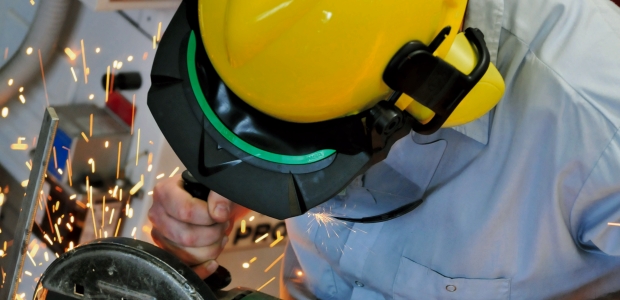
Understanding Head Protection
The bottom line is that hard hats must be properly utilized and maintained to ensure safety.
- By Trish Luedtke, Mackenzie Peters, Sue Pingree
- Sep 01, 2014
Worker safety is always the highest priority on the job site, and head protection is an essential element in providing workers with protection from falling debris, low-hanging objects, and electrical hazards. A hard hat should be worn in all situations where there are head protection hazards.
As a rule of thumb, hard hats should:
- Resist penetration and deflect blows to the head
- Have a suspension system that can absorb the force of impact
- Serve as an insulator against electrical shocks (when warranted)
- Be water resistant and slow burning
- Shield the scalp, face, neck, and shoulders.
Standards
Standards are the backbone of safety. Determined by consensus, they are the rules and guidelines that help to govern the use of safe practices and proper protective equipment in an effort to provide a work environment free from known dangers or hazards.
Standards must be re-evaluated periodically to account for improvements in technology, test methods, materials, worker needs, and current trends in use and application of products. As such, on June 3, 2014, the American National Standards Institute (ANSI) issued approval for ANSI/ISEA Z89.1-2014, American National Standard for Industrial Head Protection.
This standard was prepared by members of ISEA's Head Protection Group as a revision to the 2009 edition and approved by a consensus review panel of technical experts, unions, construction industry and other user groups, test labs, certification agencies, and government agencies.
ANSI/ISEA Z89.1-2014, American National Standard for Industrial Head Protection
The ANSI/ISEA Z89.1-2014 standard (the "Standard") provides performance and testing requirements for industrial hard hats. Taking into account the type of hazard a worker may face, the Standard establishes the types and classes of protective helmets to provide employers with hard hat options that provide appropriate protection fort the hazards present in their specific workplaces.
The Standard addresses the following:
- Specifications for helmets by Type (based on location of impact force) and Class (based on electrical insulation);
- Impact in occupational settings under normal temperature conditions and, optionally, at high and low temperatures;
- Safety recommendations for hard hats worn in the reversed position;
- Requirements for high-visibility helmets;
- Test methods for evaluating all requirements; and
- User cautions and recommendations regarding helmet care.
Types of Hard Hats
Each type of hard hat is designed to protect against specific hazards, so it is important to first consider those hazards and any use limitations to determine your proper protection.
The Standard categorizes hard hats by impact type. A Type I (top impact) hard hat is designed to reduce the force of impact on top of the head. The Type II (top and lateral impact) hard hat not only reduces the force of an object that may directly impact the top of the head, but also the force from a side blow to other parts of the head.
ANSI has divided hard hats into three general classifications: Class G (General) is an all-purpose, general helmet that provides good impact and penetration protection, but it offers limited voltage protection (up to 2,200 volts); Class E (Electrical) provides the highest level of protection from high-voltage shock (up to 20,000 volts) and is especially well suited for electrical work; and Class C (Conductive) does not protect against electric conductors.
Markings
Helmets that comply with the Standard's requirements must be marked with proper certification. Inside the helmet, you’ll find the applicable standards requirements met (including those that are optional) and the class designation. Hard hats must include the date of manufacture and the manufacturer’s name and must be accompanied by the manufacturer's guidelines for care and service.
Inspection, Care and Maintenance
The hard hat consists of a shell, a suspension system, and, when applicable, a chin strap. Each component requires frequent inspection and maintenance to ensure its continued ability to protect the worker. Understanding the importance of this information and applying it to safety protocols can help prevent serious injuries and save lives.
Follow these helpful tips for inspection, care, and use:
- Never store a hard hat in direct sunlight.
- Clean the hard hat shell and suspension system with mild soap; rinse with warm water.
- Inspect the shell for any sign of damage or excess wear, perforations, cracking, or deformity of the shell.
- Inspect suspension straps for cuts, frays, damage from chemicals, or any other sign of wear.
- Never drill holes in the shell of a hard hat unless instructed to do so by a manufacturer. This can lessen the impact resistance of the helmet and nullify the Class E or G electrical insulation rating.
- Do not use adhesives, paints, or cleaning solvents on your hard hat unless approved by the manufacturer. They may damage the shell and lessen the effectiveness of the protection and prevent proper inspection.
- Never place any object under the shell and/or between the suspension and the shell. This will reduce the ability of the entire assembly to properly protect from an impact.
Why is There a New Standard?
Voluntary industry consensus standards recognized by ANSI are required to be reviewed every five years; the last edition was ANSI/ISEA Z89.1-2009. This five-year span allows the committee to continuously reexamine the market and update the standard, if necessary, to ensure any worker who faces hazards where hard hats are required is as safe as possible.
What Has Been Updated in ANSI/ISEA Z89.1-2014?
As work environments change and new hazards emerge, ANSI/ISEA Z89.1-2014 attempts to eliminate any ambiguity regarding characteristics of industrial head protection and their importance in the work environment. Core performance requirements stated above remain unchanged. However, there are three important updates in ANSI/ISEA Z89.1-2014:
Section 5: Accessories and Replacement Components
While already a requirement of Z87 for face protection, the 2009 version of the Standard indicated that accessories or components installed onto hard hats cannot cause the helmet to fail. The 2014 Standard update provides additional language that further supports the fact that the accessory/component manufacturer is responsible for proving its products do not cause the helmet to fail:
"The entity claiming that an accessory or replacement component, when installed, will not cause the helmet to fail the requirements of this Standard, and is responsible for providing justification upon request."
Section 6: Instructions and Markings
Clarification language was added to this section to help customers understand that "useful service life" for helmets is not required by the Standard, though helmet manufacturers may choose to include it.
"NOTE: Useful service life guidelines are intended to provide the user with information that certain conditions may affect a specific helmet’s continued protection over time. A specific service life, defined in terms of number of years, is not required though individual manufacturers may choose to include such information for their respective helmets."
Section 7.3.3 Higher Temperatures
The revision enables additional protection in response to users who may work in hot environments. The 2009 Standard temperature conditioning was 48.8°C ± 2°C (120°F ± 3.6°F). An optional preconditioning at higher temperatures of 60°C ± 2°C (140°F ± 3.6°F) has been added to the 2014 version. If a helmet has been pre-conditioned to 60°C ± 2°C (140°F ± 3.6°F), it will be marked with "HT." In addition, the new updates allow for flexibility and inclusion of emerging and state-of-the-art manufacturing materials for higher temperature protection.
One caveat to note: The Standard does not address pre-conditioning that could be needed for extremes of temperature and radiant heat. To ensure you have the proper heads protection level needed for your specific heat application, check with the manufacturer for stated usage of any helmet.
What Does the New Standard Mean?
ANSI/ISEA Z89.1-2014 does not require users to discontinue utilizing products labeled as compliant with the 2009 version of the standard. However, if your occupation requires you to be compliant with the new optional certifications, such as pre-conditioning at higher temperature, older products will not be marked and may not be compliant. When in doubt, it is always best to check with OSHA for specific requirements.
Will There Ever Be a Global Standard?
Many often question why a global standard can't be established, eliminating the need for multiple regional standards. To answer, it is important to note that standards committees understand the varying challenges and issues facing each geographic region and regularly follow each other; however, since standards are frequently based on government regulations and requirements, it would prove too difficult to put forth an all-encompassing global standard for head protection at this time.
Conclusion
To safeguard workers and employers by providing proper safety protocol for work site hazards and PPE, we rely on standards. By design, they are meant to help in eliminating workplace fatalities and injuries. In continuing to ensure workers are kept safe, standards, such as ANSI/ISEA Z89.1-2014 are re-evaluated to account for any changes in use and application of products.
The bottom line is that hard hats must be properly utilized and maintained to ensure safety. And thanks to the standards designed to govern industrial head protection, you can wear your hard hat in good faith.
A copy of ANSI/ISEA Z89.1-2014 can be purchased from International Safety Equipment Association. Visit www.safetyequipment.org for details.
This article originally appeared in the September 2014 issue of Occupational Health & Safety.