An Agile Framework for Occupational Health Mitigation
Occupational hazards require continuous assessment and evaluation to ensure the sustainment of zero hazard occurrences.
- By Saso Krstovski
- Aug 02, 2021
Occupational health is a critical aspect of any industry. Organizations understand the impact and significance of the elimination of any hazards for the workforce. Occupational hazards require continuous assessment and evaluation to ensure the sustainment of zero hazard occurrences. The first step is a categorization of the occupational hazard. Two categorical approaches for hazard mitigation are reactive and proactive. Reactive is a result of an incident occurrence. Proactive is driven based on indicators signaling potential and preventive measures that are developed to mitigate future failures. A severity assessment guides solution strategy based on process, design or blended actions. The final phase in the framework requires a thorough evaluation of potential replication in other areas within the organization.
Hazard Categorization
Concern resolution is categorized as reactive or proactive. Reactive is after the fact requiring the team to work backward from the actual incident to understand the root cause. Proactive requires anticipation of concern potential. A visionary approach challenges teams to think differently at potential hazards. Both approaches are vital for occupational health management.
Reactive Approach. A reactive approach is critical in the management of hazard incidents. Every incident requires immediate remediation to prevent further incidents. Based on the severity of hazard mitigation, efforts range from process changes to complete redesign of the process. The natural human instinct for reactive measurements drives quick actions. This drives concentrated effort on particular concerns and prevents a holistic view of the complete system. These actions could impose additional risks in the process--occupation health mitigation efforts for reactive concerns.
Proactive Approach. Proactive approaches are derived from the three “R”s reports, recognition and replication.
Reporting encompasses teams analyzing current data collection methods for hazard activities. The process requires significant efforts to not only research data but also confirm accuracy and consistency in reporting. A structured approach utilizing PDCA or six sigma DMAIC problem-solving methodology is necessary to facilitate hazard concern identification and resolution. Pareto analysis of the highest functional area, procedural task or hazard condition is the first step in determining focus efforts. Recognition requires having an “eye for safety.” Hazard conditions are observed during regular activity. Recognizing hazards afford teams to formulate a temporary mitigation plan and focus on a robust permanent corrective action. This mechanism requires individuals to train themselves to have an “eye for safety.” Individuals assess every potential scene on how activities or tasks can generate a hazard condition. Enhancement of sensory skills and innovative thinking mindset is vital to discover potential concerns based on the current state. This requires a unique personal ability and requires continuous out of the box thinking.
Replication involves finding best practices implemented elsewhere and incorporating them internally. Research and assessment have already been conducted; therefore, implementation effort is minimal. This is analogous to “low hanging fruit.” The effort to pick low fruit is significantly less than ones higher in the tree. This proactive approach is greatly overlooked. Implementation is simple to perform and value is significant. Organizations lack prioritization of this proactive approach.
Replication vetting is critical after any hazard mitigation effort. Every solution strategy implemented reactive or proactive must be assess for replication internally or externally. The step-in hazard mitigation is critical to achieve avoidance and sustainment.
Hazard Severity
Assessment of hazard severity level formulates the resolution strategy type. The severity level is determined based on frequency, probability and hazard type. Figure 1 displays the criteria for the classification of each level.
Table I shows a matrix for severity level determination. High severity hazards require complex robust solutions. Low severity can be managed and controlled with minor modification to process or task.
All occupation hazards must be addressed with solutions strategies that eliminate concern and ensure no additional compromises are generated in process or task.
Solution Strategy
Hazard severity level outlines solution strategy type. Figure 2 shows the roadmap for resolution strategy based on hazard level rating. This roadmap outlines a recommendation of a strategy that provides the most significant potential for a robust solution. Low severity levels require modification in the current process to eliminate hazard condition. Hazard levels of medium and high need a design or blended approach to resolving.
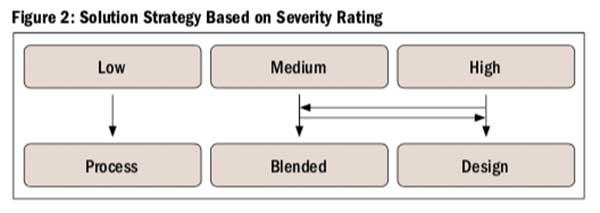
Design requires a thorough review of the process or task. Analysis centers on designing out the hazard. Solutions generated require a philosophical change. Process changes are structural and implemented relatively quickly. A blended approach involves modification of design and changes within the process or task to accomplish the requirement.
Scenario Investigation
Engaging the above framework for a typical occupational hazard condition highlights the process roadmap and tollgate outcomes to support agile solution strategy. Any categorical hazard condition assessment can embrace the framework. A consistent hazard challenge for the majority of industries is slip and trip. This occupational safety concern is a constant metric impacting top priority concerns for safety professions.
Reactive. On any particular day, an employee or customer can encounter a slip within the organization's facility. A report is submitted and immediately the safety team responds. The first action requires activities to isolate any additional cases. Next, teams review and determine the impact of severity. This would be a LOW impact and requires modification to the process. Performing a traditional 5-Whys for root cause determination is a leaking water cooler. Actions implemented a preventive maintenance schedule for water cooler assessment at a particular frequency to ensure no leaks.
Proactive. Proactive activities are desired for any concern. Proactive actions allow to prevent occurrences and afford the team more time to diagnose and develop a robust solution. There are three Key Process Input (KPI) for uncovering hazard condition proactively: reporting, recognition and replication. Each avenue contributes equally to the successful mitigation of potential hazard conditions.
- Reporting. Reporting involves a review of current data collected based on incidents. Teams review and uncover critical areas, operations or tasks to address based on historical analysis. Figure 3 displays a year-by-year hazard metric data for a manufacturing location. Visual office visits, arm and leg occurrences are not statistically different. Body metric indicates a dramatic shift in 2020. The team needs to further dissect data for body metrics and understand indicators driving higher incidents.
Figure 3: Yearly Safety Metrics
Recognition.
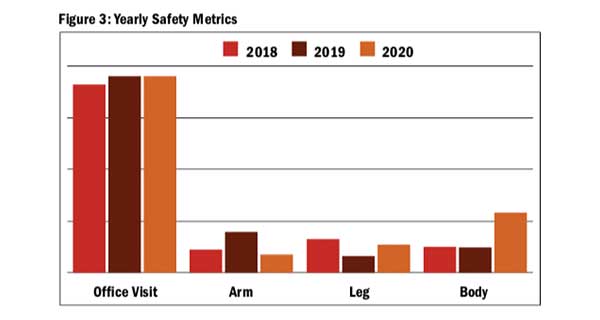
- Recognition. is an act of discovering potential hazards during daily activities. A health and safety-conscious employee walking during lunch notice an abnormal floor surface. Escalating concern to facilities department it was discovered a slow leak from above piping. Quickly area was quarantined off to prevent access. Piping was repaired. Further, a periodic schedule was implemented to assess all potential piping under walking surfaces.
- Replication. Replication is a concept of implementation of solutions from other departments or organizations. A safety professional receives an email from a colleague about a concern involving a trip hazard. An employee tripped over a hose from a hydraulic truck laying across a walkway to tap off the fluid in a piece of equipment. The team discovered this was a one-off condition and the process is used throughout their facility. During problem-solving, the team uncovered the hose blended with the flooring and it wasn't easy to see. Seeking a low cost-effective solution, the team decided to modify the hose used in the hydraulic truck to a florescent color to increase visibility. After reviewing the solution, the strategy safety profession assessment facility discovered a location that has significant usage of hoses for equipment repairs. Leveraging knowledge from other facilities, the team replicated a similar approach to the minimized potential for trips.
Conclusion
This publication outlines an agile framework to mitigate the occupational hazard. Following the roadmap supports quick, robust solutions to concerns. Both approaches reactive and proactive are necessary to ensure safety in the workforce. Organizations need to increase resources to focus on proactive methodologies to minimized reactive activities. Occupational hazards require continuous assessment and evaluation to ensure the sustainment of zero hazard occurrences.
This article originally appeared in the July/August 2021 issue of Occupational Health & Safety.