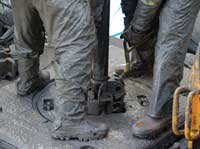
A Fresh Approach to Foot Protection
Work through the program elements and refresh your employees education and training on this topic, starting with supervisors
What are your employees doing about wearing the correct foot protection on the job? What are you and your supervisors doing to remedy what we in safety see all too frequently: An employee walks into the plant wearing damaged or worn-out safety shoes, or no protective footwear, even though the site requires it?
Admit it: Safety folks watch and listen. We typically notice and react to things many others never see in the workplace. We see potential in every anticipated hazard and try to think of the unanticipated. How recently have you watched your employees arriving for work and leaving and taken careful notice of their footwear? Occupational foot protection is very often ignored until a serious injury occurs. We "assume"employees understand and supervisors have discussed the need to wear adequate PPE on the job. We "assume" employees have and wear the correct foot protection for the hazard in their jobs.We "assume" total compliance. And we would be wrong!
How do you take a fresh approach to foot protection? You do it by working through the program elements, including the following.
Reexamine the hazards of your workplace. There have been changes since your last review of potential foot injury situations. These may be simple process changes, new equipment and tripping hazards, worn walking areas, broken/missing material handling items that may cause something to be dropped onto employees' feet, an out-of-service forklift requiring manual handling of heavy items, or something else. With the collapsing economy, the problem may be employees who were moved into new duties but do not realize the hazards associated with the tasks. Or more temps and less-seasoned employees are employed to save other costs.
As you examine the hazards, you have to consider the employees, too, from poor attitudes to impairments that may create situations causing foot injuries. Don't forget to evaluate your lifting aids and material handling equipment.
Survey the work practices. As you evaluate and watch employees coming to work, conducting shift tasks, or leaving, carefully evaluate the work practices that need correcting, such as untied shoes, inadequate foot protection, visitors or office staff visiting shop areas while wearing inappropriate foot protection or not wearing foot protection at all. With the complete array of safety-toed footwear available in all styles, you often have to ask specifically whether an employee is indeed wearing ANSI-approved safety shoes. Ask (for information, not accusingly!) about the shoes/boots, etc.
Evaluate your selection process anew. Make sure you have a resource for purchasing safety footwear, and keep this up to date. There are mobile units that will come to your site and allow employees to try on shoes/boots for a perfect fit. (Later in the day is better.) Online sites are helpful. Today's manufacturers are extremely savvy as to sizes, weight, style, and breathability of the materials. Examine the specific protections and know that all of your employees may not be able to wear the same shoe brand.
Read the injury history and review written policies if you have them. If your company needs a foot protection policy, get one and make sure each employee is aware of it. Spell out clearly what is required, why the company is implementing such a policy, and how the employee and supervisor are responsible for ensuring the correct foot protection is worn while on duty. If new employees are required to sign an agreement that they understand the safety rules of your workplace, make sure existing employees have done this, too.
Don't forget your temporary workers or summer interns. Every person who enters the work site has the potential for injury. When a foot injury occurs, it can be costly in time, missed work, and the lost expertise of specialized employees. And most such injuries are preventable.
Near-misses matter. They reveal hidden injury potential that sometimes is quietly passed off as the cost of doing business. Few employees or supervisors want to call attention to near-misses in the workplace; the truth comes out clearly when a serious injury occurs and employees are interviewed, saying similar incidents have happened and the supervisor knew about them.
Next comes communication. Refresh your employee education and training on this topic, starting with supervisors. Make sure they, too, understand the need for proper foot protection and that as immediate supervisors, they are personally responsible for ensuring every employee is wearing correct foot protection.
Too often, supervisors try to throw the responsibility to Safety. In reality, we are the coordinators for the program and they are the daily line watchdogs.
Seeing the Bigger Picture
Occupational foot protection is about more than shoes alone. Don't forget to train the workers to lift correctly as a way to reduce dropped items. Explain when lifting aids and safety shoes are required.
All safety programs require upkeep and benefit from trying new approaches. For occupational foot protection, the potential for serious injury exists on every shift, in almost every task. Our job is to reduce potential through thoughtful evaluation of the work being done, anticipate changes and increases in hazards, and correct the situation before an injury or nearmiss happens.We in safety also have to be approachable by employees and supervisors alike and take seriously any concern that is offered, no matter how crazy it may sound. Part of our talent is to defuse a potentially hazardous situation to the extent possible and educate at every opportunity. Our employee safety depends on it every day.
This article originally appeared in the April 2009 issue of Occupational Health & Safety.