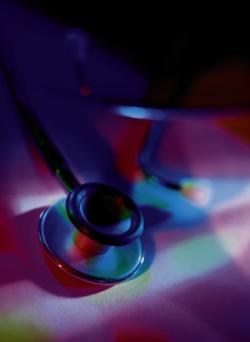
Why Safety Training May Not Be the Answer
A needs assessment or gap analysis can be performed in a number of ways. You can simply ask employees why they aren't doing what you want them to.
IMAGINE you are ill and make an appointment with your physician. You walk in
the door, register with the receptionist, and are escorted to an exam room. A
few minutes later, the physician walks in with a syringe filled with medicine.
He asks you to roll up your sleeve. As your eyes widen, you exclaim, "You
haven't even examined me yet!" As he walks closer with the syringe, he replies,
"That's all right. Most of the time, this usually does the trick."
While this scenario may seem ridiculous, how many times have we approached a
safety problem with a "syringe" full of training without diagnosing the
underlying issue?
Safety professionals are often expected to provide training to employees. If
the training is required by OSHA, then it clearly must be provided. However,
training is often used as a quick-fix solution to performance problems. The
trouble is, the performance problems may not necessarily be resolved with
training. In other words, lack of knowledge may not be the culprit.
To throw training at a performance problem when there are other issues
hampering performance is an ineffective use of your resources. In addition to
the direct cost of the training, indirect costs such as taking employees out of
production to attend can be substantial. To determine the correct fix, you need
to get to the root of the performance problem before you offer training.
Simply stated, a performance problem exists when employees do not do what the
organization and management want them to do. While certainly performance
problems can and do arise from a lack of training, often they don't. As a
general rule, training should be considered only after all other issues
affecting performance have been addressed. In other words, training should be
the last consideration and not the first.
In fact, providing training when the problem does not stem from lack of
training may even work against you. Training or telling employees how to do
something when other organizational barriers prevent them from doing it will
create resentment. For example if employees are not wearing required personal
protective equipment, will just telling them why they should or training them to
wear it really make a difference? Perhaps the PPE is not readily available or
maybe it is uncomfortable and interferes with their ability to perform their
job. Or maybe peers or supervisors put pressure on the employees that act as a
disincentive for the use of PPE. More training is just going to add salt to the
wounds.
Getting to the Root of the Problem
Some of these underlying issues
are not going to be simple to address, which may be why the "spray and pray"
approach to provide training is so often used. Peer pressure issues may require
a special approach, such as behavior-based safety, situated learning approaches,
or mentoring techniques. Lack of equipment may have to be addressed by
management. Generally, however, many performance problems are not nearly that
complicated if you take the time to find out the underlying cause.
Regardless of what is the final solution, the first step in addressing a
performance problem is trying to understand what is actually causing the gap.
Skipping this step is what often brings us to the quick-fix training solution.
We make the assumption that we know the reason for the gap and decide the
employees don't "get it," so we send them to training.
Getting to know the reason for the gap is sometimes called a needs assessment
or gap analysis and can be performed in a number of ways. The most frequently
overlooked approach is simply asking the employees why the desired performance
is not being done. Surprisingly, they may just tell you. How you approach these
interactions will depend on a number of factors. Each organization is different
as to the best approach, and a lot of the decision has to do with the
relationship and amount of trust already established.
You can ask employees in interviews, focus groups, or with questionnaires.
Informal interviews are often the easiest way to get this information. A couple
of words of caution should be considered before you begin. First, if you are
going to ask employees their ideas and if they tell you, then you need to at
least address the issue. Asking people and then ignoring what they tell you will
create even more resentment. If you don't plan on sincerely addressing the
issue, then don't ask the question, and you can probably stop reading this
article.
Second, you may hear something you don't like or want to believe. Understand
that individual as well as organizational defenses do exist. Groupthink often
can make the organizational defenses much stronger. The safety department or
human resources department does not want to hear that it may be part of the
problem--nobody does. While this may not necessarily occur, you need to
understand that, if it does, you have to address that issue as well, and in a
way that is non-defensive. This feedback, though painful, is huge and valuable.
Anyone who has done considerable training will know that the negative feedback
provided in the evaluations is always the most helpful. Your accepting and
addressing problems that may exist in your own backyard will demonstrate to
employees and management alike that you are sincere and committed to making an
improvement. If you ignore them, the doors of acceptance for others will close,
as well.
Don't assume the problems are all yours, however; just be prepared in case
some of them are.
To get to the root of a performance problem, you should use the same
objective approach you do when conducting accident investigation, which is
getting at the root cause without being judgmental or placing blame. This same
attitude must be taken to get to the bottom of a performance issue. You should
question a variety of employees, but particularly get input from seasoned,
well-respected employees. When you get the feedback from these employees
regarding the performance problem, you need to consider getting these same
employees involved in the solution, as well. OSHA Safety and Health Management
Guidelines stress the importance of employee involvement. By getting these
people involved in the solution, not only do you get their support (remember,
people support what they help to build) and gain their respect, but, more
importantly, you get input from those people who have the mastery in the actual
job performance. Like the expertise you have in safety, the expertise of these
people is in getting their jobs done. They often have solutions but perhaps have
never been given the opportunity to express them.
Using Focus Groups
Formal focus groups can be another good
approach. Focus groups can be conducted in a number of ways, and there is
considerable literature available that can help you plan a focus group. Your HR
or Training and Development department can probably assist, too, which may have
the added benefit of keeping it objective.
On simple, less formal terms, you can assemble a small group of between five
and 15 employees. You need enough that a good discussion can occur, but not so
many that people don't have an opportunity to talk or feel uncomfortable
talking. This is a good way to address a specific safety performance problem and
can also be a good way to begin establishing trust and strengthening
relationships while looking at general safety issues.
Generally, your role should be to start the discussion and keep it focused on
the topic while at the same time not being too rigid. You need to avoid giving
your subjective opinion about the issue, although providing safety guidance is
fine. So avoid "that won't work" statements--though something like "Well, that's
a good idea, but according to OSHA's lockout/tagout standard, we have to . . .
." is appropriate.
Remember, the purpose is to discover the employee's reason (or perceived
reason) for the performance gap. And, again, don't allow yourself to get
defensive. If the group suggests the safety department is not doing something,
don't throw up the shield and defend a position. Instead, encourage them to
provide more detail and give their solutions. Sometimes when people talk through
the issues and the other side is not defensive, they realize through
self-discovery that their perceptions might be wrong. This gives them a chance
to walk in your shoes and you in theirs. You should make sure everyone has an
opportunity to talk and not allow the discussion to be dominated by one or two
people. Ask, but don't force, the opinions of the introverts in the group. They
may not share their ideas unless specifically asked.
The data from the discussion can be captured on easel paper or a white board.
Let people know that not all of the issues can be easily solved or that not all
solutions are feasible, though most people will realize that. If your goal was
to build trust with the employees, look at the solutions that are easy to fix
and address them first. If you had a specific safety performance issue, then you
should focus on that. Some issues may need to be brought to upper management for
approval. Each company has different ways of dealing with this, and you'll need
to know how it is done at your facility.
Another technique that is useful allows participants to put all issues on the
table. In this technique, you allow all of the participants an opportunity to
write down their issues on paper. Then, going around the room, have each person
give one concern as you write it on the easel board. After going completely
around the room, go around again. Continue this process until every issue is on
the board. Usually, most of the issues are on the board after one or two passes.
Participants will have the same issues as someone before them, so the numbers
will get exhausted quickly.
Once all issues are up, begin grouping or clumping them together. Ask the
participants for clarification as you do, such as, "Jim, you said that managers
never provide the right equipment. Is that the same as Mary's comment about
there never being any equipment available?" By getting the participants to
clarify and consolidate, you can get consensus and agreement among the
participants. If they feel strongly that two issues are separate, keep them
separate and let them explain why. Allow the consolidation process to be
conducted by them, not you.
When you are finished you should have a pretty good, concise list of issues
and, most likely, if it was discussed, a good list of solutions, as well. Many
of the solutions suggested by the participants may be easy to address, some
harder. Again, most of the time they will know what is feasible and what isn't.
Now, you can get to work.
The Value of Personal Observation
There certainly are going to be
instances where lack of training will come up as an issue. It might be that
people need specific training, or new employees need more training, or
management may need training. Regardless, the true training issues will become
clear through the process.
Another commonly overlooked way to get to the root of a performance problem
is going to the floor and just observing. Using accident investigation as an
example, you would not consider a solid investigation to have taken place based
solely on someone's description or statement they gave you while sitting in your
office. You would want to go look at the site and see what actually occurred. In
the same regard, watching people work can provide tremendous insight into
performance issues. Quality programs that use Kaizen call this going to "gemba"
or "real place," which is the place where the work is actually being
performed.
By watching and observing, you can learn a great deal about safety
performance issues. One common example where a lack of this observation can
widen the gap of understanding is in regard to back injuries or other repetitive
strain injuries. Trainers are often asked to conduct back safety classes because
of an increased incidence of reported back injuries alone. The thinking is that
people do not "know" how to properly lift. Yet without seeing the work being
performed, just conducting the class may completely bypass the real issue.
Standing and observing the work in a non-threatening manner often will reveal a
clear understanding of the issues. Remember, training may still be needed, but
at least now, the training will be based on a clear, specific need and not just
a generally perceived problem.
The goal of this article was to begin to provide a foundation from which to
work. By addressing the underlying issues, the employees will recognize that you
are truly concerned, and you will go a long way toward establishing open
communication and trust. As the communication and trust grow, the employees will
be more willing to participate in the safety program, which in itself will go a
long way toward producing performance improvement. In the end, probably you'll
still have some training issues to address. At least your training can be
concise and specific, and the participants will find it actually more
meaningful.
The next time you encounter performance issues, try digging a little deeper.
Don't find yourself overlooking this important first step and making the
assumption that "everyone just needs more training."
This article appeared in the April 2007 issue of Occupational Health &
Safety.
This article originally appeared in the April 2007 issue of Occupational Health & Safety.