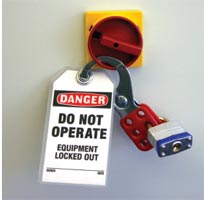
Lockout Basics
To encourage lockout, component manufacturers are now incorporating means of lockout into the device design so tagout will not be an acceptable alternative.
- By L. Tyson Ross, P.E., CSP
- Sep 01, 2008
It is tempting to think in simple terms about lockout/tagout—that you merely need to power down a machine and put a lock through the deenergized disconnect to achieve safety. The reality is that it’s not that simple, and it’s dangerous to think otherwise.
Through OSHA (if nothing else), companies have an obligation to provide a safe working environment for their employees. They must be committed to protecting the health and safety of each employee as a priority of the company. In terms of lockout/tagout, OSHA regulation 1910.147 explains the control of hazardous energy.
“The servicing and maintenance of machines and equipment in which the unexpected energization or start up of the machines or equipment, or release of stored energy could cause injury to employees. This standard establishes minimum performance requirements for the control of such hazardous energy.”
Examining the OSHA 1910.147 document, it quickly becomes apparent that the document’s authors believe that the best way to prevent injuries from unexpected energy is to remove the energy from the equipment and prevent it from returning to the equipment while it is being serviced. This is accomplished through a comprehensive lockout/tagout policy or procedure.
Lockout Policies and Procedures
An effective hazardous energy control program is not a haphazard set of guidelines. Instead, it needs to be driven by company policy and instilled into each employee. The policies set by a company create the environment in which an employee lives his daily work life. A culture that encourages a methodical and consistent approach to servicing equipment, including lockout, will result in fewer injuries or lost time incidents than an environment that stresses lost production.
Once a company policy is in place, the next step is the procedure. What are the characteristics of a successfully implemented hazardous energy lockout/tagout plan?
First, begin by creating a simple inventory list detailing the machines, equipment, and processes that expose employees to hazardous energy. This process may require an audit of the plant and is an excellent time to engage all affected parties. Potential personnel to include in this audit are the plant health and safety manager, engineering, tradesmen, machine operators, and others. Because employees can be so used to their daily routines that they ignore hazards, an engineering firm or safety consultant also can lead the official inventory. The list needs to include some key information, such as the machine name, the types of hazardous energy associated with the machine, the machine location within the plant, and the process that the equipment performs.
Next, using the list generated, list all required energy isolating devices associated with each piece of equipment. This may seem like an obvious step, but it requires you to look at the equipment again to determine the potential methods that can be used to remove hazardous energy from the equipment. You may be surprised by the results.
For example, after an energy isolation audit, an employer uncovered an embarrassing surprise. One particular piece of equipment had an electrical disconnect at the main panel, as well as pneumatic circuits associated with it. During the audit, it was discovered that the nearest air isolation valve associated with the machine was located at the main plant air header line. The main plant air line was located 25 feet above the floor, the main isolation valve was located 24 feet, 6 inches above the plant floor, and there was no visible means of accessing the isolation valve without a sky lift. This circumstance existed ever since the equipment was installed, but it was an enlightening discovery brought about by simply trying to list all energy isolating devices associated with the machine.
Following the listing of all required energy isolating devices, specific procedures must be developed for the lockout of the equipment. The procedure should include the following:
• Proper equipment controlled shutdown
• Energy isolation
• Blocking, securing, or relieving stored or residual energy (including gravity)
• Placement of the lockout/tagout devices
A key part of the development of the procedure is the creation of the lockout placard and tagged lockout points. This is only one piece of the procedure, however, and it should be not only systematic, but also communicated to all employees. Training on how to execute the lockout procedure is essential to developing a safety-conscious culture within an organization. The procedure should cover not only how to apply locks to the equipment for lockout/tagout, but also the proper procedure on how to remove locks and how to apply power to the system after lockout.
Some employers have developed lockout procedures that require a third-party witness, such as a maintenance supervisor, to observe each person removing his or her own lock prior to re-energizing the equipment. Although this level of control is not necessary for a successful lockout/tagout procedure, it is an example of a thorough approach that leaves nothing to chance.
The procedure also needs to consider how an abandoned personal lock should be removed from a piece of equipment. For example, how does the plant handle a scenario in which a contractor working on third shift leaves his lock on a machine and goes home? If the machine needs to be powered up on first shift, does the plant call the contractor back in? Or does the plant develop a plan to remove the lock, following a stringent set of guidelines?
Lockout Is Personal
After the lockout placard is created and the lockout procedure is implemented, someone will use that placard to isolate and lock out the energy source for the equipment. The lockout device must be a personal device for the affected employee working on the locked out equipment. When a person has a lock on a machine, it is potentially his life on the line. That lock is a personal guard to accidental machine start up or energization, so its removal should be under that person’s control at all times. To make it even more personal, employees’ locks should have a unique label or tag identifier, including the person’s name, department, and contact information, or even a photo.
Alternative Measures to Lockout
Based on OSHA 1910.147, does equipment need to be locked out any time it is being worked on? The short answer is yes. However, there is an exception that states:
“Minor tool changes and adjustments, and other minor servicing activities, which take place during normal production operations, are not covered by this standard if they are routine, repetitive, and integral to the use of the equipment for production, provided that the work is performed using alternative measures which provide effective protection.”
But what does the term “effective protection” mean? One interpretation is that the alternative means provides the same protection as a full system lockout without forcing a full system lockout.
In automotive manufacturing, a robotic welding line may have 60 robots that are all controlled from one PLC controller. The welding robots have welding gun tips that wear down as the production day continues. Changing the gun tip is a part of normal production and is considered to be routine, repetitive, and integral use of the equipment. Locking out the entire line of 60 robots to change a single tip is impractical for a normal production environment, so alternative measures to lockout are commonly used.
How is the alternative protection accomplished? Typically, a single robot or zone of robots has a local energy isolation switch that is coupled with local controls. Using the local controls, a user will request the shutdown of a robot or group of robots, and the control circuit will automatically isolate the hazardous motion energy for the robot zone. Using control reliable circuits and monitored power circuits, the system ensures that power is removed from the system before a local energy isolation switch is opened and a personal lock is placed on the local switch.
However, by using self-monitoring power circuits, which constantly check to see that hazardous power is removed from the circuit, an energy-free zone can be created that is isolated from the rest of the “live” cell. This provides a more practical alternative for the routine, repetitive tasks that would otherwise require a full lockout procedure.
The topic of alternative measures to lockout is complex and is introduced here to indicate that acceptable alternatives exist. Before implementing any alternative measure to lockout in a facility, it is recommended to consult a safety controls specialist.
What About Tagout?
When lockout is not a viable option, OSHA provides guidance on the use of related tagout measures. OSHA 1910.147 states:
“If an energy isolating device is not capable of being locked out, the employer’s energy control program under paragraph (c)(1) of this section shall utilize a tagout system.”
According to this statement, it seems as though a tag system is a perfectly acceptable method for controlling the energy in a system. However, OSHA takes a stringent interpretation in that the only time tagout is accepted is when an isolation device is not capable of being locked out. Recent interpretations of the OSHA regulations have made the use of tagout as an acceptable alternative means of hazardous energy control very difficult to achieve. To encourage lockout, component manufacturers are now incorporating means of lockout into the device design to the point that tagout will not be an acceptable alternative to lockout.
If you can lock it out, the energy isolating device should be locked out. This is a pretty basic but simple principle that precludes the option of tagout.
The key to success is thinking of safe lockout/tagout methods as a culture that is cultivated by company policies. Developing the appropriate habits and culture for lockout/ tagout is typically the most difficult aspect; then, the actual mechanics of locking out a piece of equipment are simplified. With appropriate lockout procedures in place, locking out a machine becomes both simpler and safer.
This article originally appeared in the September 2008 issue of Occupational Health & Safety.