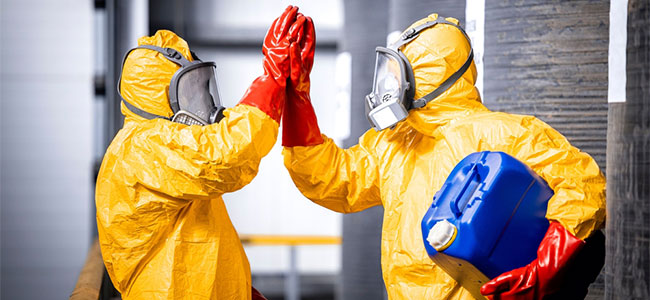
Helping New Hires Navigate Chemical Safety
Orienting new employees on chemical safety requires leveraging the right methods and tools to ensure a slate of learning objectives takes hold.
- By David Kopf
- Sep 06, 2023
Introducing new team members to chemical safety is challenging but crucial. The alarming 24.5 percent spike in hazard communication violations OSHA recently recorded is a glaring reminder of the stakes.
Trainers must balance their orientation’s thoroughness and efficacy, and that requires a structured approach, innovative methodologies, and timely execution. Done right, trainers can ensure that new employees are not just introduced to chemical safety protocols, but truly understand their depth and significance. That way, safety isn’t merely a protocol, but a practiced ethos.
Orientation Objectives: Crafting a Comprehensive Approach
A solid orientation is the foundation upon which safety practices are built, and there are many learning objectives when it comes to laying that foundation. When guiding newcomers on chemical safety, here are some essential elements:
- Understanding Hazards. New employees should grasp the vast landscape of chemical hazards. This includes not only recognizing but also proficiently classifying chemicals, understanding their properties, and appreciating the risks they pose.
- Chemical Storage Protocols. Proper storage of chemicals is pivotal. Employees should be aware of storage requirements, such as temperature controls, containment methods, and the significance of segregating certain chemicals to prevent adverse reactions.
- Handling & Disposal. Alongside understanding a chemical’s nature, employees must be versed in the nuanced protocols for safe handling. Additionally, they should know how to dispose of chemicals responsibly, keeping environmental impacts in mind and recognizing potential hazards.
- Hazard Communication (HazCom) and Safety Data Sheets (SDS). Adhering to HazCom principles is paramount in chemical safety. Employees should be adept at interpreting chemical labels and Safety Data Sheets (SDS). They must be trained to efficiently extract crucial safety information from these resources and understand its practical implications in their daily tasks.
- Personal Protective Equipment (PPE). Employees should be thoroughly educated on the different types of PPE available, such as gloves, goggles, respirators, and protective clothing. More importantly, they should be trained on when and how to use them correctly, as well as proper maintenance, storage, and regular inspection of PPE.
- Health Implications. It’s imperative for employees to understand both short-term (acute) and long-term (chronic) health effects of exposure. This knowledge empowers them to act proactively, recognizing early signs of exposure or distress.
- Emergency Protocols. Despite all preventive measures, emergencies can occur. Employees should be equipped with robust response strategies, from managing small-scale spills to navigating large-scale evacuations.
- Monitoring & Reporting. Introducing employees to tools that provide real-time monitoring for chemical leaks or air quality issues is crucial. Additionally, they should be familiar with mechanisms for reporting chemical hazards, near misses, or other relevant incidents.
- Inventory Management. A clear inventory system, especially for high-risk chemicals, ensures that potential risks are identified and managed promptly. New hires should understand how to access and update this inventory.
Methods for Effective Orientation
Carrying out a comprehensive chemical safety orientation isn’t just about presenting information — it’s about ensuring the lessons are absorbed and reinforced. Here are some approaches and tools that safety managers can utilize to achieve that:
- Blended Learning Approach. Marrying traditional classroom-style teaching with digital e-learning modules can cater to various learning preferences, enhancing overall comprehension and engagement.
- Mentorship. Experience is a powerful teacher. Pairing newcomers with seasoned professionals can provide on-the-job insights that standard training materials might overlook.
- Role-Playing & Simulations. Real-life scenarios or simulations, whether in a physical setting or a digital platform, can drastically improve hands-on knowledge. Role-playing allows employees to navigate potentially hazardous situations safely, reinforcing best practices.
- Hands-On Training. Theory and practice must go hand in hand. It’s pivotal that after learning the theoretical components, employees get the opportunity to apply their knowledge in controlled, real-world settings.
- Feedback & Group Discussions. Creating open channels for feedback and group insights can correct misconceptions, address questions, and refine training modules in real-time.
- Ongoing Webinars & Workshops. Safety standards and best practices are dynamic. Regularly updating employees through webinars and workshops ensures they stay abreast of the latest in the chemical industry.
- AR & VR. Technologies such as augmented reality and virtual reality offer immersive experiences, enabling employees to practice safety protocols and emergency response scenarios, for example, in realistic but risk-free virtual environments.
- Mobile Apps and Interactive Platforms. Digitized training materials, safety guidelines, and resources accessible via smartphones or tablets allow employees to review information at their convenience. Additionally, consider platforms that offer interaction such as gamified learning modules or quizzes. These can maintain interest and reinforce learning.
- Microlearning. Transforming comprehensive topics into bite-sized modules can significantly enhance retention. Microlearning delivers targeted information bursts, making it easier for employees to absorb, understand, and apply.
- Assessment and Follow-ups. Regular quizzes, simulations, or practical assessments can help gauge the employees’ understanding, ensuring any knowledge gaps are promptly addressed. Also, safety doesn’t stop after the initial orientation. Periodic check-ins, refresher courses, and updates ensure ongoing safety awareness and compliance.
By integrating these methods, safety managers can foster a mindset where safety becomes second nature, rather than just a checklist. That way, employees aren’t just aware of the rules — they live by them.
This article originally appeared in the September 2023 issue of Occupational Health & Safety.