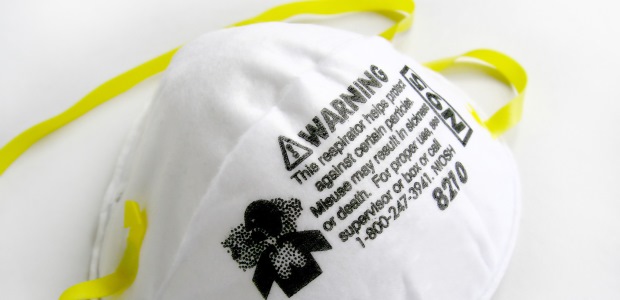
Dust Mask or N95?
OSHA's respiratory regulations require that you have a written program outlining your company's usage of respirators. The program needs to be reviewed annually.
"I need a mask," said Jim Oswald, the newest employee at the Hightower Chemical Company.
"They're in the cabinet with the other PPE," replied Oscar Cohen, supervisor of the organic mixing section.
"The what cabinet?"
"PPE. You know, the protective equipment," said Oscar.
"Oh, you mean the green cabinet?"
"Yes."
Jim went over, opened the green cabinet, and saw boxes and bags of masks, gloves, mops, brooms, and other tools. He grabbed a bag of paper masks and took them back to his work station. Tearing open the bag, he took one and put it on, throwing the open bag back onto his bench. He then began to pour 12 liters of acetone into the reaction flask, according to the formulation sheet. As soon as he began pouring, he found himself short of breath.
Oscar saw what was happening and pulled him away from the area.
"What were you thinking, Jim? That dust mask is not the correct PPE for you to use with organic solvents," Oscar said.
"What do you mean? I thought I could use it for everything," Jim replied. "It says on the bag that they are all-purpose dust masks."
In an embarrassed tone, Oscar said to him, "Jim, I don't think that we ever got you trained in PPE. Come with me to the safety office, and we'll see if Barry can give you some training."
Knocking on the door, they found Barry reading the current edition of Occupational Health & Safety magazine on his computer. "Come on in, fellows," he greeted them. "What can I do for you?"
Oscar explained what had happened and said he thought Jim hadn't received any training in PPE usage, especially respirators. Barry clicked a few buttons on his computer and pulled up the training database. "No, it doesn't look like you got properly on-boarded with your training. Let's take care of that now," he said. "First, what is Jim's job classification?"
Oscar said, "He is blender-man/mixer. He'll be working in my department weighing up formulations. He will need full- and half-face respirators, safety glasses, goggles, faceshield, and both regular and coated coveralls. And we want to get him on the Hazmat Team. He will need twenty-four hours of Hazwoper training."
"Jim, the first thing that we're going to do is send you out for a physical examination," Barry said. "I'm going to give you some time to fill out this questionnaire. It is known as Appendix C from the OSHA Respiratory Protection Standard, 1910.134. Once you've completed it, take it with you to the clinic. The doctor will review it. She will answer any questions you have about it and give you a physical examination. While you're there, we'll also give you the Hazmat Team physical. That will give us a baseline so we'll know what your levels are. If you were to get exposed to a chemical, we would have something for comparison.
"Do you have any questions of me, before you go?"
Training Fundamentals
When Jim returned, he has an approval letter from the clinic doctor indicating that he was fit for both respirator usage and for the Hazmat Team.
Barry began Jim's training by telling him, "You know who OSHA is, don't you?" And Jim nodded yes.
"Our company has to comply with all of the OSHA regulations, and we especially want to keep our employees safe while they are working. As you know, we work with some chemicals that are considered hazardous, and if we don't work with them properly, then you or other employees could become sick.
"We work to ensure your safety by following the 'hierarchy of controls.'
"The hierarchy starts with:
- substitution or elimination of a hazard
- engineering controls
- administrative or work practices and, finally
- personal protective equipment, or PPE.
"If we are able to substitute a less hazardous material for the more hazardous material, then we wouldn't need as much protection for our employees. For example, say we were using mineral spirits for cleaning. It is a solvent and tends to dry out skin when it comes in contact. Could we use soap and water to do the cleaning? That might be possible in some instances. Or what if the parts came in clean--we wouldn't have to do anything. We've protected you because there is no hazard.
"Next is engineering controls. This includes equipment that works to protect employees by sucking fumes, vapors, or dusts away from your breathing zone. Another engineering control would be to enclose the process if it were noisy or to make a work space enclosure for you if we couldn't enclose the machine.
"Our third step in the hierarchy is administrative or work practices. This would be such things as signs reminding you to wear your eye protection, or maybe we would spit the shift between two employees. That would give them job enrichment and rotation. It would also cut their exposure to noise or hazardous materials, for example, by half.
"Last step in the hierarchy is PPE," Barry continued. "Why do you think that it is the last step?"
Jim thought for a moment and said, "Is it because the worker has choices?"
"Exactly right," Barry answered. "The employees have to know and understand all of the details about the PPE they are going to need and the hazards of the chemicals to ensure they are using the correct PPE and that it will provide them with the protection against the hazards in their workplace. In addition, some employees want to get an extra feeling of protection, so in your section we have lots of suction. That suction, by the way, should have pulled those acetone vapors away from you. I'll talk to Oscar about putting in a work order to have maintenance check the motor and the ducts.
"For you, Jim, we'll start your training with respiratory protection. The first thing you need to know is the difference between the various respirators we have, and also when you should use each type and when you shouldn't use them.
"You had the plain-paper mask with one strap. These come ten to a bag. They are only for non-regulated materials. The janitorial staff likes them when they are dumping the trash cans; that is the only time they should be used."
"But I've seen guys with masks that looked like that," said Jim. "What where they?"
"In the manufacturing area we use several types of masks, and what you probably saw were the disposable, N95 dust respirators. They have been tested by NIOSH, which is a government agency that does research for OSHA. The N95 may look similar to the dust mask, but only because they are both white--that's where the similarity ends. The N95 has two straps, and an approval number is printed on the respirator. When it's properly fitted to you, you can be confident that the N95 will provide you protection from dusts primarily and some other materials. The N means that it is not resistant to oil vapor, so we don't use those masking in the fabrication shop. And the 95 means that it provides 95 percent filtration efficiency of particles.
"We also use what are called tight-fitting, air-purifying half- and full-face respirators," Barry added. "They are also approved by NIOSH, and they have the ability to protect you from a wider variety of materials, just by changing out the cartridge and/or filters on the front of the mask.
"To ensure that you get properly fitted, OSHA requires several things.
- You had your medical examination. That's to ensure you are medically qualified to wear the respirator and it will not cause you any medical complications or put an undue stress on your body and its systems.
- Training. That's what you are getting now. You need to understand the different types that are available to use, when they can be used or cannot be used, and their limitations. You should also understand that information about the chemicals can be found on SDS, or Safety Data Sheets, that you can access and print from that computer station in the lunch room.
- Fit testing. This is a method of testing the fit of each respirator that you will use to ensure it fits properly on your face. There are two methods we use. For the N95, we use a qualitative fit test. You put on that hood over there, and you let me know if you smell or taste the special test material. I note the concentration level where you first notice it. You then put the respirator on, go back under the hood, and I spray the solution again. You will be doing some tasks such as normal breathing, deep breathing, and turning your head from side to side and up and down. Finally, you talk out loud and then breathe normally again. All the while, I'm spraying the solution. You determine if you smell or taste it inside the respirator mask.
"For the half- and full-face, tight-fitting respirators, we can use either the qualitative method or the quantitative method. This involves hooking your respirator up to a machine that measures either the particles inside the respirator versus the particles outside or the vacuum inside the respirator. The machine will then use that information to calculate a fit factor. The higher the fit factor, the better the respirator fits you.
Since it is getting late, let's get the fit tests done. We can continue with the rest of the classroom training tomorrow morning."
Does the Story End?
This is just the beginning. OSHA's respiratory regulations in 29 CFR 1910.134 require the three points that are described above, but they also require that you have a written program that outlines your company’s usage of respirators. 1910.134(c) will give you the topics that need to be included. In addition, that program needs to be reviewed on an annual basis. Make changes if necessary, but at least reread it to ensure all of the information is correct, personnel listed in the program are correct, and updates are being made as necessary. For example, under HazCom 2012 (GHS), MSDS is going away and being replaced by SDS. Add the date of the review to the title page or a revision page. Train your employees on the changes.
Respiratory protection is a living program. Make the revisions, do the training, and observe your employees. If they are using the respirators correctly, then your program is one to be proud of.
This article originally appeared in the November 2013 issue of Occupational Health & Safety.