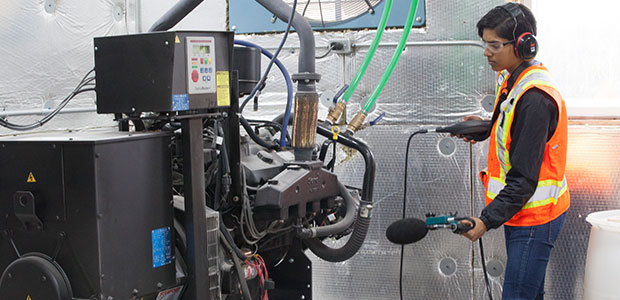
Three Basic Methods: Workplace Noise Control
Managing noise exposure is complex in terms of accurately assessing sound levels, identifying and ranking the dominant noise sources, and finding effective control solutions.
- By Rob Stevens
- Dec 02, 2019
Noise-induced hearing loss is a prevalent workplace injury in the modern industrial plant. Employers must manage workplace noise exposure. Doing so is complex in terms of accurately assessing sound levels and noise exposure in the workplace, identifying and ranking the dominant noise sources to be targeted for mitigation, and finding practicable, effective, and affordable noise control solutions.
Many aspects of acoustics and noise control are counterintuitive, and there is a great deal of myth and misinformation cluttering the common knowledge about noise. But there is a “convenient truth” we can use to cut through the confusion. Quite simply, there are really only a few ways to reduce noise indoors. All workplace noise control measures are really just variations of the three basic methods, which are:
1. Reduce the amount of sound that is produced by a given process, operation or activity.
2. Block, or contain-and-dissipate the sound.
3. Reduce excessive room reverberation.
That’s it. Three options. A bit of explanation will make this clear.
Some Important Basics of Acoustics
The reason that all indoor noise control measures fall into just three broad categories arises from the core fact of acoustics that there are fundamentally just four factors that determine the sound level at a given location indoors: the sound emission levels of the sound sources in the room; any physical measures that may impede or dissipate the sound as it propagates from the sources to the locations of interest; the distances from the sources to the locations of interest; and the amount of reverberation. (Reverberation is the tendency of sound to linger, and it occurs as a result of the sound bouncing around inside an enclosed space, reflecting and re-reflecting off of the many room surfaces. Excessive reverberation in a room increases the amount of noise by allowing the sound to build up in a cumulative fashion.)
Assuming that the distances generally cannot be changed between the sound sources and worker locations, the other three factors correspond to the three categories of noise control measures.
For reasons we will cover in the following sections, reducing the amount of sound that is produced by a given process or operation is the most effective noise control method, but is often also the most difficult to implement. Blocking or containing-and-dissipating the sound is the next most effective noise control method, and covers all of the most commonly used methods. Reducing room reverberation is only effective in a very limited number of cases.
Reducing the Amount of Sound Produced
When a way can be found to reduce or eliminate the sound that is generated by a particular manufacturing processes, doing so is typically the most effective solution.
Some manufacturing methods are inherently noisy when, in fact, there may be a quieter method of achieving the same production task. For example, it is common to use compressed air to guide components around turns in moving conveyors to prevent jams. It is also common to use rotating/vibrating hoppers to orient lightweight parts before they are fed into a processing unit. The intense “hiss” of compressed air, and the tumbling of parts in a hopper, can create levels greatly exceeding workplace noise exposure limits.
While this sound can be challenging to mitigate, there can be simple solutions by finding alternative conveying or sorting methods. Similarly, some machine surfaces such as lightweight sheet metal safety guards can act like a loudspeaker and efficiently turn the silent vibrations of a machine into high level sound, via panel radiation. If those lightweight solid panels can be replaced with perforated panels, they become inefficient at moving air, and thus do not convert vibratory energy into acoustic energy.
Often, there are no quieter alternative methods available to accomplish the production task, particularly in the cases of machining methods, or the intricate processing steps in the production of pharmaceuticals, petrochemicals, micro-components, etc.
In the few cases where it is feasible to reduce the at-source noise generation, the solution needs to be a collaborative effort between the process engineering team and the noise consultant. And, in many cases, reducing the noise generated at the source is just not practicable.
Reverberation Control with Acoustical Absorption
Reducing reverberation is another method that is, unfortunately, only effective in a relatively small number of cases. Nevertheless, it is important to understand the benefits and limits of using acoustically absorptive materials to reduce reverberation.
When sound is released into any enclosed space, such as a room or the interior of a machine enclosure, those sound waves will continue to travel around inside the space until they are absorbed through successive reflections off of the interior surfaces. If the interior surfaces are primarily reflective, the acoustic energy will accumulate and the resulting sound levels will be greater—sometimes much greater—than if the same amount of sound were released into an unenclosed space or one with adequate acoustical absorption.
When this build-up of sound occurs in a room, it is termed “reverberation.” If the surface finishes in a room do not provide adequate acoustical absorption, the reverberation can be excessive, which can adversely elevate the sound levels within. Similarly, if there is little or no acoustical absorption inside a machine enclosure, the interior sound levels will escalate until the point at which the amount of sound transmitted through the enclosure walls approaches the amount of sound emitted from the sources within, such that the enclosure will provide minimal sound containment.
Therefore, acoustical absorption is an important element in noise control. If an enclosure around a machine is to serve as an acoustical enclosure, it must include some interior acoustical absorption to dissipate the contained sound; otherwise, it will be ineffective.
While acoustical absorption is important in controlling reverberation, there is often already an adequate degree of naturally occurring acoustical absorption in many rooms such as room furnishings, ceiling tiles, and occupants themselves— which may already afford appreciable absorption. In those cases, there is minimal incremental benefit from adding additional absorption, such as suspended acoustical baffles, fiberglass or foam wall panels, or spray-on fibrous ceiling insulation.
Moreover, it is important to understand that the total sound level impinging on a worker’s ear is composed of two parts—the direct sound and the reverberant sound. The direct portion of the sound is affected only by the loudness of the source(s), the distance between the source and the worker, and anything obstructing the travel of sound from the source to the worker. The reverberant sound is affected by the geometry of the room and the amount of acoustical absorption.
At workstations close to a sound source, the direct component of the sound is usually much greater than the reverberant component, such that a reduction of reverberant sound will have little to no effect on the total sound level. Thus, in a majority of cases, controlling reverberation will only reduce the sound levels in areas far away from the production equipment—typically locations where workers are rarely present. Experience shows that the use of absorptive treatments to reduce room reverberation is rarely an acoustically effective or cost-effective solution in the workplace.
Blocking or Containing and Dissipating the Sound
By a considerable margin, the noise control measures with the widest applicability in the industrial workplace environment is engineered noise control hardware. There are many types, but in essence they are all examples of blocking the sound, or containing and absorbing it. The following sections cover the most common, tried-and-true noise control methods.
Noise Barriers and Acoustical Enclosures. Noise barriers, usually in the form of a noise wall or other obstruction, block the sound, creating an “acoustical shadow” for a protected area. In contrast to a full acoustical enclosure, a noise barrier is typically open on top, or on one or more sides. Although noise barriers are effective outdoors, they usually have minimal benefit indoors because of reverberation or discrete acoustical reflections (e.g., from the ceiling).
Some amount of sound always diffracts over the top or around the open sides of the barrier. Therefore, full acoustical enclosures are generally the most common and effective noise control measure in the manufacturing environment.
An acoustical enclosure functions by effectively containing the sound and then dissipating it by absorption. In order to contain the sound, the enclosure walls must be air-impervious and have sufficient mass (depending on the magnitude and frequency of the sound being contained).
Any openings in the enclosure—e.g., to allow ingress and egress of product or ventilation/cooling air—must be fitted with silencers or acoustically lined passages. Otherwise, any joints, gaps or cracks must be sealed air-tight. Even a small unsilenced gap or opening can dramatically degrade the containment of the sound.
In some cases, items of equipment targeted for noise control already have integral enclosures for safety or product quality reasons. However, because of openings or gaps, and absence of interior acoustical absorption, they do not naturally afford appreciable acoustical benefit. Sometimes these enclosures can be upgraded to function as effective noise control measures by sealing gaps, providing interior absorption, and devising silenced openings for ingress/ egress of product materials and cooling air.
Acoustical Lagging. For pipes and vessels, acoustical “lagging” (wrapping) is a common noise control method, as it can be less cumbersome than a full acoustical enclosure. In essence, acoustical lagging is simply an acoustical enclosure that is supported on the surface of the noise source itself. It consists of one or more layers of fibrous or porous material, potentially one or more intermediate limp, air-impervious barrier layers, and a heavy air-impervious outer jacket.
The most common jacket material consists of a protective aluminum or stainless-steel cladding, with limp mass-loaded vinyl laminated to the back side, facing the insulation, and is available from noise control suppliers. For complex shaped equipment, there are mastic products available for the outer jacket, which can be trowel applied over the insulation layer, and which then cure in place. The fibrous or porous layers provide acoustical absorption, but also act as a resilient support for the outer sound containing jacket in order to partially decouple it from the vibrating surface of the pipe or vessel.
It is important to note that the maximum noise reduction possible from acoustical lagging is less than that of a fully decoupled acoustical enclosure because of the contact between the surface of the noise source and the outer jacket. Additionally, while acoustical lagging is effective for high frequency noise, in the 500 to 5000 Hz range, it tends to amplify sound at low frequencies and is therefore unsuitable for sources that produce appreciable low-frequency noise.
Silencers and Acoustical Louvres. A silencer is a common and effective noise control measure which allows flow-through of air or other gases but which removes some portion of the acoustic energy from the gas flow which passes through it. Silencers can be fitted on the intake or outlet of a fan, or in a ventilation opening in an enclosure.
All silencers will constrict the airflow to some degree, resulting in additional backpressure to the flow path. Typically, the additional backpressure increases with increasing acoustical attenuation, so the acoustical performance must be balanced against the allowable incremental backpressure that the system can accommodate. The additional backpressure can generally be minimized by using silencers with greater cross-sectional dimensions and/or length, if the available space allows.
Concluding Summary
The best noise control solution always depends on the specifics of the noisy equipment, the setting in which it is located, and the way that workers need to interact with the production processes. In most situations, a combination of the methods discussed above is necessary. The key to resolving an existing noise issue—or preventing one at the design stage—is to identify the dominant noise sources and transmission paths, rank them in terms of significance in contributing to the overall sound levels in the work environment, and select the best combination of engineered noise control solutions based on an understanding of the fundamentals of acoustics outlined above.
This article originally appeared in the November/December 2019 issue of Occupational Health & Safety.