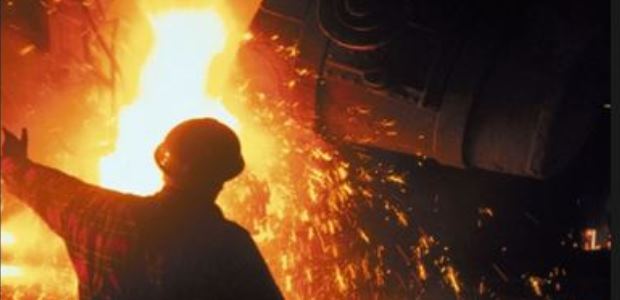
Page 2 of 4
If You Can't Stand the Heat
It's August, the hottest time of the year for much of the United States. In many work environments, the challenges of heat exposure and heat exhaustion only intensify during these summer months, often resulting in unbearable working conditions. Workers are faced with a choice: to comply with safety policies and wear their required layers of protective apparel or to remove a layer (or two) to help them be more comfortable. This is not a difficult decision for an alarming number of people.
The reality at work sites across the United States is that many workers may not be wearing personal protective equipment (PPE) as mandated. An online survey conducted by Kimberly-Clark Professional in August 20121 found that an astounding 82 percent of safety professionals polled had observed workers failing to wear PPE during the past year.
Non-compliance with PPE standards is consistently listed as a top concern for safety professionals, as shown in the Kimberly-Clark workplace safety research since 2006. In fact, 2012 marked the sixth year that the study revealed a PPE non-compliance rate of at least 80 percent.
In every work environment, the importance of complying with PPE standards is repeated on safety calls, in safety meetings, and in safety training. Many workers have seen their co-workers get injured or worse, yet they continue to put themselves at risk for serious injury or even death by not following important safety procedures. Why is this?
Complying With PPE Protocols Can Be a Double-Edged Sword
Some workers believe that donning protective apparel as mandated by their employer (or to meet a safety standard requirement) impedes their ability to do their job and may put them at greater risk in completing their work assignments. Their activity load, combined with their required uniform, may make them too hot and sweaty and thus at significant risk to succumb to heat stress. Work clothing may restrict their movement to the point that they are unable to perform their job correctly, increasing their likelihood of being injured or jeopardizing their employment should they make a disastrous mistake. These men and women think that if they alter or remove the restricting clothing article, they will be able to perform their job to the best of their ability, which in turn lessens their "need" for PPE.
The prevalence of this mentality that workers don't need PPE is substantiated in the 2012 Kimberly-Clark survey; more than half of the safety professionals surveyed attributed non-compliance to workers thinking that safety equipment was not needed.
More and more workplaces require personnel to perform multiple tasks across different hazard zones in their facilities. Diverse hazardous environments require different, and often flexible, protective solutions. PPE required in one department may not be necessary in another in which the need for protection is not as severe.
Simply because the danger isn't immediately evident doesn't mean the proper use of protective apparel is less important. Workers sometimes do not recognize or understand that, even when they may not be in impending danger of being hurt, some PPE protocols are designed to prevent problems linked to long-term exposure.
Comfort Equals Compliance
OSHA guidelines for selecting PPE state: "Employers should take the fit and comfort of PPE into consideration when selecting appropriate items for their workplace. PPE that fits well and is comfortable to wear will encourage employee use of PPE."2
Yet comfort remains another common instigator of PPE non-compliance, according to the Kimberly-Clark survey. In fact, most of the top reasons cited in the survey for non-compliance were comfort-related, including that protective apparel is too hot, fits poorly, or looks unattractive.
Improving comfort to increase PPE compliance is of the utmost importance. It is common for PPE decision-makers to settle on protective apparel that has a "lack of discomfort" but just meets the minimum level of protection required for their workplace. Measuring comfort can be very subjective. The protective properties of a fabric can be precisely measured through standardized testing, but what may be comfortable to one person may seem uncomfortable to another. There are testing standards that are designed to estimate comfort (such as the Kawabata Evaluation System, or KES), and other standards are designed to evaluate thermal comfort. Combining the data from these tests helps to assess the overall comfort of a given fabric or garment.
The thermo-physiological comfort of a garment is simply measured by a fabric's permeability to air, heat, and water. Increased air flow results in increased breathability, leading to better moisture management, and the air flow, in turn, allows heat to dissipate more efficiently.
The amount of air that passes through a garment, or air permeability, can be measured using test methods described in ASTM D 737-043 and ASTM F 1868-14.4 Measuring heat permeability is also listed in ASTM F 1868-14 and is defined as "Total Heat Loss," or THL.5 THL is the amount of conductive (dry) and evaporative (wet) heat loss that occurs through a fabric or multiple fabric layers in an ensemble. Water permeability, or moisture management, can be assessed through several methods, including tests for moisture wicking (both vertical and horizontal wicking),6 drying time (there are a variety of test methods used to determine drying time),7 and evaporation percentage.8
Finally, size and cut are extremely important for a garment to fit comfortably. While it may be a simple concept, it is often difficult to ensure that protective apparel fits properly in a workplace needing a wide range of sizing options to fit both men's and women's body types and to defend against a variety of exposure hazards. A loose-fitting garment may provide additional thermal insulation and greater mobility, while a tighter fit will reduce the risk of that clothing’s being caught in machinery. Finding the appropriate balance in the fit of a garment is vital.
Despite their best intentions, safety managers are sometimes forced to select protective apparel for their work environment based on which options provide the highest level of protection without exceeding budget constraints—an especially important decision driver. While comfort or "wearability" is often not the primary deciding factor, it is important to invest in protective apparel that workers will want to wear.
Enhancing Comfort Without Compromising Safety
Until recently, safety managers' choices for comfortable protective apparel have been limited. To put it simply, mass matters, and the more mass that can be placed between the wearer and the hazard (be it molten metal, arc flash, flame, or even cut protection), the better. Comfort-driven protective apparel (i.e., lightweight material) has not historically offered enough protection to be seriously considered for use in extremely hazardous environments.
But PPE fabric and clothing manufacturers have risen to the task of developing lighter-weight solutions that combine a high level of protection with maximum comfort. NFPA 70E Hazard Risk Category 2-rated garments continue to get lighter and lighter, and more flexible and lightweight options for extreme environments are now available. PPE apparel manufacturers have also created lighter-weight, flexible alternatives for clothing that is commonly perceived as being heavy and rigid, such as aluminized apparel.
Layering is an optimal and flexible solution to increase protection Lightweight protective apparel allows workers to wear multiple layers when undertaking hazardous tasks. while maintaining comfort. With a layered clothing system, two plus two often equals five when it comes to thermal protection. Air trapped between two lightweight layers provides additional insulation, and two lighter-weight or lower-rated garments can often provide the same or even better protection when worn together than a single, heavier primary protection layer. Also, with a layered approach, employees can wear heavier, higher-rated outer gear in extreme-risk situations and then remove this clothing when the threat of injury is not as great and still be protected by a lighter-weight protective base layer.
It may seem obvious: If protective apparel is comfortable, more workers are going to wear it. Increased compliance with PPE standards results in fewer injuries. Fewer injuries mean safer workers, a reduced number of workers' compensation claims, and greater cost savings for employers.
To achieve these results is going to require the support and engagement of safety managers year round—not just when the mercury rises.
References
1. Survey conducted with 110 people over the Internet in August 2012. All survey respondents were responsible for purchasing or influencing the purchase or selection of PPE.
2. Occupational Safety and Health Administration (OSHA), Personal Protective Equipment, OSHA 3151-12R 2003.
3. ASTM D 737-04: Standard Test Method for Air Permeability of Textile Fabrics.
4,5. ASTM F 1868-14: Standard Test Method for Thermal and Evaporative Resistance of Clothing Materials Using a Sweating Hot Plate.
6. AATCC Test Method 197-2013: Vertical Wicking of Textiles. This test method is used to evaluate the ability of vertically aligned fabric specimens to transport liquid along and/or through them. AATCC Test Method 198-2013: Horizontal Wicking of Textiles. This test method is used to evaluate the ability of horizontally aligned fabric specimens to transport liquid along and/or through them.
7. AATCC Test Method 199-2011: Drying Time of Textiles. Moisture Analyzer Method: This test method is intended to evaluate the drying time of knit, woven, or nonwoven fabrics at an elevated temperature using a gravimetric moisture analyzer. By performing the test at non-standard textile conditions, it is possible to simulate drying at body temperature or to perform testing at temperatures that simulate conditions of use.
8. Evaporation percentage and drying time can be determined using the Gravimetric Absorbency Testing System (GATS).
This article originally appeared in the August 2014 issue of Occupational Health & Safety.