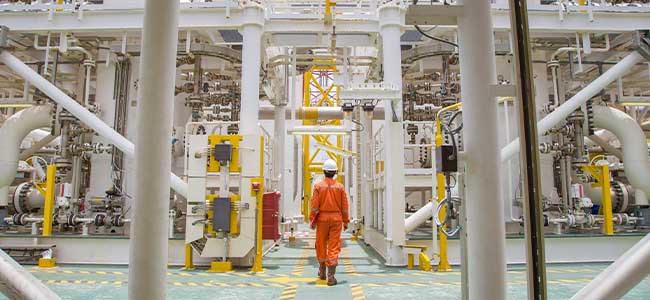
Every Worker, Everywhere, All at Once
How real-time location services are helping gas & oil companies implement individualized safety monitoring.
- By David Kopf
- Jun 01, 2023
If the goal of workplace safety means keeping every worker safe, then in many situations, that means keeping every worker accounted for. In oil & gas organizations, which have large workforces as well as workforces that can be widely dispersed, ensuring worker safety becomes a change due to size and scope.
Fortunately, there are tools to help them overcome that challenge and stay on top of individual worker safety. One of those tools is real-time location services (RTLS).
So what is RTLS? RTLS uses technology to track and monitor the real-time whereabouts of assets, employees or equipment within a facility or work environment. Depending on the manufacturer and implementation, RTLS utilizes various tracking technologies such as Radio Frequency Identification (RFID), Global Positioning System (GPS), WiFi or Bluetooth to provide accurate and up-to-date information on the exact location of employees.
RTLS systems often consist of a combination of hardware, such as tags or badges attached to assets or worn by employees, and software platforms that collect and analyze location data. The collected information can be visualized through dashboards or integrated with other systems for comprehensive management and decision-making. With those RTLS dashboards, networks and worker tags, organizations can both improve operational efficiency and enhance worker safety.
Safety and Efficiency
As mentioned, there are two sides to RTLS: business efficiency and safety. On the business side of RTLS, the technology can help address business challenges, especially in business sectors where operational costs are escalating. RTLS can help companies optimize resource utilization and track personnel in real time so that they can monitor workflows, streamline processes and locate individuals quickly and efficiently.
So, for instance, possessing an accurate count of workers at specific points is invaluable for managing both ongoing operations and key projects or turnaround phases. In that regard, it is essential to ascertain the flow of workers and their respective locations.
“It is closely tied to efficiency,” explains Veronica Turner, Regional Business Leader for the Industrial Safety Portfolio at Honeywell, which provides RTLS technology and services to companies in a variety of industries. “It helps you allocate the workforce effectively to the areas where it’s most needed, avoiding bottlenecks and situations where work crews hinder each other and are unable to finish their tasks due to waiting on preceding ones to be completed.”
While efficiency upsides are welcome and needed, the safety aspects of RTLS are where the technology really starts to shine. At the outset, simply being able to monitor the location of workers is a benefit to worker safety, but RTLS offers more specific benefits.
Safety Scenarios
For starters, when a worker has encountered trouble, such as a fall or an injury, they can use RTLS to notify the system. RTLS is not to be confused with two-way radios or similar devices, Turner notes, but RTLS systems incorporate “SOS buttons” on the tags that workers wear that workers can use to summon help.
But if a worker falls and does not activate their SOS button, the system can still get help to their exact location since the system is tracking them.
“If an employee working on an industrial site happens to fall, it will track the impact followed by no movement; an alarm will be triggered automatically if that worker falls and remains immobile,” Turner explains, underscoring that the system watches for lack of movement. “False alarms will be avoided if the worker simply trips and gets back up immediately,” she adds.
Turner also emphasizes that the RTLS devices or tags worn by workers are designed to be rugged and durable. In the case of Honeywell’s devices, she says they are designed for hazardous conditions and are certified Zone 1 and Zone 2 (ATEX, IECx), which are obviously important for oil and gas, as well as other industry settings.
Turner notes that RTLS can be used in a lot of industries, but she underscores that the type of work environment and type of work is important to consider. “While RTLS can be utilized in any setting, its value is particularly pronounced in industries dealing with hazardous conditions or materials,” she notes.
To that end, RTLS can help protect workers in settings and duties involving hazardous materials, such as chemicals, acids and other substances, that significantly increase the risk of safety incidents. Additionally, RTLS can help in workplaces involving constrained spaces, and physical obstacles within the work environment can also jeopardize employee safety. Naturally, those hazardous materials and workspaces are endemic to oil and gas workers.
Of course, RTLS can be proactive when it comes to worker safety as well. For instance, Turner notes her company’s RTLS system incorporates a fatigue monitoring algorithm that aids in tracking employees’ working hours, ensuring compliance with minimum rest periods before they are assigned back to the schedule.
Geofencing and Lone Workers
Another benefit of RTLS is geofencing, the ability to implement virtual boundaries for areas where workers can and cannot go.
In many industries, it is vital to have a means of isolating locations, such as those with lots of heavy machinery or vehicles in operation, to ensure worker safety. So, as a company’s headcount increases, it becomes even more crucial to remain attentive to all variables that can impact people’s well-being.
RTLS can play a significant role in this regard by implementing geofencing. Geofencing lets a company restrict worker traffic in specific areas to prioritize employee well-being.
“The platform administrator possesses the capability to designate areas on an interactive map, specifying whether an area is classified as a restrictive ‘hot area’ or a ‘white area’ where the flow of individuals is free,” Turner explains.
So, if a worker who does not have access to a limited area enters that work zone, the system will escalate alerts or alarms based on the security hierarchy and protocols within the organization.
Of course, while some workers might be in busy environments that require geofencing, there are also oil & gas workers that are completely on their own. Here too, RTLS can help. As long as the RTLS system can establish connectivity with a remote/lone worker’s receiver, it can track an employee who is working by himself or herself. But it can go further than that when part of a larger lone worker safety effort involving a variety of safety technologies, Turner notes.
“Obviously, RTLS is part of a safety ecosystem,” she explains. “We have more than just this device to offer a sustainable safety environment for the employee. We have personal gas detection devices that will track any gas intake and things like that. So by no means will the one [RTLS] solution will solve every problem, but certainly, as a way to offer a feasible, trackable way to monitor the whereabouts of workers and have the ability to rescue them if a safety situation was to arise, RTLS offers a very good value proposition.”
Emergency Situations and Mustering
Another notable feature of RTLS is location tracking during emergencies. This technology enables efficient tracking of individuals or critical assets in scenarios such as mudslides, explosions or building collapses, Turner explains. By utilizing this technology, the last known location of those workers or assets can be readily determined.
Another safety measure that RTLS can provide during emergencies or safety incidents is automatic mustering. Previously, in the event of a safety incident, individuals had to approach a reader and scan a card to be accounted for. But with RTLS, approaching the mustering area is sufficient for the RFD card signal to be detected, ensuring accurate accountability without additional requirements.
“One of the challenges that most businesses have is their inability to have real-time data for active people in the plant, particularly for individuals in specific zones,” Turner says. “However, using our system’s triangulation, you can have an accurate read of active people in a zone with a click of a mouse.”
Moreover, this technology enables the ability to differentiate between employees, contractors and visitors, Turner notes. So, in the event of an alarm, precise location information allows for immediate identification of where the alarm originated and who is involved.
Naturally, all this worker safety data becomes a boon in terms of training. Turner notes that reports can be downloaded and studied to enhance and tailor safety training modules. In the event of a safety incident at a plant or industrial site, a company can track data points such as an individual worker’s movements and adherence to assigned locations.
Approaching RTLS
If a company is interested in implementing RTLS, Turner advises not diving in but taking time to study the various offerings on the market and to especially consider their scalability and breadth. This is particularly important if a company is implementing other safety technologies at the same time.
Turner notes that it’s very important for companies to have a “good understanding of where this solution [RTLS] fits in the broader scheme of things as well as in the digital transformation journey of a company.”
“And I will underline the word scalability because many companies don’t want to start big,” she adds. “A lot of our customers have big footprints, but they want to assess, they want to introduce technology, and they want to have internal business cases that will help them justify the investment and the benefits of applying technologies like this.”
Companies should sit down with potential vendor partners and discuss integration and scalability, as well as their critical needs and what capabilities need to come first. A company might have an ambitious project involving a remote operation center monitoring not only one site but enterprise locations hundreds or thousands of kilometers away. And that plan might involve a one-by-one roll-out or a much faster implementation. They want to ensure they have a partner that can “get them there,” Turner says.
Next Steps for RTLS
And when it comes to technology-driven digital transformations, Turner notes that her company’s RTLS hardware, software and services solutions certainly aren’t static and are regularly adding capabilities and refinement. For example, on the hardware side, she says her company’s RTLS runs on its OneWireless network, but the next step will be to incorporate LTE communications. The same holds true for the software and services side of the equation.
“We are constantly upgrading and changing the software to include new features and to be a priority in the market,” she says. “It’s the same as a car. Cars keep on changing. They might keep on running, but the difference between you having a car from 2019 versus a car from 2023 is significant. Similarly, with RTLS, having those additional layers of protections that really make a difference in terms of worker safety.”
This article originally appeared in the June 1, 2023 issue of Occupational Health & Safety.