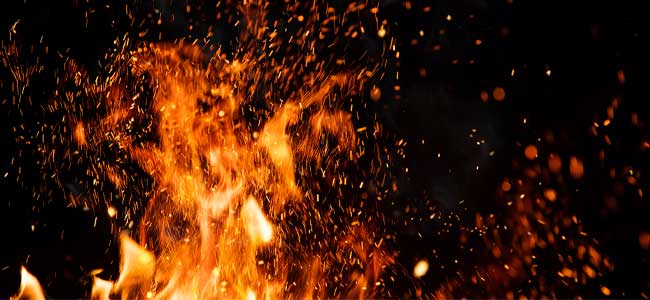
Changing Combustible Dust Requirements: 5 Ways to Comply
Combustible dust incidents have drawn OSHA and the NFPA’s attention. How can employers keep up with regulations and ensure worker and facility safety?
- By Michael Summers
- May 01, 2023
In the past six years, combustible dust incidents have caused an average of 31 explosions per year at manufacturing facilities in the U.S. and more than four times as many fires. Both OSHA and the National Fire Protection Association (NFPA) have set standards intended to prevent these incidents, but even so, accidents occur. As of January, OSHA added additional industries to its Combustible Dust National Emphasis Program, and NFPA announced it will consolidate its combustible dust standards into a new one, NFPA 660.
Here are five steps that manufacturers can implement immediately to keep up with changing combustible dust regulations for the protection of their employees, facilities and productivity.
1. Get your Dust Tested
Once you fully understand the nature of the dust your facility handles or generates—and assess the risk of dangerous incidents—you can set the proper cleaning procedures and select the best equipment to keep your people and facility safe. What’s more, in accordance with NFPA 652, this testing is required for all facilities that generate, handle or store dust. It’s your responsibility to have your dust tested, even if there is no history of incidents with that dust.
You can work with a private lab or OSHA to test and rate your dust for combustibility and classification. These tests are very detailed and should evaluate five main factors.
Dust Cloud Explosibility Parameters (Kst, Pmax). Together, these parameters quantify the severity of a dust explosion, how much pressure it will generate and how fast it will travel, even if there is no history of incidents with that dust.
Dust Cloud Ignition Limits (LOC, MEC). These two parameters predict the likelihood that a dust cloud will explode based on the concentration of oxygen and dust.
Minimum Auto-Ignition Temperature (MAIT). This is the lowest temperature at which a dust cloud will auto-ignite when exposed to hot air.
Minimum Ignition Energy (MIE). This test determines the smallest amount of ignition energy required to ignite a dust cloud.
Dust Layer Minimum Ignition Temperature (MIT). This is the minimum temperature required to ignite a dust layer on a hot surface.
For many companies, dust testing is new and creates many questions. Look for a qualified testing lab with not only the expertise to test the dust but also to analyze and explain the results. You will need this lab partner to provide the required compliance documentation.
2. Complete a Dust Hazard Analysis
If test results indicate your dust is not combustible—and you have the documentation to prove it—you can proceed with operations as normal. However, if your dust is combustible, you must then complete a dust hazard analysis (DHA), which is a complete review of your facility and your processes.
A DHA identifies potential risks and outlines plans to prevent, remove or mitigate those risks. Your DHA should group all locations in your facility into three general categories: not a hazard, maybe a hazard and deflagration hazard.
A complete dust hazard analysis should include a review of cleaning and maintenance procedures, the dust collection system and the process machinery that produces dust. This will help prioritize the management of the hazards, educate workers about those hazards and create safe, proper procedures for cleaning and manufacturing operations. A DHA should also provide the information needed to develop clear, thorough training programs for employees. A complete, step-by-step example of how to create a DHA can be found in Annex B. Chapter 7 of NFPA 652, which provides detailed descriptions and explanations of DHAs.
3. Implement an Effective Housekeeping Regimen
The right housekeeping regimen can keep dust from accumulating in the first place and prevent a secondary explosion hazard. You can use your completed DHA as a guide to define the safest cleaning procedures for each area of your facility based on the associated risks.
Proper, well-documented housekeeping procedures will help ensure that you comply with NFPA 654 guidelines and avoid OSHA penalties and fines. OSHA-recommended housekeeping procedures include, but are not limited to:
- Clean dust residues at regular intervals.
- Use cleaning methods that do not generate dust clouds if ignition sources are present (such as compressed air blow-down procedures).
- Use only industrial vacuum cleaners approved for dust collection.
- Regularly clean floors and horizontal surfaces, such as ducts, pipes, hoods, ledges and beams, to minimize dust accumulations within operating areas of the facility.
- Keep dust accumulation to less than 1/32 inch thick. (That’s the thickness of a paper clip!)
- Electrically powered cleaning devices used in dusty areas, such as sweepers or vacuum cleaners, must be approved for hazard classification.
4. Select the Right Equipment
OSHA and NFPA don’t just recommend how you should clean; they also dictate what kind of vacuum you should use. The NFPA does not approve or certify vacuums—certification can only come from a nationally recognized testing laboratory (NRTL) like Underwriters Laboratories or CSA. However, NFPA 654 does provide specifications for vacuums used to collect combustible dust:
- The vacuum features a noncombustible construction, except for the filter, and meets requirements for construction and static electrical hazard controls
- The vacuum uses conductive or static-dissipative hoses including both suction and air delivery hoses
- All conductive accessories, including wands and attachments, must be bonded and grounded
- Dusty air is not to pass through the fan or blower
- Electrical motors must not be in the dust-laden air stream unless listed for Class II, Division 1 locations
- No paper filter elements for liquid or wet collection
- Metal dust vacuums must be listed for Class II, Division 1, Group E environments and meet other NFPA 484 requirements for metals. Beware of imposters that claim to be explosion-proof but are not certified. Your best choice to keep your facility safe is to select a certified explosion-proof vacuum. NRTL certification information will be stamped on the vacuum’s nameplate. Remember, if your manufacturing environment is certified, your choice is clear. You must select a vacuum certified for that environment.
5. Get a Site Assessment
A site assessment conducted by vacuum specialists will help you make the right decisions.
Some vacuum suppliers will offer a site assessment as part of the sales process. If so, you should take advantage of it. Effective site assessments include:
Brief walkthrough. Identify where various cleaning methods or equipment could help you prevent safety hazards and remain in compliance with regulatory standards.
Identification of hazards. Rely on the expertise of your vendor partner to identify any areas of noncompliance you might not be aware of so that you can address them in your DHA and cleaning plan.
Series of questions. This is the time for your vendor partner to ask the right questions to fully understand how to help you. If they aren’t asking a lot of questions, beware.
Equipment recommendations. Recommendations should be tailored to your needs and ensure that you have the right power supply, airline diameter and pressure, etc. to support the equipment you want.
Product demonstrations. Make sure to take full advantage of this opportunity for your staff to “test drive” the equipment at your facility. Demos are critical to your selection.
Conclusion
There is a lot to consider when it comes to properly identifying hazards in manufacturing facilities and selecting the right equipment to help mitigate those risks. All the above steps can be initiated right away to reduce the risk of dangerous incidents at your facility and help you stay compliant with combustible dust requirements.
This article originally appeared in the April/May 2023 issue of Occupational Health & Safety.