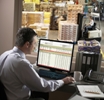
Putting Real-Time Information to Good Use
Forklift fleet and operator management systems can improve warehouse operations' safety.
- By Jim Gaskell
- Oct 01, 2011
According to OSHA, thousands of forklift-related accidents happen each year in the United States. Many of these accidents occur when safety regulations are ignored or violated; they often result in costly property damage, as well as operator injury and loss of productivity. In many instances, the number of workplace accidents involving forklifts can be reduced or even eliminated by implementing a forklift fleet and operator management system that provides real-time information about productivity and impact levels.
Historically, it was difficult to collect information generated at the forklift level. The small amount of information that was collected was delivered in a way that made it difficult to analyze and understand the information. Today's forklift fleet and operator management systems give managers access to real-time, meaningful information that helps them gain new visibility into operations to optimize productivity and identify opportunities to eliminate inefficiencies.
While these forklift fleet and operator management systems can help warehouse and material handling managers improve productivity and reduce costs, one benefit that is often overlooked is improving warehouse safety. A fleet and operator management system can help managers:
- Ensure compliance with OSHA regulations and inspections
- Stay current on operator certification and training requirements
- Prevent or reduce injuries on the warehouse floor with the system's impact detection capabilities
- Work toward an overall safer workplace environment and, in doing so, improve productivity and uptime
Ensuring Compliance with OSHA Regulations and Inspections
Ensuring compliance with workplace safety regulations is standard and important. All warehouses must operate in accordance to policies outlined by OSHA. Operating a forklift can be dangerous and cost a company in many ways if the operator is not trained and supervised properly. Wireless fleet and operator management systems can play a vital role in safety and compliance management through features such as impact monitoring and access control.
OSHA regulations are designed to help in ensuring safe environments for workers. Utilizing a forklift fleet management system, material handling managers can support compliance with these regulations by monitoring and logging the completion of daily operator checklists, as well as the amount of time operators spend performing safety checks. If users are not in compliance with OSHA regulations, managers can make immediate adjustments to ensure safety in the facility. By collecting information generated at the forklift level in real time and analyzing that information on a server, managers can optimize operator productivity and identify opportunities to eliminate inefficiencies associated with fleet and operator management.
Inspection checklists also can be integrated into the management console to guide operators through the inspection process. The electronic inspection checklists can be customized to ensure safe equipment and compliance with OSHA guidelines. Also, the next time OSHA personnel visit the warehouse, managers can easily access reports because fleet and operator management systems electronically organize the information.
Fleet management systems help busy managers easily access and maintain meaningful information, such as operator certification and training requirements. The system can alert managers of upcoming individual operator training needs and limit access to operators with required certification. All in all, overall warehouse care may increase and result in increased productivity and reductions in rack damage and work-related injuries.
Reducing Impacts, Improving Uptime
Some fleet and operator management systems on the market today have the ability to improve operator safety and reduce product damage with accurate reporting of truck impacts. Reliable and rugged truck sensors detect when impacts occur. When operators know that information such as this is sent immediately to their manager, they are likely to be safer drivers and take ownership of their trucks. Managers can locate these periodic impact reports and forward them to operators or peers to keep them informed of progress toward personal and operational goals. In addition, the system allows managers to distribute these reports via e-mail to specified individuals at pre-determined times.
A fleet manager's main goal is to run a safe, efficient warehouse. By reviewing organized fleet and operator information, managers can identify immediate opportunities for performance and safety improvement, as well as any operational inefficiency. By receiving the information in real time, managers can identify continuous improvement actions and realize how a fleet is really being used. For example, managers can find out:
- How many impacts went unaddressed that may lead to damaged lift trucks, racks, and other warehouse equipment in the future
- How to evaluate and isolate each impact by operator and then address operator behavior
- How to efficiently oversee operators' OSHA certifications
Overall, fleet and operator management systems provide reliable techniques and exemplary applications to help in assessing and controlling worker risk and protecting worker health while increasing productivity. This is a win-win situation for all involved. The systems can be programmed to help ensure the truck is in safe operating condition before it is used, for example. Also, managers can use organized forklift summary information to manage daily performance checks and preventative maintenance, as well as to expedite breakdown repairs.
A fleet management system delivers actionable data from forklifts through content-rich dashboards that help busy fleet managers focus on real opportunities and avoid wasted time deciphering mounds of data. Interactive interfaces on fleet and operator management systems help managers quickly identify and prioritize issues around compliance, impacts, and equipment -- allowing them proactively to address any issue before it turns into a bad habit. Warning indicators alert managers when expectations are not met, and specific details on each incident are available with just a few mouse clicks.
Every Day, Every Shift
Warehouse managers must remember that safety is their number one priority. Forklift and operator fleet management systems can help keep safety a priority every day, every shift. Information from reliable systems help managers gain the knowledge needed to manage a safer warehouse, where injuries are less likely to occur.
From top-level graphic summaries to deep-dive reporting, the forklift and operator fleet management systems deliver information through indicators, dashboards, and detailed reports; managers easily can compare actual performance to established goals, right from an iPad or laptop. Throughout time, trends may emerge that allow managers to deepen their understanding of an operation. Armed with historic reports, managers can elevate and evaluate benchmarks, fostering continuous improvement for operators and fleet alike.
Managing the warehouse with real information is a move forward to a safer operation.
This article originally appeared in the October 2011 issue of Occupational Health & Safety.