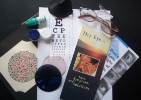
Beyond ANSI: Obtaining the Best Possible Eye Protection
Inarguably, form must follow function. That doesn't mean, however, that form has to trail by a large distance.
- By Peggy Kroesch, Jim Katz
- Sep 01, 2012
According to the OSHA website, "Thousands of people are blinded each year from work-related eye injuries that could have been prevented with the proper selection and use of eye and face protection. Eye injuries alone cost more than $300 million per year in lost production time, medical expenses, and worker compensation." There's no doubt that the International Safety Equipment Association's recently promulgated ANSI/ISEA Z87.1–2010 American National Standard for Occupational and Educational Eye and Face Protection (ANSI Z87.1-2010) has made the workplace much safer for many employees. Going into effect just over two years ago, the new standard updated guidelines last revised in 2003.
Manufacturers of safety eyewear products bearing the new standard must provide proof of protection against specific hazards, including optical radiation, impact and coverage, droplet and splash, and dust/fine dust, as well as provide products for different head sizes. The standard makes it imperative for any manufacturer of personal protective equipment to assess all possible workplace environmental risks and provide tangible technological solutions within the parameters of the new standard.
To comply with the new standard, an employer needs to consider a considerably more complex set of issues, including these:
1. How can I best select protective safety eyewear based on the hazards present in the plant?
2. Head sizes vary; which products provide the maximum protection, performance, comfort, and style to my employees?
3. What lens technology is most appropriate to the environment, such as high-pressure sodium lamps, metal halide/mercury vapor, fluorescent, or LED?
The simple solution may be to select protective eyewear products that meet or exceed the new ANSI Z87.1–2010 standard, but as a manufacturer of premium safety eyewear, we present additional and important factors to consider. We provide innovative eyewear solutions designed to provide maximum eye protection, enhance long-term eye health, and increase workplace productivity. Meeting the provisions set forth by ANSI Z87.1-2010 is both an imperative and a starting point for the major players in the safety eyeglass industry. These companies possess the technical know-how and manufacturing expertise to produce products that meet or exceed the new standards, but that is really only half the battle.
As obvious as the benefits of wearing effective eye protection may seem, too often workers provided with perfectly functional safety glasses fail to wear them at all appropriate times. Therefore, the prudent course of action is to examine every possible reason workers do not wear protective eyewear, and then thoroughly and comprehensively address each possible issue.
Although common sense dictates and statistical data prove that safety glasses are effective at preventing debilitating and costly eye injuries, a Bureau of Labor Statistics study found that 60 percent of injured workers were not wearing eye protection at the time of an accident.
Lost in a Fog
A September 2011 article in this magazine titled "Coming Out of the Fog" identified fogging as a significant reason that workers failed to wear protective eyewear. In fact, a 2009 study cited in the article named fogging as the number one vision-related reason for not wearing safety glasses. Fortunately, there are several methods of successfully minimizing the buildup of moisture that causes fogging.
A good place to start is with eyewear that is carefully designed to improve air flow and promote ventilation. Although air flow may seem an obvious solution, many products on the market still rely on antiquated shapes with little or no venting. By purchasing safety eyewear made by an established, well-known manufacturer with the expertise and resources to incorporate the most up-to-date designs, you can provide workers with glasses that won't fog.
Aftermarket anti-fog coatings, which are typically sprayed on, also can be very helpful. When using these products, safety managers and workers alike always need to remember to reapply these coatings from time to time, because they are not permanent.
Several safety eyewear manufacturers apply anti-fog coatings during manufacturing. These coatings typically last for the life of the product. We use a proprietary technology on both sides of all lenses.
Comfort is King
"They don't fit well." "They're too heavy." "They pinch my nose/temples." The chorus of comfort-related complaints about safety glasses is common, numerous, and persistent. Certainly, glasses that cause the wearer discomfort aren't likely to remain in place for more than a few minutes, let alone hours on end.
Here again, the best advice is to look for established brands with recognized design capabilities and manufacturing processes that utilize the latest and best materials. Reliable indicators include the following: flexible temples (the parts of the glasses that extend over the ears, commonly referred to as "arms"), soft material strategically located at some or all points of contact, adjustable nose pads, and high-quality hinges.
Seeing Everything Clearly
Clear, distortion-free vision is important to just about all workers, regardless of the complexity of the tasks they perform. The level of visual acuity provided by safety glasses is determined by several key factors. Lens material is at the top of the list. Manufacturers have several good choices, but polycarbonate lenses dominate because of a near perfect combination of shatter resistance, light weight, and optical clarity.
In many industrial and outdoor workplaces, glare resulting from reflected light can become a serious issue. Several brands offer the option of polarized lenses, which work by absorbing perpendicular light rays, the main cause of glare. And while polarized lenses may cost more, the benefits can far outweigh the costs.
Style Counts
Completely subjective? You bet. But how long do you think your employees will wear safety glasses that make them look like Mr. — or, worse, Ms. — Magoo? Inarguably, form must follow function. That doesn't mean, however, that form has to trail by a large distance.
Attractive shapes are not simply the product of a designer with a keen sense of style. Advanced designs, manufacturing techniques, and engineering skills are necessary to produce protective eyewear that meets or exceeds all of the applicable standards and looks great, as well. It takes the kind of attention to detail that can be attained only by years and years of industry experience.
Putting It All Together
From Kia to Mercedes-Benz, all automobiles sold in the United States have to meet the same safety standards. And while there's no doubt that the former makes a perfectly acceptable car, who wouldn't opt for the latter, given the choice? Despite some very obvious flaws in the analogy, the same basic idea holds true for protective eyewear. Fortunately for safety managers — and bean counters — the gap in price between premium safety glasses and ordinary brands is relatively small. That gap is nearly imperceptible when the value of workers actually wearing them is factored in to the equation.
The bottom line is this: The first and most important consideration when purchasing protective eyewear is that the product chosen meet the ANSI Z87.1-2010 standard. That, however, should not be where the decision ends. Premium safety glasses offer real-world advantages that far exceed any difference in price, and that makes them your best value.
This article originally appeared in the September 2012 issue of Occupational Health & Safety.