-world edges. Then we can draw a logical conclusion.
Both test methods recognized by ANSI (ASTM F1790-97 and ASTM F1790-05) utilize a metal knife blade. Gloves with components such as glass or stainless steel that act as dulling agents perform well in these tests by curling the blade edge before it can cut through the fabric of the glove–thus providing blade cut resistance.
Several years ago, I watched a customer take a knife blade and stroke it several times across the palm of a cut-resistant glove that contained glass. Under magnification, we could clearly see that the blade edge had actually been curled. This is how dulling agents such as glass and stainless steel protect against knife blades and perform very well on both the ANSI tests, as well as EN388, which uses a circular rotating blade.
If your hazard is a knife blade, these tests will give you an indication of the level of protection that they will provide. There is a known variance for test results preformed by different labs, so you can also perform a practical test as previously mentioned to get a more accurate reading of the protection provided. Just remember to change your knife blades with each pass across the glove.
Many applications involve handling machined or stamped metal or sheet glass. These applications are different. Knife blades cut. Sheet metal tears and glass is harder than metal, so how can a metal knife blade test relate to these hazards?
Sheet metal and machined metal have burrs along their edge, which cannot be dulled. In these applications, tensile strength is needed. The strength of the filament is so strong that the metal burr cannot tear through it. Glass is harder than metal, so metal knife blade test results should not be considered as an accurate indication of cut protection in glass applications.
Given the lack of correlation between the ANSI and EN388 test methods and sheet metal and glass applications, how can we evaluate proper protection? In these situations, the best way is to expose the glove only to the edge in what can be termed an application test.
Factors to consider in performing an application test and evaluating its results are:
- Edge sharpness.
- Length of the edge–longer edges require stronger gloves.
- Thickness of the metal–thicker metal has bigger burrs.
- Weight of the object–more weight can increase the force of the cut.
- Surface texture–oily and wet surfaces require gloves that can grip.
- Keeping an edge from moving is as important as the cut resistance itself.
- Type of edge–razor sharp or abrasive sharp (having burrs).
- Composition of the material – steel, glass, stainless steel.
- Most importantly, the frequency with which the edge is going to be handled.
For sheet metal and glass, stretch the glove across the edge and run it along a length comparable to that by which the hand may be exposed and with enough pressure to reflect the weight of the object. This should be done repeatedly until the glove has either been cut or shown to hold up sufficiently.
No glove is cut proof. It is up to the safety professional to determine the exposure, the potential length of the edge, the weight of the object, and the frequency with which it is being handled. Remember that the higher the frequency of contact, the greater the exposure to wear. As gloves wear, their cut resistance is reduced.
Drawbacks of Stainless Steel and Glass Composites
In general, our industry uses stainless steel and glass composites as dulling actions and continuous filaments for tensile strength. Each has its drawbacks. Most continuous filaments lack any dulling action, and they come in different levels of tensile strength, which can create a wide variance of protection in sheet metal and glass applications. Stainless steel composite yarns can make the user potentially conductive, so it is important that you know where the gloves may be used.
Glass may become friable. If inhaled, glass fibers of a certain thickness are known to be carcinogenic, so it is important to know their content and whether the application can cause them to become friable. Also, look at the surface of the knit. Many times, the glass will break during the knitting of the glove and appear on the surface as shiny white fibers. This is an indication that the glass was not properly encapsulated.
Additionally, the surfaces should be evaluated for the type of lubricant being used or if it is a dry surface. If they contain lubricants, then the type needs to be identified. This will help to determine the proper coating of the glove. Nitrile works best in hydrocarbon-based lubricants but can become slippery in water-based solutions. Latex (natural rubber) provides excellent abrasion and puncture resistance on dry surfaces. PVC cuts very easily, so it is less likely to be used in cut hazard applications. Every manufacturer has its own secret formula for coatings, so each should be treated as unique.
Ensuring Employee Acceptance
At this point, it is necessary to understand the stakeholders: the actual customer who is the user, the safety professional who needs to protect them, and purchasing, who is there to protect the company’s assets. Each has priorities, and a successful glove selection must satisfy all needs.
After application testing, a pre-selection of approved items can be made. These should then be evaluated for sizing, comfort, fit, dexterity, and cost. This section of the glove selection now involves employee acceptance. If the user will not wear a product due to improper fit or discomfort, then any level of protection and cost effectiveness will be rendered useless.
In order to ensure acceptance, features to look for are a broad size range. If the gloves selected cannot fit your entire population, then you will be unable to standardize your hand protection program. The hand form that the gloves are dipped on should be ergonomic in design to allow for proper hand function. If grip and ease of hand flexion are compromised, then you will be contending with ergonomic problems later on. If the gloves lack the necessary fingertip touch and dexterity, then productivity will be compromised, especially in highly repetitive operations. If the grip fails to give positive contact, then the edge will move, reducing the very cut resistance that you are trying to provide.
Lastly, gloves should not be so stretchy that users can downsize, as this will reduce the surface area of the fabric and thus reduce its cut resistance. Gloves that stretch too much cannot hold objects safely because the fingers and palms will stretch with the weight of the object. There is a delicate balance between stretch and flexibility for hand dexterity. Having too much stretch reduces hand safety.
Now comes the hard part. Having spent all of this time to select approved items by individual glove brand, another supplier will arrive claiming that his product is identical and lower priced. Despite the urge to switch, one must realize the time that was spent to get the correct product. Any masquerading equals should go through the same evaluation process so that they can be considered legitimate contenders.
This article originally appeared in the November 2014 issue of Occupational Health & Safety.