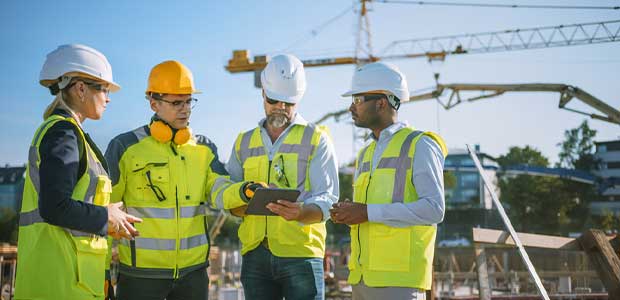
Issues with the Quality of Construction Operational Systems and Their Affect on Project Outcomes
- By Peter Furst
- Aug 16, 2021
Introduction
The built environment (structures) as produced by the construction industry greatly affects the economy, society and the environment, it influences, to some degree, defining the quality of our daily work-lives. The built environment directly or indirectly is a major contributor to global warming, air, water and land pollution and waste generation, to name a few. Some of the problems with this industry is the fact that it involves multiple stakeholders with diverse interests, there is high industry fragmentation, high levels of competition (low bid preference) with low profitability, propensity for risk transfer, one-of-a-kind- projects, unstable workforce, etc. Construction lags behind many of the other industries in the adoption of innovation and technology, which leads to improved productivity, lower cost and safer projects.
At the operational level, by virtue of the contracts that a general contractor (GC) or construction managers (CM) sign, they take on the obligation of completing the project at the agreed upon time, the specified level of quality and within the stated price. To that end, the GC or CM must assign capable, knowledgeable and motivated staff to oversee the construction activity on site. They must also ensure that they engage reputable organizations along the supply chain capable of operating cooperatively, efficiently as well as effectively in order to meet the project’s contractual obligations. This means that every partner (subcontractor) and vendor (supplier) along the supply chains must have processes, practices and procedures as well as people who are able to produce the required output within the stated requirements.
Background
The question is how does the owner of the project ensure that he/she hires the most capable and competent organization to build his/her project. The primary method of selecting a contractor to build the project is by competitive bidding with some through negotiations. To that end, the owner must establish some criteria upon which to base the selection. The primary ones may include such things as the proposed cost and the length of time to complete the project.
Some owners may have other additional criteria such as reputation, year is business, capable staff, etc. to name a few. The owner may also have a number of different firms to compete for the project in order to ensure that they get the best possible combination of cost and time. The owner then selects the most responsive bid and awards the contract. It is also a fact that the construction company is only as good as its staff (capability, experience, motivation) that it assigns to manage the project.
Productivity Issues
Compared to many other industries, construction invests little in research geared towards improvement initiatives. In many cases, this was 20 times less than some and significantly below that of manufacturing. Such underinvesting reduced the potential for research fostered innovations in potentially improved productivity, greater operational efficiency and smoother flow This creates structures that are more affordable and easier, faster and more life-cycle cost effective to build, operate and maintain. Similarly making construction workers more productive, safer and satisfied.
A long-term study by the Bureau of Labor Statistics with data spanning from 1964 to 2003 on productivity in construction compared to other industries excluding farming, found that it significantly fared worse than the others. The study measured constant contract dollars of new construction work per field work hour. The study found construction averaged a downward trend in productivity of about -0.6 percent per year, over the forty-year period. That represent an almost 25 percent decrease in productivity in that time frame. Conversely the study found that the other industries’ productivity, on average, trended upwards at a positive rate of 1.8 percent per year over the forty-year period which evolved to a 72 percent improvement throughout that period. The spread between the two equals almost 100 percent!
A study done a while back by the National Institute of Standards and Technology (NIST) found that 57 percent of project cost resulted in no value created for the construction project owners.
A study by The Construction Industry Institute (CII) found that only 43 percent of time spent on construction activities were considered productive and creating value for project owners. Another CII study found that more than 10 percent of project cost was attributable to rework. A number of studies attributes much of the situation faced by the construction industry to fragmentation. This invariably results in the following:
• Fragmentation increases complexity
• Complexity increases uncertainty
• Uncertainty increases variability
• Variability increases risk
• Increased risk leads to greater likelihood of discrepancies, disruption, disputes or damages which lead to both short and long-term problems for all involved!
Much of what was discussed above has caused construction projects to utilize significantly more work hours per constant dollar of contract. This will cause the project to cost more and take longer to complete. So, in order to reduce time, the contractor will have to either use more men or speed the process up. This, to some extent, will increase risk leading to possibly inferior quality or more worker accidents resulting in owner dissatisfaction. In one way or another, all of this affects project time and cost and is reflected in just about every important construction management metric in the area of production, productivity, quality, safety, as well as partner satisfaction, impacting relationships as well as the bottom line. It is important to note that any level of improvement of the operational systems will, in fact, to some extent, improve many, if not all of the other project outcomes.
All of this highlights the need for a massively significant change in project delivery, as well as organizational systems (policies, processes, practices, procedures). The problem is that this would be disruptive to the ongoing operation and have serious financial consequences. The best way to approach this is to find the areas that need change, evaluate the importance to improvement, devise a strategy, secure employee buy-in, deploy change initiative, monitor improvement and make any necessary changes to ensure success.
Resistance to Change
While some say that the only constant in business is change, it affects people in many ways which often results in some form of resistance. This may manifest in fairly subtle ways, such as avoidance or passive aggressive behavior, to outright defiance, hostility and even possibly sabotage. The best way to avoid resistance to change is to convince people of its necessity as well as its many benefits to the organization in general and, more importantly, to the employees in particular.
Even if the proposed change will not greatly impact the employees, they may perceive that it will. Therefore, prior to deploying the change, initiative management must carefully envision the possible impact real or perceived may have on the employees by analyzing the following elements:
-
Specific changes sure to cause concern are the ones involving restructuring or consolidation, as these may lead to reduction in the workforce.
- Which employees may be impacted: depends on the type of change and may impact a team, a project, a specific department or the company as a whole?
- How it will or may impact employees: obviously the biggest impact involves lay-offs. Any job involving significant change may be a close second. Some employee’s jobs may be restructured due to someone else being laid-off. Such changes may emotionally impact people who will lose coworkers or friends, even if the change does not directly impact them.
After the analysis of the three elements above, management should be able to anticipate the reason for and the nature of the employees’ reactions and the potential backlash(es). It should be able to devise a deployment strategy directed towards dispelling many of the reasons for the employees’ reaction to the upcoming change initiative. Management should also provide the support, knowledge, information and skills employees will need, during and following the change in order to successfully navigate the process.
Conclusion
With managing the process of change well for both the organization for one’s team and the inevitable part of working life, this has become a core competency for managers. However, for many employees, change means uncertainty, anxiety or stress from the perception of the loss of control. If you can identify why specific individuals in your team may be worried, then you can be proactive in your mitigation approach.
The most effective way to combat this is through open, two-way communication, empathically listening to concerns, encouraging employee involvement and participation in the process. Provide clear and compelling reasons for the need for the change with the concrete benefits accruing to the organization and, more importantly, the ultimate benefits to the employees from the resulting changes.