Toxic VOCs and Confined Space Entry
Most manufacturers and distributors are more than willing to make instruments available to potential customers for field trials.
- By Bob Henderson
- Nov 01, 2005
TOXIC VOC exposure is one of the most overlooked hazards in confined space entry. Volatile organic compounds (VOCs) are organic compounds characterized by their tendency to evaporate easily at room temperature. Familiar substances containing VOCs include solvents, paint thinner, and nail polish remover, as well as the vapors associated with fuels such as gasoline, diesel, heating oil, kerosene, and jet fuel. The category also includes many specific toxic substances such as benzene, butadiene, hexane, toluene, xylene, and many others. (A correction is appended to this article. Click here to view it now.)
Most VOC vapors are flammable at surprisingly low concentrations. For most VOCs, however, the toxic exposure limit is exceeded long before readings reach a concentration high enough to trigger a combustible range alarm.
Solvent, fuel, and other VOC vapors are routinely encountered in many types of confined spaces. Confined spaces particularly associated with VOCs include sewers; confined spaces at refineries and petrochemical plants, pulp and paper mills; confined and enclosed spaces on ships; commercial aviation fuel cells and wing tanks; as well as confined spaces associated with many other types of industry. In some cases, the presence of VOCs is due to materials being used or stored in the confined space. In other cases--especially sewers and other large, interconnected confined space networks--fuels, combustible liquids, or other VOCs accidentally introduced in one location easily can spread to other locations within the system.
Increased awareness of the toxicity of these common contaminants has led to lowered exposure limits and increased requirements for direct measurement of these substances at their toxic exposure limit concentrations. Photoionization detector (PID)-equipped instruments are increasingly viewed as the best choice for measurement of VOCs at exposure limit concentrations. Understanding the capabilities as well as the limitations of photoionization detectors is critical to interpreting test results and making decisions based on the use of this important confined space atmospheric monitoring technology.
Importance and Use of 'Broad-Range' Sensors
OSHA 29 CFR 1910.146, "Permit Required Confined Spaces," contains the requirements for practices and procedures to protect employees in general industry from the hazards of entry into permit-required confined spaces. Appendix E of 1910.146, "Sewer system entry," provides guidance for entries made into large, interconnected confined space systems, such as sanitary sewers. It also provides good advice for dealing with the presence of unpredictable atmospheric contaminants.
According to Appendix E, sewer entry differs in several fundamental respects from other permit entries. First, it is not usually possible to completely isolate the space (a section of a continuous system) to be entered. Second, because isolation is not complete, the atmosphere may suddenly and unpredictably become lethally hazardous (toxic, flammable, or explosive) from causes beyond the control of the entrant or employer. Unlike other confined spaces where it is possible to characterize the potential toxic hazards in advance, sewers are inherently unpredictable.
The more unpredictable the hazards, the more important it is to use sensors that are capable of providing alarm notification for a wide range of potential contaminants. Substance-specific sensors, such as the ones used to measure oxygen, carbon monoxide, and hydrogen sulfide, are deliberately designed to limit the effects on readings of other contaminants that may be simultaneously present. Broad-range sensors provide an overall reading for a general class or group of chemically related contaminants. Appendix E goes on to suggest that broad-range sensors are particularly suited for use during initial screening or in situations where the actual or potential contaminants have not been identified, because broad-range sensors (unlike substance-specific sensors) enable instrument users to obtain an overall reading of the contaminants present in the space.
Both traditional LEL and PID sensors are broad-range sensors. They can't determine which type of flammable gas or VOC is being detected, but they are excellent at determining when either of these classes of contaminants is present.
How Do PIDs Detect VOCs?
Photoionization detectors use high-energy ultraviolet light from a lamp housed within the detector as a source of energy to remove an electron from neutrally charged VOC molecules, producing a flow of electrical current proportional to the concentration of contaminant. The amount of energy needed to remove an electron from the target molecule is called the ionization energy (IE) for that substance. The larger the molecule, or the more double or triple bonds the molecule contains, the lower the IE. Thus, in general, the larger the molecule, the easier it is to detect.
On the other hand, small hydrocarbon molecules such as methane are not detectable by means of a PID. A PID is only able to detect substances with ionization energies lower than the energy of the ultraviolet photons produced by the PID lamp. The energy required to detect methane exceeds the energy of the ultraviolet light produced by the PID lamp.
PIDs may be equipped with a number of different types of lamps that produce photons of various energy ranges. The energy range of the photons produced by the lamp is expressed in "electron volts" or "eV" units of measurement. The most common types of PID lamps produce photons in the 9.8 eV, 10.6 eV, or 11.7 eV energy range. By far, the most commonly used PID lamp is one that produces photons in the 10.6 eV energy range. 10.6 eV lamps generally have much longer service lives and frequently last one to two years in normal operation. At the same time, 10.6eV lamps have an energy output sufficient to detect a wide range of VOCs. As a consequence, 10.6 eV lamps tend to be the most widely used.
Difference Between PID and LEL Sensors
PID and LEL sensors are based on entirely different detection techniques. Most LEL range sensors detect gas by catalytically oxidizing the gas on a pellistor-bead located within the sensor. Oxidization of the gas causes heating of the active pellistor-bead. The heating is proportional to the amount of gas present in the atmosphere being monitored and is used as the basis for the instrument reading.
Pellistor sensors are excellent for the detection of methane, propane, pentane, and other small hydrocarbon molecules. However, catalytic-bead sensors, at least when operated in the percent LEL range, are not readily able to detect "heavy" or long-chain hydrocarbons or the vapors from high flashpoint temperature liquids, such as turpentine, diesel fuel, or jet fuel. Consult the operator's manual or contact the manufacturer directly to verify the capabilities of the instrument design when using a catalytic-bead LEL sensor to monitor for the presence of these types of contaminants.
Limitations of Broad-Range Sensors
Broad-range sensors provide an overall reading for a general class or group of chemically related contaminants. Both pellistor-bead LEL and PID are broad-range sensors. They cannot distinguish between the different contaminants they are able to detect. The reading provided represents the aggregate signal from all of the detectable molecules present in the monitored environment. Unless an additional separation technique is used (such as a filter tube or separation column), broad-range detectors are not able to provide substance-specific readings.
Many manufacturers include a user-selectable library of correction factors (or "CFs") in the instrument design. In this case, the user simply selects "methane" or "propane" or any other correction factor in the library, and the instrument automatically recalculates readings according to the selected relative response. Changing the CF only changes the scale used to calculate the displayed readings. Selecting the "propane" CF does not prevent the sensor from responding to methane; it just reinterprets the readings as if they were entirely due to propane.
Using Correction Factors
Most PID-equipped instruments include a built-in library of correction factors. The same principles apply. Changing the PID correction factor (CF) or choosing a chemical from the on-board library does not make the instrument readings specific for that substance! Choosing the "hexane" correction factor does not make the PID a substance-specific detector for hexane; the PID will continue to respond to other detectable VOCs (such as benzene or toluene) that may be simultaneously present. Using the hexane CF simply tells the instrument to display the readings calculated as hexane measurement units.
PIDs are usually calibrated using isobutylene. Thus, the most commonly used measurement scale for most PIDs is isobutylene. It is very important to understand that no matter how comprehensive the list of correction factors, choosing the CF for any particular chemical never makes the readings exclusive or substance-specific for that contaminant. Also, if the specific nature of the VOC or mixture of VOCs is not known, PID readings are not truly quantified. Unless you are able to determine the precise nature of the VOCs being measured, readings should be thought of as "Isobutylene Units," or "PID Units," or units of whatever measurement scale has been selected from the instrument's library of correction factors.
Using Broad-Range Readings to Make Decisions
Instrument users frequently worry that they can't use a broad-range PID for VOC measurement because they need substance-specific readings for the contaminants present.
PIDs provide a single reading for the total detectable volatile organic contaminants (TVOC) present. In point of fact, many of the most common VOCs do not consist of a single type of molecule. They are comprised of a mixture of, in some cases, a very large number of individual molecular species. For instance, the size distribution of molecules in diesel fuel ranges from molecules with nine carbons (or smaller) to molecules with 23 carbons (or larger). However, the ratios of the various molecules present are fairly similar from one batch of diesel to the next. That allows PID manufacturers to experimentally determine a CF for use with this fuel. You don't have to go after the individual molecular types that may be present as a minor fraction of the diesel (such as benzene, toluene, xylenes, etc.) to provide a quantified reading. If you have a CF for the mixture, you can use this to quantify the readings for the entire range of molecules present.
Dealing with single-component VOC contaminants or mixtures is easy. Once you know which contaminant you are dealing with, simply assign the correct CF and set the alarms to the appropriate take-action thresholds for that VOC. Dealing with varying mixtures can be a little more challenging; in this case, the secret is to identify which chemical is the "controlling" compound.
Every mixture of VOCs has a compound that is the most toxic and/or hardest to detect and thus "controls" the alarm set-point that should be used for the entire mixture. Once the controlling compound has been identified, it is possible to determine a hazardous condition threshold alarm that will ensure the exposure limit for any contaminant potentially present is never exceeded.
The first step is to calculate (or look up) the exposure limits in isobutylene units for the VOCs of interest. Remember to leave the PID scale (correction factor) set to isobutylene units when using this measurement technique.
The exposure limit in isobutylene units (ELiso) is calculated by dividing the exposure limit for the VOC by the correction factor (CFiso) for the substance. For instance, the TLV® for turpentine is 20 ppm. If the CF for turpentine is 0.45, the ELiso = 20 ppm divided by 0.45 = 44.4 ppm. Many PID manufacturers include a table of ELiso values either in the owner's manual or in a separate applications note.
Consider a situation where you have three VOCs of interest: ethanol, turpentine and acetone. Let's say the owner's manual of the PID you intend to use includes a table with the following set of values:
Chemical Name |
10.6eV CFiso |
TLV® (8-hr. TWA) |
ELiso |
Ethanol |
13.3 |
1000 |
75.2 |
Turpentine |
0.45 |
20 |
44.4 |
Acetone |
1.2 |
500 |
416.7 |
Correction factors higher than 1.0 indicate the PID is less sensitive to the substance than to the isobutylene used to calibrate the PID. Correction factors of less than 1.0 indicate the PID is more sensitive to the chemical than to the isobutylene used to calibrate the detector.
Although turpentine has the lowest exposure limit, it is also the most easily detected substance of the three. Acetone is close to isobutylene in terms of detectability, with an exposure limit that is intermediate between those of the other two chemicals. Although ethanol has the highest exposure limit, it is also the least detectable of the three chemical. Thus, ethanol is the controlling compound when the "EL" exposure limits are expressed in equivalent "Isobutylene Units." Setting the PID to go into alarm at 75 ppm isobutylene units ensures that no matter which of the three chemicals, or combination of chemicals, is actually present, the exposure limit will never be exceeded.
Generally speaking, if a VOC is detectable by one manufacturer's PID when equipped with a 10.6 eV lamp, the same substance will be detectable by any other manufacturer's PID when equipped with a similar lamp. The correction factors may be quite different, however, between different instrument designs. PID users should never use the correction factors from one instrument for another manufacturer's design.
Using PIDs with LEL Sensors
Catalytic hot-bead combustible sensors and photoionization detectors represent complementary, not competing, detection techniques. PIDs are not able to detect methane and hydrogen, two of the most common combustible gases encountered in industry. On the other hand, catalytic pellistor-bead sensors are excellent for the measurement of methane, propane, and other common combustible gases. And of course, PIDs can detect large VOC and hydrocarbon molecules that are effectively undetectable by hot-bead sensors, even when they are operable in PPM measurement ranges. The optimal strategy for measurement of combustible range concentrations of combustible gases and VOCs is to include both types of sensors in the same instrument.
Limitations of PID Sensors
Humidity and moisture can have a serious effect on PID performance. Water molecules can absorb UV light without becoming ionized and thus quench the PID signal. The susceptibility of the sensor to humidity is very design-dependent. One of the most important determinants is the distance of the sensing electrode in the PID from the surface of the window of the PID lamp. Most PID designs deliberately position the sensing electrode as close as possible to the surface of the lamp window to reduce the effects of humidity.
PID manufacturers also provide tables of correction factors that can be used to correct readings for humidity at various temperature and RH conditions. Alternatively, it easy to correct for these ambient conditions simply by calibrating the PID in the temperature and humidity conditions in which the instrument is actually used.
A second, related issue is the condensation of water on the inside of the PID detector. When dirt or dust particles accumulate on the surface of the lamp, electrodes, or PID sensing chamber, they provide points of nucleation around which water vapor can coalesce to produce misting similar to the fog that develops on a bathroom mirror. In two-electrode PID designs, this can lead to surface electrical current flows directly between the sensing and counter electrodes. This "moisture leakage" can result in a rising signal or positive drift in the PID readings. The potential for moisture leakage can be reduced by cleaning the lamp and/or detector.
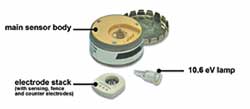
Some PID designs include a third "fence" electrode that serves as a short circuit path that mechanically interrupts current flow between the sensing and counter electrodes. In the case of designs that include a fence electrode, condensation of water vapor does not tend to produce a positive drift or interfere with the ability of the PID to obtain proper readings.
Pump vs. Diffusion
Whether or not the PID requires a pump or fan to move the sample through the sensing chamber is a function of the manufacturer's design. Many PID designs include a built-in pump or fan. Other designs allow the addition of a motorized pump to obtain samples from areas that are remote from the detector.
The easiest way to determine whether or not a pump is required is to evaluate the instrument before purchase. Most manufacturers and distributors are more than willing to make instruments available to potential customers for field trials.
The Best Approach
The best approach includes use of both substance-specific and broad-range sensors. PIDs are able to detect a wide variety of VOC and other toxic chemicals, including hydrogen sulfide, ammonia, phosphine, chlorine, and others. However, PIDs are broad-range sensors that cannot discriminate between a specific toxic contaminant and other detectable chemicals that may be simultaneously present. When a highly toxic specific contaminant such as H2S is potentially present, it is better to use a substance-specific sensor that responds only to that particular hazard.
Fortunately, PID-equipped multi-sensor instruments are available that include up to five channels of detection, allowing users the latitude of choosing exactly the combination of sensors they need to keep their workers safe.
Correction
The explanation given in this article under the subheading "Using Broad-Range Readings to Make Decisions" should have explained the controlling chemical in the example as written is turpentine, not ethanol. Author Robert E. Henderson said the example as originally conceived was based on the NIOSH recommended exposure limits for the three chemicals. The ELiso is calculated by dividing the exposure limit by the correction factor. The NIOSH REL for Turpentine is 100 ppm (8 hr. TWA). When the NIOSH REL is used to calculate the ELiso, ethanol is the chemical with the lowest ELiso value and is the controlling chemical. However, when the TLV for turpentine of 20 ppm (8 hr. TWA) is used, the calculated ELiso for turpentine is only 44.4 ppm, making turpentine the controlling chemical. The table should have listed both sets of calculated values and should have properly identified turpentine as the controlling chemical when the TLV is used as the basis of the calculation.
Chemical Name |
10.6eV CFiso |
NIOSH REL
(8 hr. TWA) |
ELISO (REL) |
TLV
(8 hr. TWA) |
ELISO (TLV) |
Ethanol |
13.3 |
1000 |
75.2 |
1000 |
75.2 |
Turpentine |
0.45 |
100 |
222.3 |
20 |
44.4 |
Acetone |
1.2 |
500 |
416.7 |
500 |
416.7 |
This article appeared in the November 2005 issue of Occupational Health & Safety.
This article originally appeared in the November 2005 issue of Occupational Health & Safety.