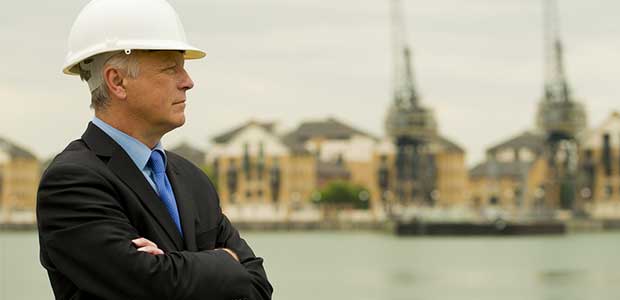
Management Commitment is Crucial to Environmental Health and Safety Programs
Management Commitment pertains to high level leadership’s “direct participation” in an organization’s EHS program.
- By Russell Carr
- Dec 01, 2020
What is management commitment, and why is it absolutely critical to the success of any environmental health and safety program?
It’s a very broad and important topic that can’t be fully addressed in this article, but we’ll take a summary look at key issues including a working definition, positive and negative indicators, prevalence and underlying drivers. Most importantly, we will examine the critical role that management commitment plays in the long-term success or failure of any environmental, health and safety program.
So, if you value the success of your EHS program and are unsure about this issue, then please read on.
Working Definition of Management Commitment
Let’s begin with this simple yet effective definition from a company called IGI Global: “Management commitment is direct participation by the highest-level executives in a specific and critically important aspect or program of an organization.”
For the purpose of this article, it pertains to high level leadership’s “direct participation” in an organization’s EHS program, which we can all assume is a “critically important program.”
In reality, all company stakeholders should be involved and committed to the EHS process, but as the definition suggests, it all needs to start at the top. And by the top, I’m referring to ownership, especially at a small company. It could also be the CEO, COO or President of a medium or large company.
This is critically important because these are the people who are ultimately responsible for EHS issues at any given company, not only from a practical standpoint but also from a legal standpoint. They only ones who can “write the check” and ultimately approve the entire process.
So, from this perspective, if you don’t have their commitment and involvement, it puts the entire process at risk.
Why Is Management So Critical to EHS Success?
Now that we have a basic understanding of the term, let’s talk about why it’s so critical to the long-term success of an EHS program.
The short answer is pretty simple—it’s the fact that managing EHS compliance, especially over the long term, isn’t easy. In fact, it’s often very difficult. In a nutshell, it’s inconvenient, costly and disruptive to business operations.
Here are some quick examples to illustrate the point:
- You must make time for employee training, which means pulling employees off the production line, which then ads payroll costs and can disrupt production schedules. To complicate matters, training is a never-ending process.
- You must routinely and consistently enforce your safety program, which means supervisors must continually monitor employees and hold them accountable when they don’t follow rules, like not using PPE for example. And for those who refuse to comply, you might actually have to fire and replace them.
- You must conduct routine inspections to identify and correct safety and environmental hazards, which can be expensive and disruptive in all kinds of ways.
And the point is, despite all of these and many other challenges associated with managing your EHS program, company leadership must maintain a consistent and unwavering commitment to the cause. Otherwise, cracks will begin to form and pretty soon everything falls apart.
Warning Signs That Your Company Lacks Management Commitment
How can you tell if your program is in trouble due to lack of management commitment?
It often starts with little things, like delaying or cancelling planned inspections or training sessions, or allowing known safety hazards to persist over time without correction.
Other examples include:
- Your company safety committee meeting schedule gets changed from bi-weekly to bi-monthly, or less frequently.
- The draft copy of your new safety plan was submitted for review and comments, yet has been ignored for weeks.
- When accidents or injuries occur, there are no follow up investigations to determine root cause and make recommended corrective actions.
- Your assigned safety or EHS manager is routinely ignored when he or she brings issues to the table.
These situations would never exist or be tolerated in a company with strong management commitment, and are actually symptoms of a dying EHS program. So, if any of this sounds familiar, beware.
Signs of Strong Management Commitment
Now let’s flip the script and talk about what strong management commitment looks like. And by the way, the examples I’m about to share are typical at large organizations who often fully support EHS.
In these cases, company leadership routinely:
- Includes strong EHS support messaging in company memos, speeches and other communications.
- Includes key safety metrics such as TRIR, DART and EMR alongside other financial and quality KPI reporting
- Gets involved in all accident and injury investigations and approves corrective actions.
- Sets positive examples by consistently wearing PPE, such as safety glasses, when walking through work areas.
- Gives front line workers the authority to stop work when they identify/recognize unsafe conditions.
Notice that in most of these examples, senior leadership is actually participating in the process, as opposed to just offering lip service.
And to the point of this article, if you’re not recognizing any of these indicators at your company, it’s yet another reason to be concerned.
How Common Is Management Commitment?
Now that we have a better idea of what management commitment is and is not, it’s worth asking how commonly it’s practiced at U.S. companies.
Unfortunately, the truth is that strong and consistent management commitment when it comes to EHS support is relatively rare.
As indicated earlier, it’s much more common at large companies, much less prevalent at medium sized businesses and even less so at small businesses. I’ll explain why this is so below, but it’s also important to recognize that larger companies often have the resources needed to fully support EHS, which smaller companies often lack.
The answer also depends on industry, with manufacturing, construction and energy being at the top of the list for strong management commitment, largely due to overall risk exposure, value and visibility issues.
What Drives Management Commitment?
When trying to understand the underlying drivers and motivations for establishing and maintaining strong management commitment, we begin to get to the crux of the matter and why it’s so important.
As you’ll see, drivers are often very different depending on the size of the organization.
Large Businesses: > 1000 employees
Let’s begin by discussing drivers at large companies where management commitment is often strong and prevalent.
Primary drivers and motivations include:
Protection from harm. Large organizations understand that their employees are their greatest asset and that they have a fundamental duty to protect them from potential work-related harm. The same goes for protecting their local communities and the environment. In other words, they fully understand these risks and the company’s duty to take preventative action in the form of EHS programs.
Exposure & Risk. Large organizations typically have major exposures in all areas of EHS, and therefore have little choice but to give strong support to programs which function to reduce their overall risk profile. The bigger the company, the more complex their operations. The more locations, the more employees, the greater the exposure and therefore the greater the need for management commitment to mitigate overall risk.
Culture. Given these duty, exposure and risk issues, large companies clearly understand the value proposition behind EHS programs. As a result, their company culture reflects this by instilling these values within the organization from top to bottom. In other words, EHS is baked into the culture, company leadership gets indoctrinated into that culture and then naturally assume their supporting role.
Education. I believe it’s fair to say that education plays a key role. In other words, most senior executives at large companies are college and/or management educated, which often includes training and curriculum on the importance of managing environmental, health and safety compliance and risk management.
Small to Medium Sized Businesses: 1 -999 employees
For the purposes of this discussion, we’ll combine small and medium sized businesses.
Here are common drivers:
- Response to a specific negative event, such as a failed OSHA or EPA inspection, serious injury, fatality, environmental cleanup or some other damaging or costly incident resulting from a lack of EHS compliance efforts. Unfortunately, management commitment only arises in reaction to a negative event which ends up causing serious financial, reputational or even emotional distress for the business and/or leadership. This is probably the #1 driver for smaller companies.
- Customer or industry driven requirements. Often times, especially as a company grows, small to medium sized businesses are eventually confronted with customer or industry driven requirements including having to develop an EHS program, reduce high injury rates or implement ISO EHS management systems. In other words, either the company meets these customer or industry requirements, or faces losing major business opportunities.
- Increased Workers Compensation premiums. High injury rates can result in up to three times higher premiums which can be devastating to a company, and often result in management commitment towards injury rate reduction and safety performance improvements.
Although these are common management commitment drivers for smaller companies, they often don’t result in long-term, consistent results since they’re all reactionary, rather than being focused on core EHS values.
In other words, the core value proposition or goal behind any EHS program should be to protect the company’s employees, local community and the environment from potential harm caused by company operations. Whereas large companies often understand this obligation, smaller companies often don’t.
I’m not suggesting that smaller companies don’t care about these issues, but in my experience, most don’t fully recognize and respect the life and death risks that their operations pose to their employees, etc. Many of these business executives often don’t really believe that it could ever happen to them. This lack of respect, awareness and understanding is arguably the biggest reason that management commitment is so rare and unsustainable at smaller companies.
Summary
Hopefully this article has succeeded in explaining the critical role that management commitment plays in the success or failure of an EHS program and helped you determine whether or not it exists at your company.
If management commitment is lacking at your company, I strongly recommend that your company leadership seek resources to help educate and build awareness surrounding EHS regulations and laws, as well as the many benefits that companies can achieve by committing to implement and support their EHS programs.
This article originally appeared in the November/December 2020 issue of Occupational Health & Safety.