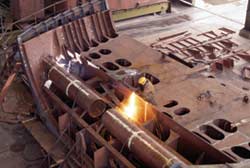
Unique Hazards of Shipbuilding and Modular Construction
This site learned that multiple precautions (even if redundant) must be employed to enhance safety for those working around suspended loads.
- By Murv Granderson
- Aug 14, 2007
THIS article by Northrop Grumman Ship Systems, Inc. (NGSS) addresses lessons learned from a fatality at its New Orleans facility involving a suspended load.
The shipbuilding industry faces many unique hazards. Like all major shipyards, NGSS builds its vessels through modular construction. In modular construction, NGSS builds hundreds of separate units that are assembled into larger units and then integrated into the vessel.
The modular construction process results in an extremely dynamic work environment in which the job site continually changes, with employees and materials constantly in motion. Very few operations involve a static "assembly line" where conditions are uniform and subject to constant controls. Nearly everything and everyone associated with vessel construction will, at one time or another, be in transit as the unit construction process takes shape.
NGSS Safety and Health Program
In early 2002, NGSS embarked on its "New Vision for Safety," which emphasizes personal responsibility for safety performance by the workforce. In launching this New Vision, NGSS established specific goals regarding safety and health and identified clear paths to achieve those goals.
The New Vision includes all stakeholders in the shipbuilding process and is designed to enhance employee safety and health. This process requires "buy in" from Operations, Facilities, Upper Management, support organizations, and, above all, the workforce.
In adopting the united approach, NGSS formed cross-functional stakeholder teams and strengthened its employee Safety Action Teams (SAT) to meet its goals of reducing injuries and illnesses. Moreover, NGSS entered into a Strategic Alliance with OSHA for its shipyards in Louisiana (New Orleans, Waggaman, and Tallulah) and Mississippi (Pascagoula and Gulfport). The Strategic Alliance includes the active cooperation and participation of the collective bargaining representatives for the workforce, including the Metal Trades Department, AFL-CIO and the International Brotherhood of Electrical Workers.
The New Vision initiatives had a significant impact on reducing injuries and illnesses across the sector. In 2002, the total case incidence rate (TCIR) was 32.9 per 100 workers. This TCIR, in part, reflected the unique and hazardous nature of the shipbuilding industry. The initiative, however, sought to reduce the TCIR to 22.0 per 100 workers by the end of the first quarter of 2005. NGSS exceeded its TCIR reduction goal. Indeed, for the year ending 2006, NGSS’ New Orleans facility reduced its TCIR for the year to 9.6--a 70 percent decrease from the facility's 2001 TCIR of 32.2.
The Fatality
One of the unique hazards facing the shipbuilding industry involves employees working near or under a suspended load. It is widely recognized in the industry that certain operations can be accomplished only by employees working under a suspended load. In light of these operational requirements, the industry has been striving to find ways to mitigate the exposure to this special hazard for employees working in this manner. Indeed, this very issue of working under suspended loads was raised as an agenda item at the Maritime Advisory Committee on Occupational Safety and Health (MACOSH) meeting on Sept. 26-27, 2006.
Despite the systemic changes to its safety and health systems and culture, NGSS’ New Orleans facility incurred a fatality in July 2006 when a suspended load struck an employee at the facility. In the incident, a portal crane had been suspending and traveling with a mast unit for a vessel under construction by NGSS. The mast unit was scheduled to be set at a designated staging area on the ground pending its integration. As the crane operator boomed down to position the load, he observed that the load was approaching the boom angle's rated capacity. The operator and Crane Foreman halted the travel of the unit to its designated location and made arrangements to secure another crane to assist with the lift. For several hours, the mast unit remained suspended approximately 4 feet off the ground.
While it was suspended, a General Superintendent decided to inspect the underside of the mast unit. He sought to inspect a particular component to assess how to integrate the mast unit onto the vessel. With the General Superintendent beneath the suspended unit, several employees voluntarily traversed under the load to greet the General Superintendent. Unfortunately, a sling holding one end of the spreader beam broke, causing one side of the load to fall to the ground and strike one of the employees beneath, causing the fatality.
Lessons Learned in Controlling the Hazard of Suspended Loads
NGSS cooperated fully with OSHA in the investigation of the accident. In the end, the General Superintendent and other employees did not heed policies in place to prevent exposure to the hazard of the suspended load. In the investigation, however, NGSS recognized it could take enhanced measures to minimize the need for employees to work near or underneath a load and to protect employees in the rare instances they would have to work in these conditions. At the conclusion of OSHA's investigation, NGSS and its unions agreed to take several additional measures to protect employees from the hazards of special lifts (i.e., over 25 tons) by taking the following actions:
1. Perform a risk analysis of each of the three phases of the lift process (turning unit, traveling with unit, and setting unit).
2. Clarify company policy to eliminate, where feasible, static periods of the lift process that would leave the unit suspended in the air. In exceptional circumstances when a static period in lift occurs, policy must require an effective means to restrict access (e.g., yellow caution tape) plus continuous posting of sufficient personnel around the lift area to prohibit access by employees to the area under suspended loads.
3. Require supervision of lift by a "Lift Coordinator" who has ultimate responsibility and authority for ensuring that all employees (managers, supervisors, and craft employees) follow lift safeguards. The coordinator will accompany the lift while it is traveled to insure compliance with all safeguards. This authority shall include the responsibility to shut down the lift process for any failure to follow established safeguards.
4. Retrain all employees and contract employees regarding the policy prohibiting employees from being under a suspended load.
These actions, agreed upon with OSHA, reflect just some of the actions taken by NGSS and its unions to address this hazard. Among other actions, NGSS addressed policy violations by its employees; revised, strengthened, and formalized its processes and procedures; replaced equipment connected to the incident; enhanced the involvement of its Engineering and Quality Assurance functions in the lift process; and revised its training curriculum for Crane Operators and Riggers.
These precautions recognize that, because of the consequences associated with the hazard of suspended loads, multiple precautions (even if redundant) must be employed to enhance employee safety and health. Ultimately, the best precaution against similar incidents comes from an enhanced culture of accountability, high employee involvement, and individual responsibility for safety and health. NGSS strives to reach these goals and obtain VPP status for all locations in Mississippi and Louisiana in 2007.
This article originally appeared in the August 2007 issue of Occupational Health & Safety.