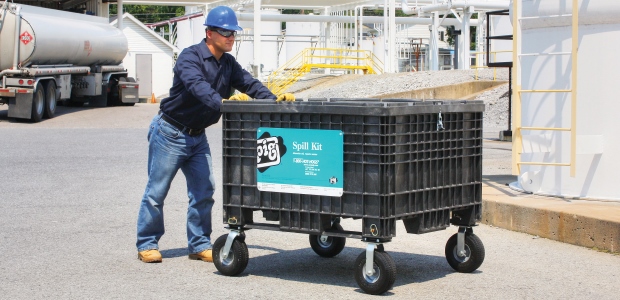
Get Everyone on the Same Page
Every employee needs to be able to answer these six questions in an emergency.
- By Karen D. Hamel
- May 01, 2014
Performing the same action repetitively promotes muscle memory. Musicians and athletes often use the technique to help perfect certain skill sets. Facilities can use a similar training strategy to make sure that everyone knows exactly what to do when there is an emergency.
Even though it typically interrupts everything, increases the production manager's blood pressure, and makes employees roll their eyes every time there is a drill, going through emergency response exercises regularly helps everyone to know instinctively what to do. An employee who inherently knows what steps need to be taken when an alarm goes off or when something unanticipated happens is less likely to panic, freeze, or do something unexpected.
Whether the facility calls them emergencies, accidents, disasters, or incidents, they all share a commonality: According to most preparedness experts, although they are unplanned, emergencies are predictable. Facilities located in coastal areas can expect flooding and hurricanes. Facilities with machines can expect them to break down. Because emergencies are predictable, plans can be put in place and properly communicated through training so that everyone is prepared and knows exactly what actions to take when they do occur.
Preparing employees involves more than pointing to the nearest illuminated exit sign and hoping they'll remember that when an alarm goes off in five or six years. Employees who experience drills regularly and can answer these six questions will be better prepared to handle emergencies and to take the correct actions.
1. What is an emergency?
Less than a generation ago, the definition of an emergency could be segmented, depending largely upon a person's isolated perspective. For example, to an office worker, it may be someone having a heart attack. To the plant manager, it may be an entire line unexpectedly shutting down. To a spill responder, it may be a spill threatening to leave the boundaries of the facility. Acts of terrorism and natural disasters were rarely even considered.
Now, planning for emergencies needs to encompass many different scenarios: from first aid to rescue operations; from chemical spills to fires and explosions; from natural disasters to active shooters and other forms of terrorism. Recognizing that emergencies can take many different forms and identifying the scenarios that may affect the facility are vital steps in emergency planning and education.
Each facility will have a unique set of emergencies. Recognizing what constitutes an emergency allows steps to be taken to mitigate and plan for those emergencies. They are also in a better position to help employees understand how those emergencies may affect them and what actions they need to take when something unexpected does occur.
2. What is an emergency action plan?
Emergency action plans are required by a number of different OSHA regulations. Well-prepared plans outline the facility's procedures for reporting emergencies, document emergency evacuation and exit routes, and list methods for accounting for everyone after an evacuation. They also document procedures for employees who will remain to operate critical plant processes before evacuating and for anyone who will perform rescue or medical duties in an emergency.
Simply knowing that there is a plan is an important first step. Employees should know where to access copies of the plan and understand how it helps to keep them safe when there is an emergency.
3. Who is in charge?
Roles and responsibilities can be different during emergencies. While a president or vice president may customarily make decisions concerning purchases, operations, or other functions, this individual may not be the primary person in charge when there is an emergency.
Even for employees whose only role in an emergency is to pull an alarm or evacuate, knowing where to go and whom to report to after they evacuate is vital so that evacuation coordinators know not to send someone into the building to look for them. Employees who will take response actions need to know where to report and who is in charge of response planning and operations. Establishing clear lines of authority and communicating those lines of authority helps to avoid chaos and keep responsibilities within everyone's span of control.
4. What exactly do I need to do when there is an emergency?
No matter what the scenario is, well-trained employees who are comfortable performing their expected duties should be able to handle emergencies instinctively. Whether they are evacuating when they hear an alarm, providing first aid, cleaning up a chemical spill, or sheltering in place, the actions that need to be taken should be second nature.
Each employee should, at a minimum, know at least two ways to get out of the building, where to go once they exit the building, and whom to report to. Employees with critical roles or tasks should be able to perform them as if they occur every day.
Evaluate every drill and encourage feedback. Observe employees who have response roles. Can they perform the roles comfortably? What worked well? What didn't? Working through issues before there is an actual emergency is far better than having someone not be able to perform necessary duties in a crisis situation.
5. Who can talk to the media?
During an emergency, the media can be a blessing or a curse. It sometimes seems as if journalists have a knack for finding the least-knowledgeable person to quote or feature in their news segments. Having a media plan that includes the names of facility personnel who will speak with media representatives as well as policies for posting information on social media can help avoid information leaks and the potential for misinterpreted or conflicting messages reaching the public.
Media plans should establish policies that direct which individuals are permitted to speak to the media or post information to social media on behalf of the facility. Also, they should document a means of handling media requests for quotes or other information. Because even "no comment" can be misinterpreted, teaching employees to say "Please contact (name) for more information" or something similar will help to channel requests to personnel who have been trained to work with the media and are in a position to provide accurate information.
6. How is my facility going to recover from this?
This may not be a question after every emergency, but it will likely be a question after a widespread natural disaster, a significant fire, or a large chemical release. At the most basic level, employees simply want to know if they will have a job tomorrow.
Facilities with business continuity plans will be able to answer that question because procedures already have been established to rebuild, reestablish, and regrow the facility with the least amount of interruption and in the shortest amount of time. Robust plans even will establish roles and responsibilities for groups of employees and account for employees who may need to take time to repair or rebuild their own homes or attend to other family matters before returning to work.
An Eye Toward the Future
It can be hard to shift from the "Ugh--not another drill" mindset. Drills are disruptive, and it's easy for them to become routine with everyone simply following the masses of people headed out the nearest door. But until everyone is as comfortable performing their expected duties as they are signing their name, improvements or changes to the plan may still be needed to help with comprehension and comfort levels.
Involving employees in planning efforts can help teach them why drills are important and encourage understanding. It also can help them become leaders, encourage safe behavior during an emergency, and remind others of their roles until everyone is on the same page.
This article originally appeared in the May 2014 issue of Occupational Health & Safety.