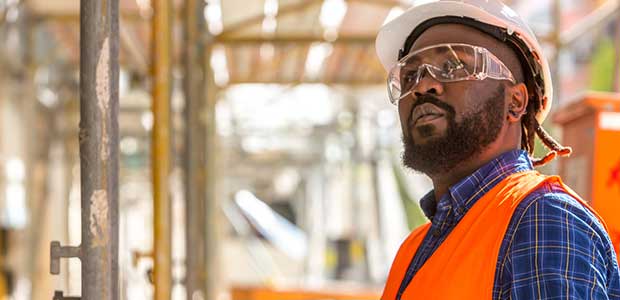
EHS Compliance: Make It Personal
Safety professionals are the bridge between those worlds—corporate safety/compliance programs and the frontline work. Therefore, it’s imperative that your health and safety programs meet your workers where they’re at.
- By Kraig Haberer
- Oct 01, 2020
Environmental Health and Safety (EHS) work doesn’t always happen in the office; in most cases it happens in the field. So, how are EHS professionals keeping up with their dual obligations to keep workers safe on the job and their company in compliance? As health and safety professionals, you have vast health and safety programs that may span multiple divisions, locations and work functions across hundreds, if not thousands, of employees. To deploy the most effective health and safety program, tailoring the requirements to the situation and needs of each employee enables you to shrink the global requirements to each worker in a “just in time” and “just as needed” scenario.
As the title suggests, making safety personal means two things: 1) first, putting relevant and personalized data, content and safety solutions directly in the hands of your field personnel, but also 2) taking advantage of technology solutions to operate better in the field with better feedback, better functions, and better action.
The real moments of incident prevention and response happen with workers themselves, wherever that work might take place. Safety professionals are the bridge between those worlds—corporate safety/compliance programs and the frontline work. Therefore, it’s imperative that your health and safety programs meet your workers where they’re at. In this article, I’ll talk about the opportunities and benefits of cascading safety initiatives down to each employee and how to make health and safety personal for each employee based on their unique locations, functions and needs.
Personalized Safety: What’s in It for Me?
Personalized health and safety programs benefit employees, managers and businesses as a whole. At the employee level, they help workers organize their day and save valuable administrative time. Utilizing mobile-friendly safety management software allows employees to stay in the field where they can be most productive. Imagine an employee safety dashboard that organizes each worker’s activities, training requirements, safety documents and location-specific or role-specific job hazards. Furthermore, personalized health and safety programs specific to workers and roles allow for faster onboarding when specific training resources and relevant job information are right at their fingertips.
For safety managers, personalized programs create a proactive health and safety culture. With collaborative tools and content in the field, managers can push information to the field in advance and respond quicker when there is an issue. It enables managers to capture feedback immediately and maintain a hand on the pulse of your organization. Additionally, incident tracking, hazard management, observations and corrective actions are all contextualized down to the individual worker, thus enabling teams to pinpoint specific areas to address.
Finally, corporations and executives benefit because health and safety technology in the field delivers leading indicators via data-gathering mechanisms that give businesses early insights into what is happening in the field. These leading indicators help identify potential issues before they become an issue, raise the profile of safety and boosts employee engagement.
So, what are the best areas to make safety and EHS compliance personal? I’ll discuss several, including safety training, hazard prevention and personalized safety dashboards.
Like Having a Safety Expert in Your Pocket
The best form of training is training that is relevant, specific, timely and available in the right context. If we think of personalized safety programs as on-demand EHS compliance, we can think of personalized training as “Knowledge on Demand.” Training typically happens in an episodic, non-contextual manner through an online or in-person class. However, a smarter approach is to supplement your general workforce training with specific safety and skills training that’s immediately available in the field at the right time and for the right purpose.
This in-the-field training may include shorter, more specific, topic-focused training that relates to a particular safety issue or situation applicable to that location, employee role or existing hazard in the work area. For example, workers can watch a 60- to 90-second video on a real-time safety issue like fire safety, lockout/tagout, CPR, first aid or hundreds of other relevant topics via a mobile app before the employee enters the risk area.
The benefits of in-the-field training include many. Employees benefit from the convenience of anywhere, anytime training. It cuts down on lost time and administrative hurdles to execute training vs. traditional onsite or even web-only training in a designated training center. Concurrently, employers benefit from higher rates of completion and mastery when training is made more readily accessible and is relevant to a specific task or job requirement. Ultimately, this results in lower costs for the organization: lower training costs, less lost time and higher competency, which results in fewer health and safety issues.
Heads Up!
What all EHS professionals strive for is a workforce focused on prevention rather than reaction. This is where safety programs tailored to the individual shine. Safety managers generally know the locations within facilities, the employees within those locations and the potential risks and hazards in those particular locations. For example, a company that keeps lists of chemical inventory by location should be able to predict and prepare employees for the types of chemical hazards they may face, wherever they are in the building. Additionally, if a company has completed audits, inspections and observations, the company should be aware of potential physical and health hazards that exist and supply the workers in those areas with the right suggestions for personal protective equipment and training right on the spot. This allows employers to connect the dots between risks/exposures, safety training and other preventive measures, as well as protect lives.
While this may sound daunting to set up and track, safety management software can help. A safety and compliance management system will track your employees, locations, risks, safety programs, training content and more, all in one system. This helps companies train, track and report on safe working conditions and enable proactive employee engagement to promote an active safety culture. Some examples of its benefits include might be:
- A worker submits a hazard via an incident workflow and the system deploys real-time content and training to the employee based on the hazard type
- An employee is assigned to a new location or role. The system auto-enrolls the employee into specific training based on that role or location
- Tags used to identify employees with special designations such as “fire safety” or “incident response” which the software can then use in workflow and automations triggered on specific events, incidents or training so that action items are pushed based on context and group identification
Finally, this doesn’t have to be expensive. Today’s modern safety management and compliance systems can be easily configured to meet your exact business needs, tailored to your employees and specific to the way employees work. An important note: look for configurable systems, not customizable ones. Configuring tailors existing functionality to your needs. Customizing involves expensive professional services to set up your specific environment.
Just the Facts, Please
Dashboarding is often a concept only discussed in management scenarios where managers and executives synthesize incoming data into a few key performance measures. However, dashboards specific to employees and roles are a significant opportunity to personalize health and safety initiatives. Personalized safety dashboards hide anything that isn’t relevant to a worker. This dramatically reduces unnecessary ‘noise’ and confusion. Safety dashboards organizes workers’ upcoming, current and overdue actions in one place, all at a glance with personal reminders and notifications.
Here’s an example of pulling employee safety management all together in a personal safety portal. In this example, you can see that the employee has access to the key safety knowledge and tools specific to their work. In the main pane of this dashboard, you see the training classes and tasks that have been assigned. As you can see, the training view outlines what is completed and what is still outstanding. Furthermore, the specified training can be launched directly from the mobile device. This really expedites the training process. This is good for the employee and good for the employer.
Additionally, the dashboard displays personalized content for:
- Chemical hazards and safety – direct access to the safety data sheets in the area, outlining the chemicals in the location, the risks and hazards of those materials and protective measures that the employee might want to take.
- Safety documents – access to key safety, operating or company information such as SOPs, building maps, and location or role-specific knowledge requirements.
- Incident management – allows for submission of incidents or injuries, with pre-populated input of employee name, role and location in the form.
Paul O’Neill, former Chairman and CEO of Alcoa, once said, “never budget the cost of keeping humans safe.” Not that cost isn’t a factor; however, we can work smartly by finding ways to tailor health and safety programs directly to our employees and make safety personal. Look for ways to deliver that personal safety portal for each employee so that they have the specific safety information they need based on their job, their location and the hazards surrounding them. Workers’ lives and livelihoods are dependent on making safety personal.
This article originally appeared in the October 2020 issue of Occupational Health & Safety.