Understanding Oxygen Sensor Performance
Though mechanically complex, these instruments are easy--and vital--to use.
- By Bob Henderson
- May 01, 2005
OXYGEN deficiency is one of the most common of all categories of atmospheric hazards. It stands to reason that the sensors used to measure oxygen concentration are one of the most widely used types of sensors included in portable atmospheric monitors, especially those used in confined space monitoring procedures. In spite of the millions of oxygen sensor-equipped atmospheric monitors in service in the United States, however, there is still a lot of misunderstanding when it comes to the performance characteristics and limitations of this very important type of sensor.
Death in Confined Spaces
Fatal industrial accidents that stem from oxygen deficiency are unfortunately very common. Tragically, the same conditions and factors appear over and over again in confined space accidents. In one recent accident, four men died and three others suffered serious injuries due to oxygen deficiency in a confined space on board a barge.
The lack of oxygen was due to rusting (oxidation) of the exposed metal in the confined space. Workers had been engaged in maintenance work on the barge earlier in the day. During a mid-morning break, they realized one of the workers had failed to return and was still inside the barge. The worker and three who tried to save him died during the attempted rescue. Several more rescuers were seriously injured.
In another accident, a welder who had entered the hull of a barge became unconscious in the oxygen-deficient atmosphere. Again, the oxygen deficiency was due to rusting of the exposed metal in the shipboard compartment. Four other workers entered the hull to attempt a rescue of the unconscious welder and also were overcome. The welder died, and the other four workers suffered lung damage. In yet another recent incident, the owner of a small winery collapsed while taking a sample from a wine fermentation tank. A second person entered the tank to attempt a rescue and was overcome. Both people died. The cause of the accident was attributed to a lack of oxygen due to displacement by carbon dioxide created by the fermentation process.
In another accident, a worker at a pulp mill entered a tank without testing the air. The tank had been filled with colorless, odorless nitrogen as part of an inerting process, and the worker collapsed from oxygen deficiency. A second worker at the entrance to the tank also collapsed. Neither worker could be revived.
In all of these accidents, the cause of the fatalities was asphyxiation due to lack of oxygen. Oxygen deficiencies are extremely dangerous. At concentrations of 10 percent oxygen or lower, a single breath is normally all it takes to result in immediate unconsciousness, followed by irreversible brain damage or death if the unconscious individual is not quickly revived. Oxygen deficiencies are invisible to human senses. Without the use of an instrument capable of directly measuring the absence of oxygen, the only indication of the existence of an oxygen deficiency very well may be when workers begin to pass out.
What Is an Oxygen Deficiency?
The concentration of oxygen in normal air is approximately 20.9 percent. The balance (more than 78 percent) consists primarily of nitrogen. The remaining fraction includes small amounts of water vapor, carbon dioxide, and argon, as well as traces of other gases.
OSHA's 29 CFR 1910.146, "Permit Required Confined Spaces," contains the requirements for practices and procedures to protect employees in general industry from the hazards of entry into permit-required confined spaces. The standard defines an oxygen-deficient atmosphere as any atmosphere containing less than 19.5 percent oxygen by volume. Any atmosphere that contains less than 19.5 percent oxygen is hazardous and may not be entered by unprotected workers.
Confined spaces are particularly prone to the development or containment of oxygen-deficient atmospheres. The reason that oxygen deficiency is common in confined spaces is that they develop by mechanisms that affect the contents of the space and boundary surfaces. Causes of oxygen deficiency include microbial action, displacement, combustion, oxidation, and absorption and adsorption. Work activity is also an important cause. Use of solvents, paints, and degreasers or hot work can affect oxygen levels.
Any oxygen concentration other than 20.9 percent indicates an abnormal condition. A less-than-normal concentration of oxygen by definition indicates a greater-than-normal concentration of some other component or the presence of a contaminant in the atmosphere being sampled. Even when the oxygen concentration does not constitute a statutory hazardous condition, workers should determine the cause of the abnormal reading prior to entering a confined space. The safest approach is to initiate entry only when monitoring has determined that a "fresh air" oxygen concentration of 20.9 percent exists in the space.
Oxygen Enrichment
The concentration of oxygen in confined spaces is a concern from two standpoints. Too little oxygen can cause asphyxiation. Excessively high (or "enriched") levels of oxygen above normal oxygen concentrations dramatically promote or accelerate combustion and other chemical processes.
The definition of oxygen enrichment varies between different standards and regulatory documents. OSHA's 1910.146 references 23.5 percent as the concentration for oxygen enrichment. However, OSHA's 1915-Subpart B, "Standard for shipyard employment," specifies 22 percent. The latter value is consistent with non-mandatory recommendations from groups such as the National Fire Protection Association (NFPA). The most conservative standards specify 22 percent as the concentration above which the atmosphere is deemed to be hazardous due to oxygen enrichment. For this reason, an increasing number of instrument manufacturers use 22 percent as the default high-alarm setpoint.
Oxygen Detection
Most portable or survey instruments utilize fuel-cell type oxygen sensors, which are mechanically complex. Oxygen sensors generally contain a diffusion barrier used to limit or control the amount of oxygen that enters the sensor; a sensing electrode (cathode) made from a noble metal such as gold or platinum; a working electrode (anode) made from a base metal such as lead or zinc; and other components, such as external moisture barriers or filters. The internal sensor components are bathed in a basic electrolyte, such as a solution of potassium hydroxide or potassium acetate.
The principle of detection is very straightforward. Oxygen diffusing into the sensor is reduced to hydroxyl ions at the cathode:
O2 + 2 H2O + 4 e- ? 4 OH-
Hydroxyl ions in turn oxidize the lead (or zinc) anode:
2 Pb + 4 OH- ? 2 PbO + H2O + 4 e-
This yields an overall reaction of:
2 Pb + O2 ? 2 PbO
Fuel cell oxygen sensors generate electrical current. The amount of current generated is proportional to the amount of oxygen consumed. Oxygen-detecting instruments simply monitor current output from the sensor. Of course, this is a simplification of the way oxygen sensing instruments are designed.
The electrolyte may be buffered or consist of a solution (such as potassium acetate) that is less prone to poisoning or being ruined by gases such as carbon dioxide. The electrolyte also may be a semi-solid gel rather than a liquid. Use of a gel electrolyte improves low temperature performance as well as reducing the potential for leakage or drying out.
The working electrode seldom is a simple chunk of lead because this surface must be available and accessible for contact with oxygen molecules before the electrochemical reaction can occur. The working electrode usually consists of lead wool or some other finely divided form of the metal that provides a good surface area-to-volume ratio. Other design features can include temperature compensating thermistor-resistors, internal membranes, spacers, wicks, and current collectors. Numerous variations on these general design features are used to optimize the performance of an oxygen sensor for use in a specific product.
One of the most important design constraints is the build-up of lead oxide that develops in the sensor capsule over the life of the sensor. As lead is converted into lead oxide, an increasing fraction of the volume of the sensor capsule is occupied by solid material. If the sensor design does not include a provision for this increase, it will eventually rupture, possibly leading to leakage of electrolyte into delicate and expensive instrument electronics.
The lead wool in the working electrode in a fuel-cell oxygen sensor is consumed over time. When all available surface area of the lead (Pb) anode is converted to lead oxide (PbO), electrochemical activity ceases and current output falls to zero. At this point, the sensor must be rebuilt or replaced. Most fuel-cell sensors are designed to last no more than one to two years.
In most instruments, even when the instrument is not being used, the oxygen sensor continues to generate current and use itself up. Some instrument designs prevent the flow of electricity by breaking the circuit. This blocks the electrochemical reaction as long as the instrument is turned off and increases the effective life span of the sensor. The drawback to this approach is the need for a restabilization period (sometimes lengthy) when the instrument is turned back on.
The temperature of the atmosphere influences the output from fuel-cell oxygen sensors. The warmer the atmosphere, the faster the electrochemical reaction proceeds. For this reason, oxygen sensors usually include a temperature-compensating load resistor to hold current output steady. Microprocessor-based designs usually provide additional signal correction in software to improve accuracy further.
Cold temperatures can be a major factor that limits performance. The freezing temperature of electrolyte mixtures used in some oxygen sensors can be as high as minus 20°C (minus 5°F). Once the electrolyte freezes, electrical output falls to zero. The gel and liquid electrolyte mixtures used in more recent sensor designs, however, show much better cold temperature performance.
There are two fundamental variations in designs of fuel-cell oxygen sensors: "partial atmospheric pressure" and "capillary-pore" type designs. These variations reflect the mechanism by which oxygen diffuses into the sensor.
The partial pressure of oxygen (or pO2) is that fraction of the total pressure due to oxygen. Partial pressure oxygen sensors rely on the partial pressure of oxygen to drive molecules through the diffusion barrier into the sensor. Table 1 lists the partial pressure of oxygen versus the percent volume concentration at varying altitudes above sea level. As long as pO2 remains constant, current output is a reliable indicator of oxygen concentration. Shifts in barometric pressure, altitude, or other conditions that affect atmospheric pressure will cause a systemic change in sensor output. To illustrate this problem, consider a sensor calibrated at sea level where atmospheric pressure is 760 mm Hg. Now consider the same sensor at an elevation of 3,000 m (10,000 ft).
TABLE 1
PARTIAL PRESSURE O2 VS. % VOL AT VARYING ALTITUDES |
Height above sea level |
Atmospheric pressure |
Partial Atmospheric Pressure O2 (pO2) |
Concentration |
Feet |
Meters |
mmHg |
mmHg |
kPa* |
% Volume |
16,000 |
4,810 |
421.8 |
88.4 |
11.8 |
20.9%
|
10,000 |
3,050 |
529.7 |
111.0 |
14.8 |
20.9%
|
5,000 |
1,525 |
636.1 |
133.3 |
17.8 |
20.9%
|
3,000 |
915 |
683.3 |
143.3 |
19.1 |
20.9%
|
1,000 |
305 |
733.6 |
153.7 |
20.5 |
20.9%
|
0 |
0 |
760.0 |
159.2 |
21.2 |
20.9%
|
*19.5% O2 at sea level = 18 kPa
|
Although at both elevations the air contains 20.9 percent oxygen, at 10,000 feet the total atmospheric pressure is only 514 mm Hg, and the partial pressure for O2 is only about 107 mm Hg. Because there is almost one-third less force driving oxygen molecules through the diffusion barrier into the sensor, current output is significantly lower.
It should be noted that most instrument designs that use pO2 sensors include software to correct sensor readings for barometric pressure fluctuation. In the case of these designs, oxygen readings will not be affected by changes in ambient pressure within design parameters.
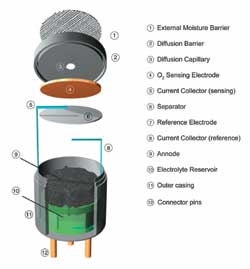
Figure 1 provides a simplified diagram of a capillary-pore oxygen sensor. These sensors utilize a narrow-diameter tube through which oxygen diffuses into the sensor. Oxygen is drawn into the sensor by capillary action in much the same way water or fluid is drawn up into the fibers of a paper towel.
Capillary-pore sensors are much less influenced by changes in pressure than partial pressure oxygen sensor designs. Although rapidly changing pressure leads to a change in sensor output, as soon as the diffusion barrier capillary has stabilized at the new pressure, the output will return to the previous level. Because the volume of atmosphere contained in the diffusion barrier capillary is very small, stabilization at the new pressure is usually achieved within 10 to 30 seconds.
This effect can be seen clearly when a properly calibrated capillary-pore oxygen sensor is taken on board a commercial jet. Initially the sensor reads 20.9%. As the jet takes off and begins to gain altitude, the pO2 drops, causing a drop in oxygen sensor readings. When the jet reaches cruising altitude (actually, when cabin pressure is stabilized at normal operational levels), the readings return to 20.9%. As the jet begins its descent prior to landing, pO2 increases, causing a rise in readings. As soon as the sensor is back at ground level (and the cabin is once again depressurized), readings will return to 20.9%.
Capillary-pore designs are potentially vulnerable to blockage of the capillary. For this reason, capillary-pore sensors include an external moisture barrier to prevent the pore from being blocked or plugged by solid materials, water, or other fluids.
Oxygen reading instruments used in confined spaces generally display readings in units of percent by volume concentration, regardless of the type of sensor that is employed. Readings are usually in increments of plus or minus 0.1 percent O2, with a full instrument range on the order of 0 to 25 percent oxygen.
Mechanisms of Oxygen Sensor Failure
Oxygen sensors may be affected by prolonged exposure to acid gases, such as carbon dioxide. Most oxygen sensors should not be used continuously in atmospheres containing more than 25 percent CO2. In some cases, prolonged exposure to the acid gas damages the basic (alkaline) sensor electrolyte. In other situations, high concentrations of acid gas produce a current flux that alters the normal expected output of the sensor at a given concentration of oxygen.
Use in extreme conditions can affect data provided by the instrument. Extreme conditions are any that exceed published operating specifications for the instrument. Users should always consult the owner's manual or contact the manufacturer directly before using an instrument in any unusual or extreme environment, including operation in cold or excessively hot temperatures. While the instrument may not pose an ignition or intrinsic safety hazard, the accuracy of readings may be adversely affected during use outside of design parameters.
As indicated previously, the working electrode in a fuel-cell sensor is consumed over time. When all available surface area of the lead (Pb) anode is converted to lead oxide (PbO2), electrochemical activity ceases and current output falls to zero. This is the type of sensor failure most frequently experienced by users. This failure is fail-safe because the oxygen deficiency alarm activates whenever current output falls below a minimum level. At this point the instrument will alarm continuously until the sensor is replaced, making it unlikely anyone would attempt to use it.
The standard method used to calibrate most oxygen sensors is to let the instrument automatically adjust its readings to match 20.9 percent while the sensor is located in fresh air. It is very important to "bump test" the oxygen sensor before each day's use. During the bump test, the proper performance of the sensor and alarms are verified by exposing the sensor to a concentration of oxygen below the oxygen deficiency alarm setpoint. Bump testing the O2 sensor can be done by exposing it to calibration gas packaged in small 34- or 58-liter cylinders or simply by exhaling onto the sensor. Readings should decrease to a level low enough to activate the low-oxygen alarm, then recover. Readings that fail to decrease or that require an abnormally long time to recover fully may indicate a problem with the sensor.
Oxygen sensors are among the most dependable, stable, and reliable type of gas-detecting sensors available. But no sensor can detect gas unless it is used. Understanding your instrument is important; using your instrument is critical.
This article appeared in the May 2005 issue of Occupational Health & Safety.
This article originally appeared in the May 2005 issue of Occupational Health & Safety.