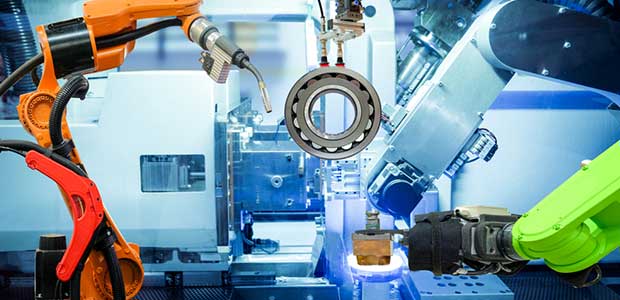
Reflections on Safety in the Robot-Built Environment
Poor safety performance can result in substantial loss and unanticipated and detrimental risk, both acute and chronic, to project stakeholders.
- By William Mueller
- Mar 09, 2022
Safety is a top priority in today’s workplace, but that has not always been the case. While occupational safety existed long before the Occupational Safety and Health Administration (OSHA), it was often poorly defined and limited in scale. In the U.S., pioneering trade unions, public advocates, and government officials demanded safer working conditions for years, but until 1970 with the creation of OSHA, no Federal legislation existed to cover occupational safety throughout the country.
Even with legislation that has been bolstered over the years, the construction industry remains extremely dangerous. With so many workers, hazardous activities, and heavy equipment moving around a rapidly changing environment, actively providing for safety on construction projects remains as challenging as it is necessary. Poor safety performance can result in substantial loss and unanticipated and detrimental risk, both acute and chronic, to project stakeholders. Such losses may include injury events that result in penalties and oversight by Federal and state agencies, schedule interruptions, loss of materials, and tragic loss of life. Chronic impacts may include civil litigation, increased cost of insurance, and a reduced ability to compete in a market where safety performance continues to be closely scrutinized. Poor safety performance can also be detrimental to employee morale, impacting everything from quality workmanship to employee attendance and retention.
Thus, for owners in the construction industry, there is a great need to continually assess and mitigate safety risk. As such, any aid in the execution of that mission is welcome to project stakeholders. In addition to the practice of safety professionals and stronger legislation, improved technology offers promising new means of delivering our built environment safely.
The Expanding Horizon
So what safety technologies are on the horizon in the construction industry? What recognized hazards can they get rid of? And how can we safely use the technology?
Some technology literally takes the place of humans who would otherwise be engaged in hazardous or strenuous activity. Drones, for example, can inspect elevated and hazardous work locations, thereby eliminating the risk associated with such a work task. The Semi-Automated Mason (SAM) by Construction Robotics is designed reduce the physical demands that come with masonry.
Other technology is enabled by the internet of things (IoT). For example, Wireless Sensor Networks (WSN) enable objects and devices to sense, map, and communicate environmental conditions in real-time. WSN can be incorporated into the job site or even worn by employees. Smartphones and portable tablets allow for easy monitoring and transmission of collected data to employees and managers alike. This allows for easy alert systems and constant monitoring for dangerous conditions. In addition, Building Information Modeling (BIM) can utilize WSN technology to create digital models that provide visualizations of the built environment throughout the construction lifecycle for enhanced safety management. BIM, WSN, and other technologies paired with virtual reality applications create the safest access to hard-to-reach or dangerous locations on a construction site.
Most exciting and promising for safety outcomes, perhaps, are innovative uses of artificial intelligence (AI) within robotic equipment to safely execute repetitive and dangerous tasks on construction sites. These technologies can reduce or eliminate long-term health impacts on workers arising from heavy lifting, repetitive motion, and other strenuous laborious tasks that commonly lead to injury. The benefits of such ingenuity within the construction industry are only anticipated to increase as technology advances. While the initial investment associated with planning and implementing robotic technology is high, the return on investment is instantaneous. AI can increase efficiency and productivity with minimal loss by reducing the number of man-hours needed to execute certain tasks and working non-stop for hours or even days at a time. As AI becomes even more advanced and more economical, owners will be able to deliver projects on time, within budget, and safely with much more consistency.
Changing Roles & Increased Responsibility
There will likely come a time when most, if not all, construction will be executed solely by robots. However, this will follow a long period of construction executed by both humans and machines.
As autonomously moving equipment, robots represent a new hazard on construction sites. They may be heavy, and their operation may be complex. They will likely require the use of special platforms from which to operate with precision. They may have features, actions, or triggers that are unknown to those working around them, and they may move in ways unsuitable for certain environments. Robots may have their own safeguards, such as sensors that halt activity if an unexpected object (like a hand) comes into the machine’s proximity, if the robot gets too close to some boundary (like an electric fence or laser), or if the machine’s grade exceeds a certain angle. However, those safeguards may not always be present—a moving robot would be a major fall hazard if used on scaffolding or elevated floors of a building without appropriately demarcated edges, for example. Therefore, robots will require appropriate installation, oversight, and maintenance, as well as regular inspections to ensure they are working as specified in the appropriate environment. Likewise, employees will require training to operate robots and work safely in their proximity. If used improperly, robots may add more hazards to construction than they remove.
For example, the SAM contains a multidirectional robotic arm that primarily moves side to side and up and down. The entire mechanism moves on rail system set on a work platform. An adjacent worker must program the robot and fully understand how the robot and its appendages move, as well as how others can safely execute their own work around the robot. The robot itself will require installation, as well as bricks and mortar. It may also have to be moved manually as its work is completed. Set-up will require a professional that understands the full potential and limitations of the robot, such as its ability to detect an unprotected opening onto a lower floor. Material delivery and human movement of the robot are opportunities for human-machine encounters and potential safety hazards. Someone replenishing the robot’s mortar supply, for example, must ensure the robot is de-energized, properly isolated, and will not suddenly start work during their task.
In addition to the potential dangers of human encounters with robots, humans will still have to enter hazardous locations where the machines are working. Those encounters include windows of time, in which those responsible for the operation of robots are exposed to fall hazards, electrical hazards, loud noises, and all other familiar construction site hazards. Even though robots reduce worker exposure to these hazards, the hazards do not cease to exist. As AI and robots become more integral to construction, I expect project personnel will need a more sophisticated approach to safety. To develop an understanding of the full potential and limitations of all new technology as it pertains to construction safety, as well as to create conditions for the safe implementation of new technology, safety professionals will still be in high demand. Our roles will simply have to evolve alongside changing construction conditions.
My colleagues in safety will have to add to our existing body of knowledge with continued research, data collection, and analysis. The education of safety professionals will have to change, as tech literacy becomes more important for our profession. We will have to develop an appropriate understanding of all different types of robots being used, as we have for all the machines and tools in current use. We will have to experiment and develop appropriate policies and training for use of the robots. We will certainly have to consider what new hazards will be created for those working with or near robots. We’ll also have to devise ways of preventing injuries stemming therefrom. Much of this information will come from the equipment manufacturer, like any product, but much of it will have to be acquired through real-world usage of the equipment. We will have to conduct on-site inspections to understand changing site conditions—even where the monitoring done by construction managers is able to be done via machine. Most importantly, safety professionals will have to continue cultivating appropriate attitudes towards remaining and new dangers on construction project sites, lest through laxity or overconfidence, avoidable accidents happen.
Final Thoughts
As we evaluate safety in the construction industry’s robotic age, we must understand it took pioneers in the workplace, the public, and government hundreds of years to create the safer conditions we have today. While no one thinks we’ll need centuries to address occupational safety and health in the robotic age, we know it will take pioneers to lead the charge.
Despite these considerations, I am very optimistic. The expertise and foresight of safety professionals combined with the potential of new technology promises safer construction projects than ever before. That means better project performance, fewer workplace injuries, and less tragic loss of life. I’ve personally witnessed numerous innovations in technology in my career and believe we continue to blossom with ideas and innovations that will continue to benefit the construction industry. Safety professionals and project teams need only stay vigilant to make the most of the exciting new developments on the horizon.